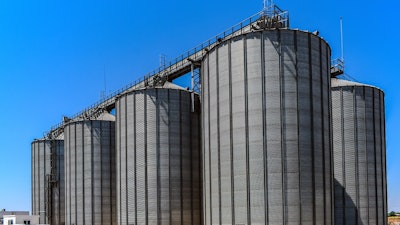
Stored grain pests become active at temperatures above 55-60°F, making winter temperature control a critical factor in pest management. Successful grain storage requires maintaining temperatures between 30-40 degrees Fahrenheit throughout the cold season.
Weekly grain monitoring protocols safeguard stored grain quality. Standard inspection schedules call for bi-weekly checks during winter months, while damaged or lower-grade grain stocks need more frequent assessment. A clean, vegetation-free zone extending 10 feet around storage bins serves as an effective barrier against pest infiltration.
Winter grain storage challenges
Winter grain storage presents distinct technical requirements due to temperature variations. The natural insulation characteristics of grain, measured at R=1 per inch, create unique temperature patterns within storage structures.
Storage duration depends heavily on temperature control. Cereal grain with 18% moisture content maintains quality for 200 days at 40°F, while storage life drops sharply to 15 days at 80°F. Storage capacity decreases by half with each 10-degree temperature rise. Storage periods at 70°F range between 30 days for 18% moisture grain and 200 days for 14% moisture cereal grain.
Laboratory research documents specific cold tolerance levels among storage pests:
- Multiple species - sawtoothed grain beetles, rusty grain beetles, hide beetles, and flour beetles - withstand 32°F exposure for 7 days
- Rice weevils exhibit poor survival rates at 32°F
- Rusty grain beetles show remarkable resilience, enduring temperatures from -4°F to -22°F
Pest adaptation capabilities merit attention. Research shows rusty grain beetles adjust their supercooling point from 2.3°F to -4°F through acclimatization.
Moisture migration risk increases when outdoor temperatures fall below 20°F. Temperature gaps exceeding 20 degrees between stored grain and ambient conditions trigger internal moisture movement. The cycle starts at bin walls as cooler air descends. This air mass moves toward the center, gathering moisture while rising. Condensation forms at the grain surface center upon contact with cooler upper zones.
These moisture patterns can raise grain moisture content substantially, creating spoilage risks through surface crusting. Winter conditions amplify these moisture migration effects compared to summer storage periods.
Advanced pest monitoring systems
Current pest detection equipment offers precision monitoring capabilities beyond standard inspection methods. Machine learning systems demonstrate 96% accuracy rates for common grain pest identification.
Modern sensor arrays and automated systems provide species identification, infestation mapping, and population assessment capabilities. Detection equipment includes:
- Visual and thermal imaging systems
- Movement detection through bioacoustic sensors
- Internal pest detection via near-infrared analysis
- Species verification through DNA barcoding
Smart wireless networks support remote monitoring operations through SmartProbe devices, recording visual data and environmental metrics. Field tests show these systems reduce pesticide applications by 74% through precise targeting.
Temperature tracking systems form essential components of pest prevention programs. Current monitoring equipment provides:
Storage facilities benefit from continuous data streams through strategically placed sensors. Temperature profile analysis reveals early pest presence through baseline deviation tracking. System protocols activate ventilation controls or alert operators when measurements indicate potential problems.
Detection equipment identifies pest presence indicators before physical evidence appears. Key monitoring parameters include:
- Temperature pattern changes indicating pest populations
- Grain quality assessment through CO2 measurement
- System algorithms process local insect behavior patterns, generating automated alert reports
Field results demonstrate monitoring system effectiveness across commercial operations. Testing programs at 13 storage facilities confirm successful implementation of online monitoring platforms. Large facilities gain particular advantages through centralized temperature monitoring across multiple storage locations.
Implementing Preventive Measures
Storage facility preparation and maintenance establish primary pest control barriers. Successful pest prevention programs combine specific grain treatments, facility sanitation protocols, and precise aeration management.
Grain conditioning requirements set quality preservation standards. Long-term corn storage demands moisture levels at 15% or below. Quality protection protocols specify thorough cleaning through gravity screens or rotary cleaners, removing damaged kernels and debris. Protective grain treatments during bin filling provide additional pest control barriers.
Storage structure cleaning protocols determine pest prevention effectiveness. Standard cleaning procedures require:
- Complete removal of residual grain from equipment and bins
- Wall, ceiling, ledge, and floor cleaning
- False floor and aeration system maintenance
- Structural repair of bin holes and cracks
- 10-foot vegetation clearance around structures
Bin preparation includes residual insecticide application 2-3 weeks before grain storage. These treatments target pest populations in difficult access areas, particularly under perforated floors.
