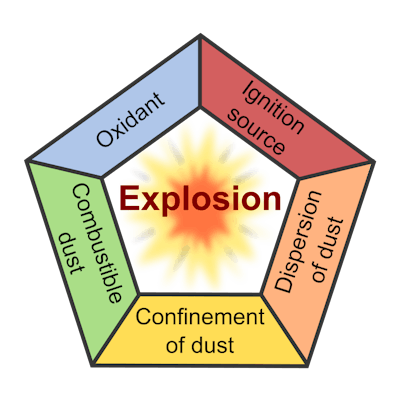
At GEAPS Exchange 2023 in Kansas City, Missouri, I had the opportunity to sit down with Bob Reis, director of commercial sales of AGI, to discuss AGI Digital’s renewed focus on grain safety education and its Roadmap to HazMon Safety.
Reis said his mission has been safety since co-founding CMC, the HazMon-in-a-Box supplier, more than two decades ago, but these days he enjoys a more active role as a provider of safety education for the grain handling industry. Read on for more of my interview with Reis at the AGI booth earlier this week.
Schafer: How do temperature sensors on material handling equipment at grain storage and processing facilities relate to safety?
Reis: It has to do with the Dust Explosion Pentagon, the five elements needed for an explosion: air, dust, dispersion, an enclosed area, and heat — the ignition source. Hazard monitoring is all about the prevention of that heat source and is why the government requires hazard monitoring in its OSHA 1910.272 standard.
I was at a major co-op a few weeks ago where they brought in over 200 people, and I was one of the guest speakers. In rural America, especially, it's difficult to find labor or hire seasonal help, so some people working at co-ops have no idea what hazard monitoring is or that OSHA has the authority to conduct unannounced grain facility inspections and levy stiff fines for non-compliance.
So, I conduct education about the non-profit National Fire Protection Agency (NFPA) standard because that is our gold standard. I present a matrix I created that shows the types of machines that are required to have hazard monitoring and where on the machines they’re required, so they can take and use that information at-a-glance.
Schafer: What else do you recommend grain companies do to meet OSHA’s HazMon safety standard?
Reis: OSHA can inspect any facility unannounced, so we advise our clients, whether it's a CMC system or any other brand, to conduct a visual inspection to ensure nothing is broken when they do their monthly Preventive Maintenance (PM). At a minimum, conduct an annual validation, which involves testing the sensors, testing the alarms, and having it documented.
We also provide the framework for that documentation process, so we can validate their systems with both parties’ sign-off that it was tested for compliance on this date. Then when they’re audited, they can show OSHA they’re in compliance. Again, that should be done with any HazMon system, and this process is not only critical for safety, but also prepares our clients for what is expected during an audit.
Schafer: Can hazard monitoring systems data be used to take grain facilities from a preventive maintenance to a predictive maintenance model?
Reis: Right now, we’re focusing on what started CMC, which is safety. Here at GEAPS Exchange, we’re talking about our safety education and services with everyone, but today’s top bearing manufacturers have great predictive maintenance profiles.
ABB and Dodge said in their presentations at this year's GEAPS Exchange that in terms of predictive maintenance, the grain industry is behind other industries, such as auto. That's going to come in the future, but we have a long way to go to catch up with other industries.
Schafer: Why has the grain handling industry struggled to adapt to technological advancements that could enhance safety?
Reis: Safety isn’t about technology; It’s about company culture. I believe labor is a big part of this challenge because if you have high turnover, you must constantly reiterate the message. That’s why grain safety education and outreach is a priority for AGI Digital.
I co-founded CMC USA in 2010 before it was AGI Digital, and immediately our mission in the industry was about protecting human life and property. It may sound clichéd, but we believed it, and it was interwoven through our culture from the shop floor to the office to our salespeople.
This led us to develop a process called the Roadmap to HazMon Safety, which differentiated ourselves as a hazard monitoring provider that also leveraged our knowledge of grain facilities and HazMon technology to provide education and foster the customer’s safety culture.
My role has become an ambassador to the industry, focusing on training our clients’ employees about how fires start and can cause explosions. We have different agendas for different types of trainings, an hour-long safety training and a more in-depth technical hands-on training for the classroom.
Then, with the foundation of a strong safety culture, adapting to digital technology that contributes to worker safety will follow.