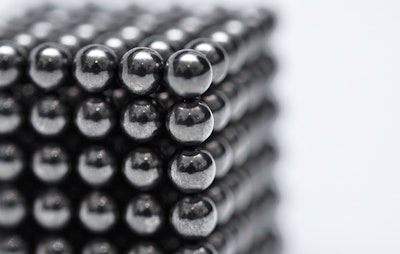
Join Steven Kilger, managing editor of Feed & Grain Magazine, as he delves deep into the world of feed manufacturing, grain handling, and related industries. In this episode, Steven is in conversation with Kyle Rhodes, vice president of business development, and Kris Tennyson, director of sales at Magnetic Products Inc. (MPI).
Together they explore the crucial role of magnets in grain and feed processing, how various magnet types are used, and the game-changing impact of intelligent magnet technology. Learn how smart magnets are revolutionizing grain and feed facilities by providing real-time data and automation, ultimately improving product quality, equipment maintenance and profitability.
Transcript has been edited for clarity.
Steven Kilger: Hi, everyone. My name is Steven Kilger. I'm the managing editor of Feed & Grain and the host of the Feed & Grain Podcast. Thank you so much for joining me today as we dive deep into the issues affecting the feed manufacturing, grain handling and all the allied industries involved.
Today, I'm speaking with Kyle Rhodes, vice president of business development, and Kris Tennyson, director of sales, both for Magnetic Products Inc., also known as MPI.
We're talking about the types of magnets used in the grain and feed industries, how they are best used to remove metal from grain and emerging technologies that can make that whole process way more efficient at the grain elevator and feed manufacturer level.
Before we start, if you're listening to this in a podcasting app. Please rate us and subscribe. If you're listening online. Make sure to sign up for the Feed & Grain newsletter, Industry Watch, to stay up to date on all the latest podcasts, along with all the news across the industry. Now onto the show ...
Hi Kyle and Kris. Thank you so much for being here.
Kyle Rhodes: Hey, how are you doing Steven?
Kilger: I am going to start by asking you to tell me and the listeners about yourself and what you do at MPI.
Rhodes: All right. Kris, you want to go first?
Kris Tennyson: My name is Kris Tennyson. I'm a director of sales at MPI. I'm in charge of the sales side of things as well as some of the customer service and some of those pieces.
Rhodes: And I am Kyle Rhodes. I'm the vice president of business development for Magnetic Products. I have a big background in sales at the company, as well as marketing and also involved now on the product development side.
Kilger: Let's get right into it. What are some of the main challenges that grain producers and processors face when it comes to grain cleaning? And how can having a good magnetic cleaning system help with those challenges?
Rhodes: Great question Steven, thank you. There's lots of types of contaminants that grain producers and processors have in their plant, metal is one of them. It can come externally from vendors or it can come internally from equipment attrition. When we look at magnetic technology, we talked about adding it in three primary areas of the plant. The goals in all of those areas can be either to keep it from breaking equipment further downstream or also ensuring the product is pure and free from metal before it leaves the facility.
The first area typically that we look at is the receiving area with which we call a primary magnet. We always say the best way to keep metal from getting into your plant and getting into your product is to keep it from coming into the facility in the first place. Having a good primary magnet at the receiving areas will help keep that metal from coming into the facility. The most common application that we see for grain producers is typically having a plate magnet mounted onto a bucket elevator.
As we move deeper into the plant, we get into the processing areas. That's where we have secondary magnets. Those are typically used to protect processing equipment from damage due to scrap metal, so magnets that are installed prior to hammermills, pellet mills, extruders, etc.
Then the last place is before packaging, and typically before any metal detector. We call those a finishing magnet. The finishing magnet should always be used to remove any fine ferrous metal or work-hardened stainless steel from the product before it goes into the package. The magnets today are so strong that they are pulling out work-hardened stainless steel. Stainless steel is not magnetic, but through attrition, you get these wear items that break off and can end up in the product as well. It could be a fine sliver, things like that.
Rare earth magnets today can pull that material from the product stream. That magnet in the finishing location should always be working at peak performance and not have a lot of metal on it. As it collects metal, it actually loses performance, it loses strength because it's holding on to that metal. We always want to keep it clean, and it should be installed prior to the metal detector to remove any metal that the metal detector may reject with good product.
Sometimes the metal that a magnet can find is smaller than the metal the metal detector can even detect, so if a preproducer or processor has installed the correct magnetic separator and maintains them in the primary, the secondary in the finishing areas, then they'll be able to prevent damage to plant equipment in ferrous metal contamination and their final product.