Proper aeration equipment maintains consistent grain mass temperatures. Fan operation continues through complete cooling cycles until top grain layers reach target temperatures. Natural air drying systems complete cooling cycles within 24 hours, while standard aeration equipment requires up to seven days.
Winter storage specifications require grain temperatures between 30-40°F. Cold weather fan operation needs precise monitoring to prevent sub-30°F grain temperatures, which create unloading difficulties through frozen grain formation. Winter aeration schedules maintain temperature uniformity and prevent spoilage from moisture movement.
Grain surface leveling and spreader use optimize airflow patterns. These practices ensure even fine particle distribution and maintain consistent air movement. Fan covers prevent unwanted air circulation patterns during inactive periods.
Integrated Pest Management Strategies
Stored grain protection requires coordinated pest control methods throughout winter storage periods. Field tests confirm optimal results through combined biological, chemical, and physical control measures.
Beneficial insects provide residue-free pest management solutions. Studies document Xylocoris flavipes effectiveness against storage moths and beetles. Field observations show sustained pest suppression through multiple pest life stages, even during periods of limited prey availability.
Research validates several biological control species:
- Moth larvae control through Bracon hebetor and Venturia canescens parasitoids
- Beetle population management using Anisopteromalus calandrae
- Selective pest reduction with Theocolax elegans
Storage protection programs utilize chemical treatments when pest populations exceed biological control thresholds. Application schedules specify empty bin treatment 6-8 weeks before grain storage. Post-filling surface treatments target Indian meal moth infestations.
Organic storage protocols permit specific materials. Bacillus thuringiensis provides effective moth control without chemical residues. Emergency protocols allow phosphine fumigation under certified supervision when pest damage threatens grain value.
Non-chemical control methods offer additional pest management tools. Diatomaceous earth applications create mechanical pest control barriers through exoskeleton damage. Product specifications require uniform distribution during bin filling operations.
Temperature management programs specify cooling below 13°C to halt pest development. Heat treatment protocols maintain 120°F (49°C) for complete pest elimination.
Sealed storage systems create pest-lethal environments through oxygen reduction. Technical specifications require 1-2% oxygen levels, achieving pest mortality within 1-4 days. Organic storage facilities benefit particularly from these chemical-free control methods.
Emergency response protocols
Storage facility monitoring programs detect early pest problems, while severe infestations demand rapid intervention protocols. Standard response procedures ensure effective pest outbreak control.
Pest outbreaks present specific warning indicators requiring immediate response. Storage inspection protocols require odor evaluation, as pest activity produces distinct sweet, musty grain odors. Surface examination reveals moth-related webbing formations. Kernel inspection shows characteristic weevil damage through 'shot hole' patterns.
Field indicators of severe infestations include:
- Indian meal moth larvae create dense food fragment webbing
- Lesser grain borer populations generate grain dust accumulations
- Storage structures show surface penetration or larval presence
- Product quality suffers from odor and taste alterations
Infestation confirmation triggers specific response sequences. Technical evaluation requires probe sampling and trap monitoring procedures. Standard protocols mandate immediate action when one-quart samples show pest presence.
Technical specifications outline three response options:
- Livestock feed grade reclassification
- Market value adjustment sales
- Fumigation protocols
Winter conditions allow pest reduction through temperature exposure during grain transfer. Grain retention programs require treatment selection based on previous chemical application records.
Severe infestations exceed standard control measures, requiring certified intervention. Fumigation procedures demand specialized certification and safety equipment. Important: Safety protocols restrict fumigation operations to licensed professionals due to lethal gas hazards.
Professional fumigation specifications require:
- Documentation of management protocols
- Respiratory protection systems
- Safety procedure compliance
- Gas concentration monitoring
Post-treatment sanitation programs specify complete facility cleaning. Empty storage structures require approved insecticide applications to interior and exterior surfaces. Documentation systems track all control measures and monitoring data.
Current regulations specify fumigation certification requirements. Operating standards require private pesticide applicator licensing for fumigant purchases. Technical specifications recommend professional fumigation services for severe pest control.
Storage economics demonstrate prevention program cost advantages compared to infestation treatment expenses. Quality maintenance programs specify regular monitoring, temperature control parameters, and early intervention protocols. These technical requirements, supported by modern detection systems, ensure grain value protection throughout storage periods.