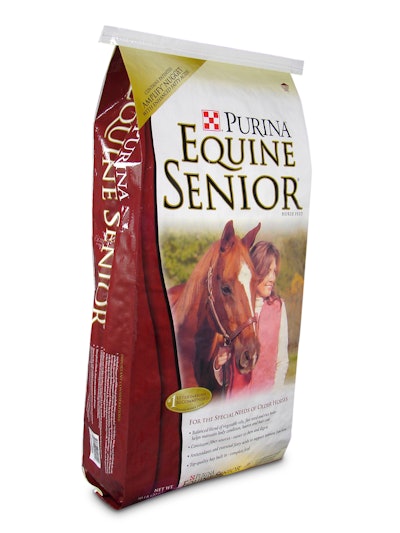
Many feed and grain packaging operations have transitioned to fully or semiautomatic bagging systems in recent years, while a smaller number continue to maintain efficient manual packaging lines. The decision to automate is not cut-and-dried, but hinges on such factors as a company’s size, product offerings, and the skill and experience of its workforce.
If your company is considering a switch to automated bagging, it’s advisable to seek assistance from your packaging equipment and industrial bag suppliers. They can offer technical support and help you make the right decision for your specific bagging application.
Manual Vs. Automated Bagging
Feed and grain products are typically packaged in 25- and 50-pound open-mouth bags that are sewn shut or heat-sealed. In most manual operations, a worker takes hold of an empty bag and positions it by hand on a filling spout. Subsequently, a second worker presents the filled bag to a sewing machine for closure.
In automated operations, a bag placer system grasps empty bags via suction and positions them automatically on the filling spout. The filled bags are then conveyed directly to a sewing station, where they are securely closed.
Automated operations reach speeds of 20 bags or more per minute, and reduce overall labor and operational costs compared with manual methods by eliminating one or more tedious, highly repetitive tasks per line. In addition, many automated systems are fully enclosed, protecting workers from any airborne dust and improving workplace air quality.
Improved product shelf appeal is another benefit. Automated systems align the filled bags precisely before closing, resulting in an attractive and consistent closure. In contrast, on manual lines workers occasionally position a bag incorrectly for closing, detracting from product appearance.
Despite the overall trend toward more automation, manual methods remain productive at some facilities. Smaller companies with skilled employees, for example, can maintain highly efficient manual operations that are the equal of most automated systems. Also, companies may be reluctant to invest in new automated systems because of the costs or prefer not to take on the learning curve associated with new equipment.
Key Issues
If you opt for greater bagging automation, there are a number of issues to keep in mind. Bag sizing is an important example. Converting to a fully automated system generally entails a change of bag size. Your bag supplier’s technical experts can help select the optimal size for your equipment.
Bag consistency is another issue. Because automated systems are less forgiving than manual methods, the bags used must have minimal size variation and be supplied in wrinkle-free condition. Otherwise, they will not mesh well with the bagging equipment. The bags also need to be palletized in a way conducive to automated operation.
In summary, the decision to automate ultimately depends on a company’s size, workforce, current operation and the cost and perceived benefits of automated bagging systems. By carefully weighing these factors, you can determine the most efficient bagging solution for your facility.