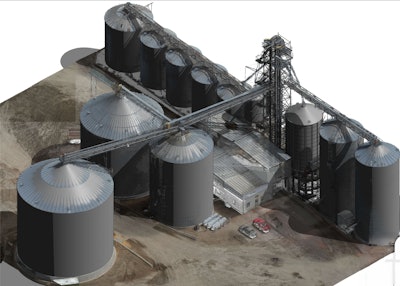
For a recent Feed & Grain Chat, I interviewed Dan Starr, partner/owner of ScanStar LLC, a digital scanning design consulting firm for architectural, civil and structural engineering, specializing in agriculture.
Starr joined me live from a job site in Montana, where he was analyzing a fertilizer plant in need of foundation repair. His fascinating description of the work involved using high-definition scanning devices to create a point cloud and a digital twin of the location. A digital twin is a virtual model, or exact counterpart, of a physical object or space.
“Here at this facility, we’re scanning it to analyze the foundation because they found it's sinking in certain areas,” he said. “We’re going to recreate the slab of this fertilizer plant, so the concrete contractor has enough information to raise it back up where it's supposed to be.”
Digital twins can also be generated for Greenfield sites in the planning phase. Starr likened a digital twin to the project book facility design and engineering contractors typically provide to clients. The software that creates the virtual model stores all the same vital data, like equipment specifications and locations, approval drawings, and process and material flow plans.
“It’s the complete informational package of your facility so there's more to reference in a full digital twin than what you can see in just a point cloud,” he said.
Once a digital twin is created, Starr said “it lives forever,” and can benefit facility owners and their contractors throughout the facility’s lifespan. For existing facilities, creating a digital twin not only helps repair damage, like the fertilizer plant’s foundation, but can also create new processing lines, modify existing ones, or model the addition of storage bins or other structures. Starr said one advantage in this case is eliminating the risk of manual measurement errors that could cost extra to correct.
When asked how high-definition digital scans can be used beyond creating point clouds and digital twins, Starr said, “Some grain facilities are antiquated, and concrete has a half-life; It degrades. Loading and unloading bins can cause stress on the walls, so analyzing these structures could lessen risk for potential buyers and insurance companies.”
Starr predicted that conducting ground penetrating radar (GPR) scans before companies acquire or purchase a facility will become more prevalent with prospective buyers and insurance companies because it can reveal hidden structural problems or prevent the loss of assets.
Watch Tape measures to digital twins: Scanning tools’ evolution [Video] to learn about enhancing safety and data accuracy with the latest digital structural scanning technologies.