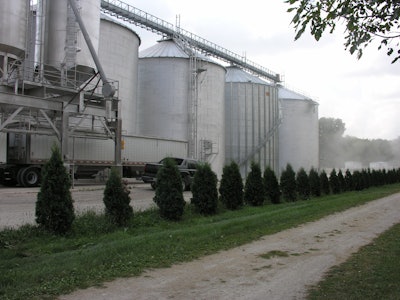
Keeping the inside of bulk storage bins and silos clean is an ongoing challenge for many feed mills and grain elevators, especially since a number of ingredients used in the feed and grain industries are prone to buildups that can impede flow and reduce storage capacity. Worse yet, a complete obstruction can shut down the system entirely.
“From a practical side, material buildup reduces flow, decreasing the ‘live’ capacity of the vessel and the overall efficiency of the bulk handling system,” says Brad Pronschinske, global product manager, Martin Engineering. “When the flow reaches a critical level or stops altogether, the system must shut down until the problems can be rectified. This often happens when the greatest demand is placed on the storage system, making unplanned downtime a key issue. In other words, accumulation problems tend to crop up when the system operator can least afford a stoppage.”
Cotton and soybean meals, wheat middlings and dried distillers grains (DDGs) can be some of the worst offenders for buildups and blockages, says Dan Bruenderman, project engineer/manager, Mole•Master Services Corp.
“The nature of these products makes them problematic because they compact,” he says. “They are like snowflakes that inherently stick together in a snowball. Also, materials in the feed industry are often ground into smaller particles, then blended together. There is greater interaction between materials, and a greater opportunity for them to stick to one another and pack in.”
Rob Duffee, contract cleaning manager, Pneumat Systems, agrees, noting that during the summer months they receive more crisis calls which are often related to wheat midds or DDGs. “However, just about any ingredient can build up,” he says, adding that the bulk of cleaning projects is actually associated with fractured ingredients. “Modifying ingredients makes them more susceptible to moisture, humidity and heat that can cause them to stick together and hang up in the bin.”
Likewise, materials with a high sugar or high moisture content can also be challenging, causing arches and plugs to completely block material flow. “Also, products that are brought in a little warm can consolidate or cake up and bridge,” says Greg Wurst, CEO, C-Tec Ag.
Even elevators and mills that handle whole grains can experience buildup issues related to dirt, chaff and fines that inevitably make their way into a storage vessel by tagging along with the grain. Since these ‘extras’ don’t have the same flow characteristics as a kernel of grain, they sift through to the bottom. “As they do that, they’ll pack in tightly,” Bruenderman says. “As you add more grain, you continue to get more fines, causing an accumulation from the bottom up. If a bin is never fully emptied, you can end up with a buildup of junk that is several feet thick.”
Grain and agricultural products are also prone to mold, rot and other contamination when accumulated material sits for long periods, endangering valuable future loads, notes Pronschinske.
Rely on the professionals
Given the long list of obstacles associated with removing material buildups and blockages, cleaning bin and silo interiors is best left to professional cleaning services.
“There are a lot of pitfalls that mill and elevator employees are faced with if they try to remove buildups or blockages themselves,” says Sam Cebula, sales and marketing manager, Pneumat Systems. “We are working on a project now where employees tried to clean a bin. They have been unsuccessful, and now one person has gotten sick in the process.”
Cebula cites heights, confined spaces and dangerous gases as just a few of the hazards. “People can also inadvertently cause a fire from sparks if they are working inside with the wrong tools,” he says. “They can also be engulfed and buried alive in overhead material that breaks loose. Every year we hear of people who are killed inside grain bins and silos trying to take care of problems.”
Pronschinske agrees. “There is a tendency for bulk handlers to try and resolve an issue themselves, thereby placing employees at risk,” he says. “Typically they do not have the proper training or tools to safely evacuate clogged silos. Conversely, commercial silo cleaning services have specialized equipment that can perform the work faster and more efficiently, without damaging the silo. By enlisting a professional service, the facility can concentrate its workforce on core business activities as well.”
Different bin cleaning companies use different tools and methods, consultation is important for determining what is best for your facilities situation. Some of that equipment can include augers and drills; high-pressure CO2, air or water tools; and hydraulically powered whips, which operate like an industrial-strength ‘weed whip’ to remove buildup by rotating flails against the material in the vessel.
