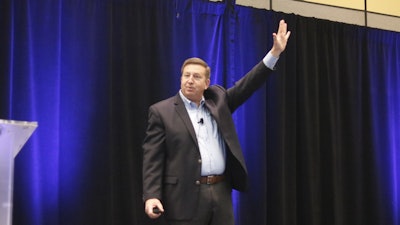
In today's rapidly evolving industrial landscape, plant managers and reliability engineers often find themselves bombarded with the demand to integrate digital solutions into their maintenance programs. That was the message from Kevin Walker, product manager — IIOT Products at Dodge Industrial Company, Inc. during his presentation at the Grain Elevator and Processing Society's (GEAPS) 2024 Exchange. He notes that many digital initiatives end up being half-finished or partially implemented, leading to a lack of measurable success. To ensure long-term success, there are three critical requirements that need to be considered when adding digital solutions to any maintenance program. Walker listed three requirements and provide valuable insights into deploying, implementing, and maximizing low-cost wireless sensors to drive lower maintenance costs.
Requirement one: local champion
To kickstart the deployment of low-cost wireless sensors, it is crucial to have a local champion who can spearhead the initiative. This individual should possess in-depth knowledge of the factory or plant, including the location of equipment and problem assets. The local champion should also have a good understanding of the previous maintenance issues faced by the facility and be open to trying new technologies. This person will play a vital role in ensuring the success of the IoT program by cooperating with the sensor providers, monitoring the alerts and alarms, and communicating with the support team. Having a local champion who is invested in the success of the program is essential for driving positive outcomes and achieving long-term maintenance cost savings.
Requirement two: dialed-in alerts and alarms
Accurate and well-defined alerts and alarms are crucial for the effective implementation of low-cost wireless sensors. These notifications ensure that maintenance personnel are promptly notified when there is a problem with the equipment or system being monitored. By receiving immediate alerts, maintenance teams can quickly address issues and prevent costly breakdowns or failures. The alerts and alarms should be tailored to the specific key performance indicators being monitored, such as temperature, vibration, speed, current, or pressure. They should provide the necessary information, including the asset name, geographical location, date and timestamp of the alert, and the specific performance indicator that triggered the alarm. By dialing in the alerts and alarms, maintenance teams can save time and resources by focusing their efforts on the most critical issues.
Requirement three: robust back-end support
To ensure the smooth operation of an IoT program, robust back-end support is essential. This support should be local or within a close time zone, enabling easy communication and quick response times. The support team should consist of experts who can address any technical issues, provide guidance on system deployment and maintenance, and assist with data extraction and integration into existing systems. It is crucial to have a reliable and accessible support network to ensure the ongoing success of the IoT program. The support team should be readily available to address any concerns, provide regular updates, and collaborate with the local champion to drive continuous improvement.