Kilger: You mentioned there are quite a few different kinds of magnets out there. You mentioned rare earth magnets, more traditional ones that are different formulations of grate magnets and all kinds of things. Can you go over the different types that a grain elevator or feed manufacturer might actually use within their facility?
Rhodes: Yes, there are two things there. You mentioned how I brought up rare earth. There's the magnet material. When we say rare earth, we're talking rare earth neodymium magnets. Those magnets are typically what we're using today.
A lot of older magnets, 20- to 30-plus years old, these are all permanent magnets. As long as the product in the magnet isn't wearing out from the product growing over it, the magnets are permanent and they will last forever and have their magnetic strength. Older magnets are typically ceramic. When we install a new magnet today, most of those magnets are always rare earth magnets, you get a lot more performance from a rare earth magnet, a lot higher strength. We install those into two main types of magnetic separators or magnetic circuits.
The first would be a plate magnet-style separator which comes in a bunch of different designs. We use those typically in the primary and secondary locations to remove large, medium metal. With plate magnets, product is just flowing over the magnet. What's really important when we specify those is, the deeper the product and the more the magnet has to reach out. If you have eight inches of grain going over the plate magnet, you need to make sure that magnet is reaching out eight inches into the product grain to pull that metal to its working surface conduit until it can be cleaned.
Another very common type of separator, the drawer magnets -- often referred to as great magnets or tube magnets -- those are used in finishing and sometimes the secondary applications. Those are designed to capture in all fine or very small ferrous metal. They have a very high performance contact, meaning a very high Gauss value or a pull value depending on how you're doing your measurements. They have a very limited reach out to have that high Gauss, so they have to be put directly into the product below and have direct product contact. When they are applied correctly, they are the most effective magnetic separator and therefore the best solution to ensure there's no metal in the product.
Kilger: I think it gets a little overwhelming for some people, right? When you look at a list of options that you have, for layman, we don't understand the difference between rare earth magnet or ceramic magnet and all these other ones. I think the most exciting thing you guys have is the Smart magnet technology. Can you explain what that is? What is a smart magnet?
Tennyson: Yeah, absolutely. So you might find this hard to believe, Steven, but there's not a ton of major technological advances in the world of magnets. The last one was about 20 years ago. The smart magnet, or the intelligent magnet, is really a huge thing in the magnetics world. Let me back up a little bit, let me tell you about kind of how magnets have been.
Up until now, magnets have always been dumb, they show up to work, they try hard, they do their job, but they're just dumb magnets. They don't know any better. What that means is that someone has to constantly shut down the production of a plant -- whether it's every two hours or four hours or once a day or once a shift or whatever -- shut everything down that's making money with your plant and your process to walk over and check a magnet that may or may not need to be cleaned. That's a pretty big investment for something that we don't really know if it's doing its job or not. Should it have been cleaned two hours ago? Or maybe it doesn't need to be cleaned for two more days.
That was where the invention of the intelligent magnet started. What if one of the magnets could just tell us, talk to us, that would make life so much easier. What the intelligent magnet does, or smart magnet does, is tell you when your magnet needs to be clean -- or just as importantly when it doesn't. An example is you have a vendor that loads something in your plants, you can see in real time how much metal that magnet is capturing. How much of what we call saturation, or the percentage of full, it is.
When it spikes to a certain level, then the end user gets an alert that says, "Hey, you're 30% full or you're 50% full, you're 80% full." Then you have the ability to say, "Okay, that's enough, I'm going to stop everything and check my magnet." Or in this example, "I'm going to stop the vendor from unloading because I got a whole bunch of metal with this one," or the opposite, "Hey, this one was really good, and we only got a little bit of metal. I can do a few more loads until I clean it."
As you go through the plant, this has the same benefits that Kyle talked about where we know in real time how much metal is on our magnets, so maybe I could stretch out the time in between in terms of cleaning my magnets, or maybe, I need to clean a little bit more often to protect the integrity of my equipment or protect the end product for someone.
It's also very important for data. It shows you when the magnet has been cleaned. It shows you when the magnet hasn't been cleaned. It gives you a history of those trends. It gives you immediate alerts. You know when something's happening, which is all pretty important things. We all have safety plans these days, a lot of that has some form of tracking as part of it, so this really gives you a tool for that as well.
Kilger: I imagine it would really help with diagnosing problems to this one truck you're unloading and suddenly that percentage of your magnet that has metal on it is going up suddenly. You have a bearing breakdown or something terrible like that in your equipment, and suddenly that magnet's filling up. You can actually see that information and know when it's happening rather than, "Oh well, we stopped and eight hours later, apparently it's full so something happened. Wow, that's really cool."