“There are several different types of equipment that can be used, depending on the situation,” says Wurst.
Oftentimes that equipment can be controlled remotely, thereby eliminating the need for anyone to enter the bin or silo.
“We can either drop tools in from the top, or attack buildup or a blockage from the bottom,” says Bruenderman.
“By avoiding the need for confined space entry, employees are not exposed to the risks of accessing the vessel and attempting to clean either by poking from the bottom or hanging from a harness at the top,” adds Pronschinske.
Cebula concurs. “Safety is one of the most important things we bring to the table,” he says. “Equipment we use eliminates bin entry so we are able to clean from the outside 99.9% of the time. The remaining .01% we don’t do.”
“Safety is always top priority,” adds Wurst. “The fewer the number of bin entries, the better. We are constantly working on improving equipment that eliminates bin entry. It’s ongoing and evolving.”
What happens during the process?
Accumulations tend to take one of several forms, including arches, plugs, build ups or rat holes, says Pronschinske, who indicates whips can be effective for removing them. Technicians first clear a path for loosened material to flow out, he explains, noting the discharge opening must be clear and a takeaway mechanism — such as a conveyor, truck or end loader — should be located at the bottom to remove dislodged material. A cleaning head will typically be inserted through the access port and into the vessel on a pivoting arm. The whip is then lowered through the center of the accumulation and operated from the bottom up, with the flails dislodging material as the device is slowly raised.
“The whip uses its rotating flails to cut the material off the silo walls,” he continues. “One key to success is matching the flails to the material. Rubber-covered nylon rope has proven to work well on a variety of materials, and can be equipped with ‘knuckles’ to improve the cleaning effect and extend whip life. These knuckles are typically made of urethane to provide impact without the risk of damage or sparks. Non sparking brass chain can also be used on compacted materials where there may be the risk of fire or explosion.”
For bridged materials, Duffee explains that a bin drill would be used to create a pilot hole that allows the use of the BinWhip™. “A BinWhip™ has a tremendous amount of power,” he says. “It gets lowered into the bin top and works around the edges and walls to facilitate the cleaning process.”
Catch problems early
Many bin/silo cleaning companies estimate as many as 50% of calls are crisis calls, and while some buildups and even occasional obstructions are inevitable, scheduled cleanouts and routine inspections should be the first line of defense for managing these challenges.
“Because of some of the special types of products used in the feed industry, we recommend annual or even biannual cleaning so any problems can be addressed sooner when they are more manageable, and often less expensive,” says Wurst. “That can keep the product in better condition as well, and ultimately the operation will run more smoothly because you minimize intermittent issues. All in all, routine cleaning improves the whole operation.”
Duffee recommends that bin/silo inspections be done once a year. “That way you can see small buildups before they become a crisis,” he says.
Pronschinske agrees. “It’s important to do bin inspections and maintenance periodically, before accumulation gets too overwhelming,” he says. “That one- to two-day job can turn into a week, or more, if the silo goes for long periods without cleaning. Further, scheduling periodic cleaning during planned stoppages can save significant amounts of money and frustration by avoiding emergency calls.”
Bruenderman advises that bins are managed so they are periodically emptied for a visual inspection. “In the grain industry, that can be at the end of summer, right before harvest,” he says. “In the feed industry, it can be more difficult because bins and silos are often continually in use. They may always have some degree of material in them, but that makes it more critical to have a preventive maintenance program in place to address any issues.”
In addition to visually inspecting a storage vessel, monitoring product quality and quantity can reveal a lot about the ‘health’ status of a bin or silo.
“Guys in the field who are utilizing these bins have the insight as to what is happening inside,” says Wurst. “They know the condition of the product that is flowing out of the bin. And, they know if the amount of product coming out is less than what they put in.”
Flow monitoring is another indicator that material may be accumulating and affecting the process, says Pronschinske. “If the flow is slowing down over time, or if the flow vacillates widely, it could be a sign that material is building up and then suddenly breaking loose within the silo,” he says. “In the case of weigh bins, excess weight even after emptying would be another indicator of potential accumulation.”
“A lot of people may think of a silo or bin as a static piece of equipment that only does one thing,” adds Bruenderman. “But it is a piece of process equipment that has a life, with issues people may not think about. It isn’t simply a matter of moving product in, then moving product out.”