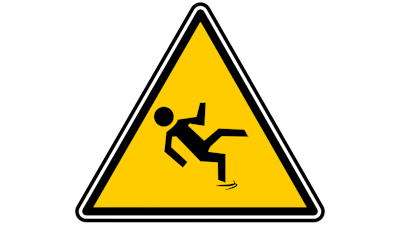
Slips, trips and falls represent a persistent safety challenge for grain storage facility operators. These incidents generate thousands of workplace injuries annually, resulting in significant productivity losses, elevated insurance premiums and serious consequences for affected workers.
Grain handling and storage environments create distinct hazard profiles that demand specific prevention approaches. Dust accumulation, variable weather exposure and intricate equipment configurations establish risk conditions requiring targeted safety measures. Occupational Safety and Health Administration (OSHA) regulations address these particular dangers through specific slip, trip and fall requirements, establishing both safety imperatives and legal obligations for facility operators.
Grain facilities combine multiple hazard sources that position slips, trips, and falls among the primary causes of workplace injuries. Risk identification forms the foundation for developing effective prevention strategies.
Common causes of slips, trips, and falls
Grain storage facility environments generate multiple accident scenarios. Slips occur when workers lose footing on wet, muddy, greasy or oily surfaces. Grain transfer operations frequently create these conditions through spilled product accumulation.
Trips result from obstructions that catch workers' feet, causing forward stumbling. Standard trip hazards include:
- Extension cords and air hoses positioned across walkways
- Tools and equipment components scattered on work surfaces
- Floor mats with raised or curled edges
- Uneven walking areas with elevation changes as minimal as 3/8-inch
Falls occur across any surface and elevation, with height-related incidents carrying particular severity. Workers fall 4 feet within 1/2 second and 16 feet in one second, providing minimal reaction time for protective measures.
Why grain storage environments are high-risk
Grain storage operations present elevated accident potential relative to standard industrial workplaces. Multiple environmental factors contribute to increased hazard levels:
- Required climbing, narrow catwalk navigation, and work activities at elevations between 22 and 108 feet
- Dust accumulation producing slippery surfaces and reduced visibility
- Variable operational conditions during grain movement processes
- Seasonal wet or frozen surface conditions
- Limited lighting within enclosed storage structures
Large equipment proximity compounds injury risks through potential blunt trauma, sprains, strains and entanglement incidents.
OSHA definitions and classifications
OSHA addresses slips, trips and falls through Subpart D, "Walking-Working Surfaces," applicable to general industry facilities including grain operations. OSHA identifies potential fall locations throughout grain handling facilities as floors, machinery, roofs, unguarded openings, ladders, catwalks and platforms.
Fall protection requirements apply at open elevations of 4 feet or higher and above dangerous equipment and machinery. Walking-working surface regulations mandate clean and dry conditions, prohibiting aisle obstructions that create hazard potential.
OSHA standards classify quarter-inch floor level variations as tripping hazards, demonstrating how minor surface irregularities can produce serious accident consequences.
Key Hazards to Watch For
Specific hazard identification enables targeted safety measures in grain storage facilities. Focus safety efforts on these primary danger areas for maximum protection effectiveness.
Wet or dusty walking surfaces
Spilled grain creates immediate slip hazards, particularly when mixed with mud, grease or oil. Weather conditions compound these risks - rain, snow and ice produce exceptionally slippery surfaces. Grain dust presents dual dangers: slick walking conditions and explosive potential when ignited.
Unsecured ladders and platforms
Daily operations require frequent access to loading platforms, catwalks and maintenance areas. Painted ladder rungs create slip hazards; grip tape application or rough-surface ladder replacement reduces this risk.
Obstructed or uneven walkways
Trip hazards occur frequently around grain facilities:
- Electrical cords and cables on ground surfaces
- Scattered tools and equipment parts on floors
- Uneven surfaces with depressions or irregular steps
- Protruding objects and surface irregularities
Minor irregularities pose significant risks - OSHA considers a quarter-inch change in floor level a tripping hazard.
Improper footwear and PPE
Footwear selection directly affects worker safety. Grain facility shoes require adequate traction, support and protection. Replace worn boot treads promptly, and select footwear with defined heels for ladder climbing stability. Nonslip soles remain essential for slip, trip and fall prevention.
Poor lighting and visibility
Insufficient illumination increases accident probability. Proper lighting requirements cover walkways, aisles and work areas. Strategic lighting supports both safety and operational efficiency, especially during early morning or late evening operations. Emergency lighting with reliable battery backup requires placement in critical areas and regular testing.
Proven Methods for Preventing Slips, Trips, and Falls
Effective safety measures significantly reduce accident risks in grain storage facilities. These proven prevention methods establish safer work environments while ensuring regulatory compliance.