Rhodes: Steven, if I can just say, if the magnet is fully loaded, it's not going to capture anymore, it's reached its maximum saturation. So a metal is just going to keep going past it and going into the product going into the plant. It goes back to that main idea -- keep it from coming into the plant in the first place.
Kilger: Especially because, as we all know, that's a liability because no one likes it when metal ends up in the finished feed. You're not going to have very many happy customers after that. Are there any other specific considerations or best practices that people should use when they're implementing magnate technology? If you're upgrading now, you should at least get smart, intelligent magnets throughout your facility. It seems like a no brainer. Is there anything else that people should really be considering if they're going to upgrade or install a new system?
Tennyson: Yeah, we talk to folks about it all the time, nobody likes to eat metal. Anytime that we can get it out before that happens is good for everybody.
I would say first, it's important to get the right magnet for the application. For example, we have a presentation called, "A magnet is not just a magnet." This is an accredited presentation that we've done for 15 to 20 years, but it still holds true today. To your point earlier, Steven, there's all these options.
And yes, a magnet is better than no magnet. So that's good. Better is actually getting the right magnet for the application. Then best is getting not only the right magnet for the application, but getting it installed properly and all the T's crossed and I's dotted in the process to make sure it's exactly the right one for what you want. I will start there.
Secondly, as you already alluded to, the smart magnet technology is kind of a no brainer. I would say to use your words, it makes perfect sense to me, why wouldn't you want to know when things are getting into your plant or when you need to stop the lines? It really makes sense. It's on the cutting edge of where plants are going. Plants are moving more toward automated systems and smart technology and smart mills and all these things. It really aligns with what's happening in plants today. Use technology to our advantage because it's here. Having this information in real time to protect other pieces of equipment is also very important.
Kilger: Definitely. Well, we mentioned that because intelligent magnet is what's happening now. Are you seeing other trends develop anything that's magnet technology for grain cleaning that could have an impact in the future?
Rhodes: Yeah, so Steven, there's a few big changes that I think we'll see unfold. One that is already taking place today is just the move to automated magnetic separators versus a manual or a quick-clean design.
As Kris mentioned, as they're building new plants with automation, you're going to want to automate your magnetic separator. That's going to put less stress on the plant maintenance teams that are already stressed out and having hard time having people on the staff to go and take care of the magnetic separator. So why not automate that when you can?
The biggest change that we're going to see is a continuation of that into adding intelligence to that through the patented and telematics platform that is going to continue to spread to different magnet designs in different applications. Based on our current experience, as our customer feedback has meant so far, they're finding that they're shutting down their equipment, way more necessary than they need to, to clean a magnet that has no metal on it. Adopting this technology is really going to enable them to increase the productivity and their profitability.
As they replace them with new magnetic separators and have this intelligence in this data, one thing I think that's going to result in, Steven, is that they're going to have less magnetic separators in the entire plant. As those get upgraded, they're going to be upgraded with better magnetic separators. They're going to be automated, and they're going to have real time monitoring. I think overall, the number of magnetic separators that are going to be used will be less into more efficient, more productive pieces of equipment, and getting a better ROI on their investment that they make.
Kilger: Automated clearing sounds amazing. There's less people than ever working in a plant. Something falls through the cracks, actually, so having all that automated already seems like it'd be great for everything right? Even your equipment and everything else because you can't the moment you have metal clunking through your conveying equipment, it can't be good for anything else on top of the grain quality. So yeah, that sounds really cool. Is there anything else that you guys want to mention that I might have forgotten with these questions, anything else you want to get out to our audience? Other than I'm sure you are willing to take their questions if they have any and they want to reach out. But other than that, anything you'd like to add?
Rhodes: Of course, Steven, so if anybody does want to reach out to us, they can reach out to us through our website at mpimagnet.com and much ways to contact us on there. Get the company's magnetic product safe and smart technology is the telematic.
Tennyson: Another thing I'll mention is we have direct employees of MPI all over the country, Steven, so if anyone has any questions or need some help locally, and you know we're here, we're based out of Michigan, but we also have we have people all over the country to help out. Just let us know. We're happy to help in any way we can.
Kilger: Excellent. Thank you so much for talking to me. Chris, it's been a pleasure and I hope we come back on and everyone should check these out because if you're not using intelligent magnets What are you doing thank you everyone for listening and we'll see you we'll see you next time.