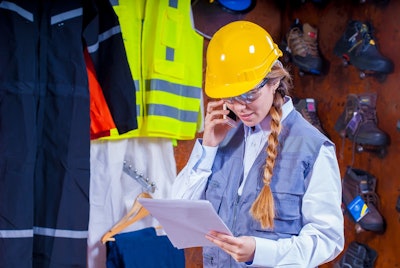
"The basics of safety are the same,” says Pete Mutschler, Environment and Safety director for CHS Inc.’ Country Operations Division. “However, we’re seeing adoption of the equipment more than we ever have.”
As someone who oversees safety services for grain facilities from Michigan to the Pacific Ocean and into Texas, Mutschler knows the importance of risk management. He says that no operator should wait for a major situation to get serious about safety.
“We have been noticing a trend in the industry of us getting comfortable with our controls,” he notes. “We’ve had a lot of fires this past year, which tells me that, even with the advances in our equipment, we might be getting a little comfortable with the risk.”
Mutschler’s solution is to make sure equipment and people are working properly at their “A game,” as he calls it. While improvements can be made in safety protocols, he adds that there are many positives in the industry today, including the innovative products on the market. Here’s a look at some of the safety products that are providing an extra level of protection to feed and grain operations around the country.
Fall and entrapment risk management
Grain entrapment and falls are not unheard of in this profession. The good news is that OSHA reports say that 82% of entrapments occur on farms and only 4% in grain facilities. New products are continually available to prevent entrapments, and the numbers speak for themselves, that they are being used, and used successfully.
Mutschler says the other area which has seen success through enhanced safety precautions every year is fall protection. He remarks that he spent the first two-thirds of his career going through facilities where he saw equipment simply hanging on the walls, never being used. “Now I walk through and I talk to employees who are all harnessed up,” he explains. “It’s very refreshing.”
Mutschler says it’s obvious to him that employees in general are more knowledgeable about their fall protection equipment, how to use it and actually are using it in their daily routines. He credits operators for getting employees to “buy into” the need for this level of precaution, making sure they are secure on railcars and trucks. “This was rare for a while,” Mutschler adds, when mentioning those working on grain and feed trucks.
He also credits the manufacturers for offering progressively better equipment, and says that companies are able to provide more comfortable and practical options when operators are providing feedback because of regular product use. It’s vital, he says, that people ask questions when buying equipment, to know what they’re getting and the quality. “You can buy a lot of really cheap equipment out there, and it won’t do you a whole lot of good if it fails,” Mutschler adds.
CHS hired a fall protection specialist about a decade ago just to learn and know the uses of that protection equipment inside and out. He was the expert in how to use it and training others. That person has since moved on and still does training for CHS operations, but another safety specialist carries on the tradition in-house as well.
Overall, Mutchler says there is more emphasis on quality harnesses, lanyards and lifelines. The equipment is much more acceptable than it used to be and that shows with fewer falls in the grain industry. “If the employee doesn’t feel secure in the piece of equipment they are wearing, they won’t wear it,” he concludes.
Technology helps with tasks
According to OSHA, in the last three and a half decades, there have been 500 explosions in grain handling facilities across the United States, which have killed more than 180 people and injured more than 675. This is an area where technology is making huge strides in insuring safety in the industry, both on the feed and grain sides.
Keary Getter, operations manager at CP Feeds in Valders, WI., is right in the middle of this trend as the company builds a new, high-tech facility in Wrightstown, WI., just a little over a half hour from the main feed mixing plan. The Wrightstown facility will be able to produce 1,500 tons of feed each day.
Getter says 99% of CP’s business is mixing feed for Wisconsin dairies, and that after 40+ years in the business, he’s seen big improvements in technology over time. “I said before I retire, I would help get this new plant up and running,” he says with a laugh. It’s expected to open in June of this year and is incorporating many new technological upgrades available today.
Temperature monitors for bearings and alignments on the elevator belt legs are just two of the hazard monitors being built into the new facility. Currently, he says there is a speed control monitor on the belts and legs, but these new measures will be a big improvement.
“All the feed mixing will be done by computers that automatically batch the product,” Getter continues to explain. “On that screen, bearing temperatures will be reported to the control room operator, and he has access to that at all times. If something is getting too high, the computer will alert us.”
Mutschler adds to this conversation by saying that for upgraded facilities, this type of equipment is a “godsend” and greatly decreases chances of equipment failure. Knowing the exact hours a machine has run and receiving a warning is much more accurate than an operator tracking this manually for so many moving parts, or relying on their best guess, or as he adds, just relying on days of operation.
“If at 500 hours you need to grease the bearings, and the computer tells you that, it’s much more likely it’s going to get done,” Mutschler notes. “Human error, human nature is just to not force yourself to always go check something.”
Getter agrees. He says he diligently keeps and updates the list of equipment due for maintenance, but is excited for the sensors that will be available come summer for the one location.
Maintenance truly matters
Speaking of maintenance, operators know that maintenance on any equipment is crucial to its long-term success. Mutschler adds that safety equipment is wonderful, if it’s used. “We’ve seen some fairly sophisticated systems that people are able to bypass,” he adds, and says over time, this practice leads to serious problems.
The newer monitoring systems don’t allow that as much, and he agrees with Getter that if a machine can catch that one small problem, it’s very likely to prevent a bigger incident. Getter says that the computer program in Wrightstown will provide detailed reports on every piece of equipment and maintenance needed based on run times. “We’re adding that too and I think it’s going to be of key importance to monitor run times,” he remarks. “That should be really helpful.”
First priority, Getter says, is controlling dust and leaks. Dust collectors, and good ones, are key for the first issue. OSHA reports that just from 2007 to 2016, there were 91 explosions attributed to grain dust in the country. Getter says this is nothing to mess with. “It’s so important to keep dust out of the air and systems, and from accumulating on equipment,” he adds. Only an eighth of an inch accumulation is enough to kick in safety regulations.
Proper maintenance protocols also help with any leaks in the pipes as they are continually used and worn out. He says it’s so vital for the operation’s success to monitor all pieces of equipment and practice prevention. Getter calls this his “housekeeping” plan, one he says has been his way of making sure everything is handled and has made for a lot fewer breakdowns than in years past.
Another way the new CP Feeds’ location is handling risk management and streamlining maintenance is through separate buildings for each of the feed mixing processes. Grinding will be in one, mixing in another and finishing/load-out also in a separate location. “It’s all isolated,” he adds. “If for some reason we would have a problem, it would be contained and not affect the whole facility.”
The risk control factor
Mutchler says that safety concerns for feed and grain operations have their ups and downs. “You can get really comfortable not having anything happen, so you can easily drop your guard,” he says. “It can happen to anyone at any time, and this equipment really helps reduce the chance of a disaster.”
When doing inspections around the country, he says a key thing he looks for is making sure operators know what products/equipment they need and when they need it. OSHA has requirements to follow, but he stresses that operators must analyze their own risk, the controls they have in place and also have a sound understanding of why they are doing these things. “If you don’t know what the equipment is there to help you prevent, then it won’t do you a whole lot of good,” this grain industry expert adds. “Anything that makes risk controls easier for the employee to follow is always a good thing.”
A good thing for employees is a good thing for operators, and in turn, the industry as a whole. This is a profession that won’t be without safety risks, but one that can produce success stories of prevention that saved lives.