During Wednesday's GEAPS Exchange Online Conference, Joe Mlynek, partner, subject matter expert with Safety Made Simple, gave an update on the Walking- Working Surface Standard.
The standard, which was 26 years in the making, went into effect on January 17, 2017.
Most employer requirements have passed, and the standard only has one final implementation date on November 18, 2036, which is designed to replace cages and wells used as fall protection with ladder safety or personal fall arrest systems on all fixed ladders over 24 feet.
“I would encourage you to start working on these final requirements now,” says Mlynek. “Don’t wait for the last minute to do a mass installation of this equipment.”
What do you need to look for on your ladders?
- Must be capable of supporting maximum intended load
- Inspect before initial use during work shift to identify defects
- If a defect is found, use a “Danger: Do Not Use”
According to standard, ladders should be inspected each time they’re used.
“You don’t need to document it, but they are required to be inspected prior to each use,” says Mlynek.
How do you prove an inspection took place? “A compliance officer could ask employees if they inspect ladders prior to use, and if they answer ‘no,’ there could be a fine,” he says.
“I would recommend addressing this issue during training – that ladders should be inspected prior to use,” says Mlynek. “And consider documenting inspections as part of JSA process.”
What to look for on a fixed ladder
When inspecting a fixed ladder, what should you be looking for?
- Capable of supporting intended load
- Minimum perpendicular distance from centerline of rungs to nearest permanent object in back of ladder is 7 inches
- Side rails of through or sidestep ladders must extend 42 inches above top of access level or landing platform
- Grab bars extend 42 inches above access level or landing platform
- Ensure ladder rungs, steps and cleats are parallel, level and uniformly spaced when the ladder is in a position of use
- Ladder rungs and cleats are spaced not less than 10 inches and not more than 14 inches apart
- Ladder rungs and cleats must have a minimum clear width of 16 inches
- Metal ladders made with corrosion-resistant material or protected against corrosion
- Ladder surfaces are free of puncture and laceration hazards
The final rule phased in requirements to equipment fixed ladders which extend over 24 feet with ladder safety or personal fall arrest systems.
“This rule prohibits the use of cages as a means of fall protection after the 20-year phase-in period,” says Mlynek.
Ladder safety systems
Ladders safety systems must be designed to reduce the possibility of falling from a ladder. The system must consist of a carrier, safety sleeve, lanyard connector and body harness.
These systems must:
- Allow employees to climb up and down using both hands and not require employees to continuously hold, push or pull any part of the system while climbing
- Feature a connection between the carrier and lifeline and point of attachment to body harness does not exceed 9 inches
- Be capable of withstanding without failure a drop test consisting of an 18-inch drop of a 500-pound weight
Employers must ensure that single or multiple-section ladders have personal fall arrest systems or ladder safety systems provided throughout the entire vertical distance of the ladder, including all ladder sections. They must also ensure the ladder has rest platforms provided at maximum intervals of 150 feet.
OSHA has revised and now defined ladder landing platforms as walking and working surfaces.
In the definition, OSHA notes “any horizontal or vertical surface on or through which an employee walks, works or gain access to a work area or workplace location.”
Related to platforms, under the revised standard, employers are therefore required to “ensure each employee is protected from falling into a ladderway floor hole or ladderway platform hole by a guardrail system and toeboards erected on all sides, except at the entrance to the hole where a self-closing gate or an offset must be used.”
Compliance suggestions
Mlynek offered a few suggestions in order to be in compliance with the ladder standards.
- Compile an inventory of all fixed ladders
- Assign an identification number/code to each ladder
- Indicate height and type of fall protection system in place (if applicable)
- Develop deadlines for addressing fall protection requirements based on the final phase-in period
Mylnek notes that Emergency Use Ladders should be labelled as such and only used for that intended purpose, noting that employees need to be trained to only use them for their appropriate designation.
Staying safe on ladders
Here are some tips for staying safe while using a ladder:
- Use for purpose intended – users should face the ladder when climbing up and down
- Use as least one handle when climbing
- Do not carry any object or load that could cause loss of balance when climbing. “This is the number one reason for falls and fatalities involving ladders,” says Mlynek.
Additional resources
OSHA for FAQs, regulatory text, fact sheets and letters of interpretation
NGFA Guidance
For the full educational session, click here. GEAPS Exchange Education Sessions will be available online for 30 days and can be viewed with a registration.
SPEAKER
Joe Mlynek
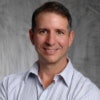
Joe Mlynek, partner, Safety Made Simple, LLC has a degree in Environmental Policy and Analysis. Joe began his safety career in 1996 and has since worked in the grain handling, milling, insurance, construction, manufacturing and maritime industries. Mlynek holds certifications as a Certified Safety Professional (CSP) and an Occupational Health and Safety Technician (OHST) through the Bureau of Certified Safety Professionals. He is also an active member of the National Grain and Feed Association, Grain Elevator and Processing Society, Ohio Risk Coordinators, National Fire Protection Association, and American Society of Safety Professionals.