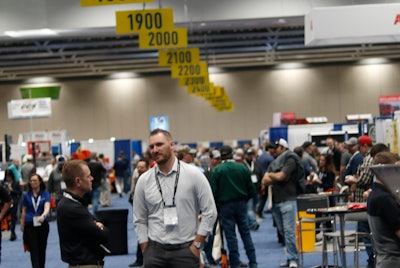
The commercial grain handling industry is seeking innovative solutions to enhance productivity, reduce costs and minimize environmental impact. The 2024 GEAPS Exchange introduced attendees to a number of new technologies addressing these challenges through its Idea Exchange, exhibitor demonstrations on the Expo floor and educational tracks.
Attendees from 45 states, 23 nations and nearly 1,000 companies gathered at the Kansas City Convention Center in Kansas City, Missouri from February 24-27 to learn about the latest innovations, products, equipment and services the commercial grain industry has to offer. The following three solutions showcased at GEAPS Idea Exchange feature uses for cutting-edge technology tailored for grain handling applications.
Sustainable grain drying with biomass fuel
Sunday’s Idea Exchange introduced biomass utilization as a sustainable alternative form of grain drying. Biomass is derived from plants or animals and can be burned to produce bioenergy. Biomass examples include wood pellets, wood shavings, grain screenings, straw and agricultural residues like corn stover. Biomass is also carbon-neutral, meaning the carbon emitted during combustion is offset by the carbon absorbed during the growth of the biomass source.
Unlike fossil fuels, which are non-renewable and subject to price fluctuations, biomass is abundant and renewable, offering a stable and cost-effective solution for grain drying. Studies have shown that utilizing biomass can result in cost savings of up to 80% compared to propane for grain drying.
One company providing biomass solutions for the grain handling industry is Triple Green Products. Their patented Bio Dry Air (BDA) system offers a revolutionary approach to grain drying by utilizing biomass furnaces. Since biomass combustion emits less water vapor, Triple Green Products’ BDA leads to more efficient drying processes, conserves water resources and savings on operational cost. It is compatible with any make and model of grain dryer.
For those looking to invest in biomass technology, financial assistance is available from the federal government, such as incentives offered by the Rural Energy for America Program (REAP), which provides grants and loans to support renewable energy systems and energy efficiency improvements.
The adoption of biomass technology not only offers cost savings and operational efficiency, but also aligns with the growing demand for sustainable agricultural practices.
Industrial Internet of Things streamlines facility maintenance
The role of technology has become increasingly crucial in grain handling facilities, particularly in predictive maintenance. This shift towards proactive maintenance strategies is revolutionizing how facilities optimize their operations for safety, efficiency and reliability.
The Industrial Internet of Things (IIoT) is a concept that integrates smart sensors, data analytics and connectivity to enable real-time monitoring and predictive maintenance. At GEAPS Exchange 2024 Dodge® Industrial demonstrated the value of the IIoT with its OPTIFY™ condition monitoring platform. This cloud-based system offers a user-friendly interface that is simple to implement without the need for subscriptions. Dodge's OPTIFY hardware allows grain handling facilities to integrate predictive maintenance into their operations within minutes.
OPTIFY consists of a range of products tailored to the needs of grain handling facilities. The wireless sensors, introduced in 2019, feature enhanced temperature measurement capabilities and the Intelli-Lube™ product focuses on optimizing bearings through wireless connectivity for precise control over lubrication processes. The platform’s ability to remotely monitor equipment and avoid hazardous situations also enhances workplace safety.
From a productivity standpoint, the cost of downtime in the grain industry can range from thousands to hundreds of thousands of dollars per hour. Predictive maintenance programs prevent unplanned downtime and optimize equipment performance. By reducing downtime, improving reliability, and enhancing safety, predictive maintenance helps ensure operational continuity and profitability.
Advanced material flow sensors increase accuracy
Accurate measurement of material flow rates and weights is fundamental in grain handling operations to optimize processes, reduce waste and enhance productivity. The CADARO Veracity and Integral flow sensors aim to revolutionize how grain handling facilities tackle measurement challenges.
The Veracity flow sensors are engineered for vertical material handling installations, capable of measuring up to 5,000 pounds per minute or 5,000 bushels per hour. With patented technology, these sensors increase operational transparency with real-time insights into flow rates and weight measurements.
The Integral flow sensors are tailored for incline installations, providing flow rate and weight measurements with typical accuracy within +/-1%. Designed for dry flowable materials like seed, grain, and minerals, these sensors can handle a broad range of flow rates, making them versatile solutions for various grain handling applications. Their touchscreen PLC controller allows for easy placement and data capture at the plant operator or enterprise level.
The value proposition of these sensors for customers includes improved efficiency in loading optimization, enhanced inventory management, seamless data integration and overall productivity gains. Enabling accurate measurement with sensors paves the way for automation, according to Dale Vinsand of Landus, who shared his experience as an early adopter of the technology at its Mitchellville, Iowa, facility.
Landus's partnership with CADARO was instrumental in overcoming measurement hurdles with the integration of Veracity and Integral flow sensors, Vinsand said they’ve revolutionized their loadout processes and achieved precise loading within 1% of target weights — minimizing overloads and optimizing freight logistics.
Accurate measurement is a cornerstone of efficient grain operations, and advanced sensors like CADARO's are poised to redefine what’s achievable in terms of material flow precision.