1. Maintain clean and dry floors
Floor maintenance serves as the primary defense against slips and falls. Clean spilled grain, water, oil and other substances immediately to eliminate slippery conditions. Establish regular cleaning schedules to prevent dust accumulation, which creates both slip hazards and fire risks. Proper cleaning techniques require sweeping from top to bottom to avoid disturbing unstable grain piles.
2. Use proper signage and hazard markings
Strategic warning signs alert workers to potential dangers. Position signs at entrances, ladders and hazardous areas to control unauthorized access. Essential signage includes:
- Warning signs for rotating augers and equipment
- "Authorized Entry Only" notifications for bins and confined spaces
- Lockout/tagout requirement reminders
- Hazardous gas warnings where appropriate
3. Install guardrails and fall protection systems
OSHA mandates fall protection for work areas 4 feet or more above ground level. Platforms and walkways require sturdy guardrails meeting OSHA strength specifications. Bin access areas need safety features including ladder cages and harness anchor points. Ladder use demands maintaining three points of contact—two hands and one foot, or two feet and one hand.
4. Conduct regular inspections and maintenance
Routine inspection schedules must cover all walking surfaces, ladders, platforms and fall protection equipment. Verify guardrail security and structural integrity. Check for rust, cracks or other damage that could compromise safety. Address minor issues immediately rather than allowing them to develop into major hazards.
5. Provide proper footwear and PPE
Non-slip footwear prevents slips effectively. Employers must supply necessary PPE at no cost to workers, including cut-resistant gloves, safety goggles, hearing protection and N95 respirators for dust protection. Current State Allotment provides $250 maximum per employee for safety-toe shoes during each biennium budget period.
6. Train workers on hazard recognition and response
Employee training must cover workplace hazard recognition and response procedures. Workers need proper lockout/tagout procedure knowledge before bin entry. All personnel should maintain alertness during work activities and avoid distractions like mobile phones that increase accident risk.
Compliance and Training for Long-Term Safety
Safety regulation compliance requires structured training programs and systematic monitoring practices across grain handling operations. Sustained safety performance relies on technical competency and organizational commitment at all levels.
OSHA regulations mandate employers provide training to employees at least annually and whenever job assignments change, exposing workers to new hazards. Training programs must address:
- General safety precautions, including recognition of dust accumulation hazards and common ignition sources
- Specific procedures for job tasks such as cleaning grinding equipment, clearing choked legs, and implementing lockout/tagout procedures
- Special training for employees assigned tasks like bin entry, focusing on engulfment and mechanical hazards
Documentation protocols require maintain certification records for each inspection containing the date, inspector's name, and equipment identifier.
Creating a culture of safety awareness
Safety culture development requires sustained commitment rather than short-term initiatives. As one industry leader notes, "It's been a 20-plus-year process in which we have taken incremental steps to get to where we are, and we still believe we have room to improve".
Successful safety cultures start with ownership and management demonstrating genuine concern for employee well-being. Safety investigations should focus on identifying systemic problems rather than assigning personal blame. This approach enables employees to assess task safety independently and halt work when conditions appear unsafe.
Using checklists and safety audits
Systematic safety inspections provide the foundation for effective hazard prevention. Written housekeeping programs should establish frequency and methods for reducing grain dust accumulations. Housekeeping inspection logs document dates, areas examined, and remarks.
Safety checklists must verify critical items:
- Equipment powered off, locked and tagged
- Oxygen levels tested where combustible gasses might be present
- Proper PPE availability and usage
- Presence of necessary warning signs
Team member involvement in inspections incorporates diverse perspectives and extends educational benefits across facilities. This systematic approach satisfies regulatory requirements while building sustainable safety frameworks.
Creating safer grain facilities through consistent vigilance
Slips, trips and falls constitute major hazards within grain storage facilities, though these incidents remain preventable through established safety measures. Regular maintenance, appropriate signage, adequate fall protection systems and proper training form the cornerstone of effective risk mitigation strategies.
Prevention demands a multifaceted approach. Clean, dry floors establish primary defense against accidents, while clear hazard markings alert workers to potential dangers. Guardrails and fall protection systems provide essential safeguards for elevated work areas. Proactive inspections identify and address hazards before accidents occur, rather than responding to incidents after they happen.
Safety commitment must extend beyond regulatory compliance requirements. Building genuine safety awareness transforms protocols from mandatory rules into embedded operational values. This shift protects workers while improving operational efficiency and reducing costs associated with workplace accidents.
Safety achievement requires ongoing vigilance rather than one-time efforts. Comprehensive training programs, regular safety audits and consistent PPE provision form the foundation of sustainable safety management. Investment in slip, trip and fall prevention generates significant returns through reduced injuries, improved morale and enhanced productivity across grain storage operations.