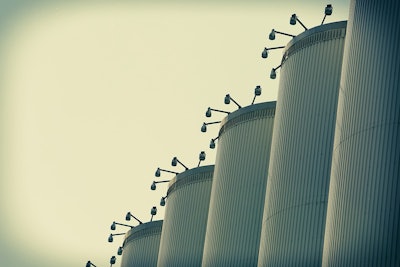
Storing and handling large volumes of grain carries risks to your employees. Increased storage capacities, larger and faster handling capacities, and automation contribute to many potentially hazardous situations during the storing of grain — and employees need to be aware of the inherent risks.
“The greatest challenge — and most important aspect — in keeping workers safe is establishing a safety culture in the workplace that views a task as complete only if it was done safely,” says Jess McCluer, vice president, Safety and Regulatory Affairs with NGFA. “A successful safety culture is one in which workers do not even consider completing a task any other way, except for safely.”
Human error or the willingness to take a chance in order to save time leads to most of the incidents, says McCluer.
“Many companies have safety programs that address the hazards associated with bin entry as well as the equipment necessary to complete the job safely,” he explains. “But motivating employees to work safely and to follow the safety procedures in place only go so far.”
The employee mindset about what constitutes a complete job is what matters most. “If the job is completed any other way than besides safely, the job was completed incorrectly,” notes McCluer.
Grain storage hazards
There are several hazards associated with grain storage bins, but the two most common are engulfment and entanglements.
Engulfment: As grain flows downward toward an open sump it forms a funnel. The pull of the funnel quickly draws a person down, entrapping them. An adult can be engulfed by flowing grain within one minute.
Entanglements: Grain augers are one of the most dangerous pieces of equipment that your employees will work around. The primary danger in operating an auger is getting caught in a moving part, such as the flighting or power-take-off.
“Engulfments and entanglements have one thing in common — they happen quickly,” says McCluer. “The newest employees and the most seasoned employees are the most susceptible to bin hazards due to one group being ignorant to the hazards and the other being too comfortable with them.
“The most effective safety cultures would treat both new and seasoned employees with the same seriousness when it comes to safety procedures,” he adds.
Entanglement hazards
Mechanical equipment within grain storage structures, such as augers and conveyors, present serious entanglement and amputation hazards. Workers can easily get limbs caught in improperly guarded moving parts. Equipment used to fill and discharge grain storage structures needs to be properly guarded to prevent this.
Bin Sweep Augers: OSHA’s sweep auger policy memo states that employees are allowed to be physically inside a bin with an energized sweep auger provided:
- The only unguarded portion of the auger is in the front
- Sub-floor augers are guarded by secure grates or other guards
- There is an engineering control (such as a standard guardrail attached to the auger, a portable guard rail trailing seven feet behind the auger, or a dead-man switch on an operating control inside an enclosure or attached to a handle that keeps the employee seven feet back from the auger)
- The facility’s bin-entry permit procedures are followed
Sub-Floor and Other Reclaim Augers: Sub-floor augers are to be locked out while an entrant is inside a bin, unless it is guarded and secured in such a way that removes the possibility of an employee coming into contact with its moving parts. OSHA’s 1910.217 Subpart O provides guidelines for addressing other types of augers (such as semi-exposed sloped floor, mobile bin and truck-fill augers).
Belt and Chain/Paddle Drag Conveyors: These systems can be used as a fill or reclaim system. As a fill system, they should be included in the facility’s lockout/tagout program for bin entry since they have the potential to create hazardous conditions for workers when inside a bin. When these conveyances are used for reclaiming purposes, the same sub-floor guarding principles described above also apply.
Power Takeoff (PTO) Shafts: PTOs, unless properly guarded, can create wrapping hazards. These hazards could be caused by the joint, burrs or the air current formed by the rotation. To mitigate the hazard, install shaft guards that entirety cover the moving parts.
Workers should never step over a rotating shaft or operate controls from outside of the machine, never wear loose-fitting clothing, jewelry or hair, and stay clear of rotating PTO shafts.
For more safety tips, visit ngfa.org/safety. ■
Toolbox Talk: Lockout/Tagout
Lockout/Tagout (LOTO) is used during bin entry to disconnect power sources to the unloading and conveying equipment of the bin. LOTO before entry protects entrants from engulfment and entanglement hazards associated with flowing grain, unloading augers and sweep augers.
LOTO all unloading equipment prior to bin entry. Other preventive measures to take during bin entry include:
- Always have an observer positioned outside the bin.
- Guard sump holes upon entering if permanent guards are not in place.
- Use a lifeline to prevent being engulfed more than waist deep.
Some questions to ask employees during your Toolbox Talk on LOTO:
- What are LOTO procedures our workers are supposed to use prior to bin entry?
- Who is responsible for ensuring LOTO is performed? How does an entrant ensure LOTO has been done prior to entry?
- How do we protect each person involved in the bin entry process with LOTO?
Information provided by the Grain Handling Safety Coalition. For more information, visit grainsafety.org.