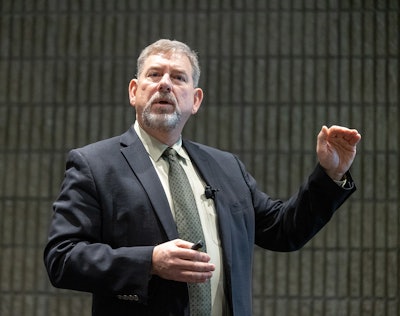
The American Feed Industry Association (AFIA) hosted its annual Feed Education Program January 25, covering what the animal food industry can expect from U.S. federal regulators in 2023 and findings from a recent African swine fever (ASF) feed mill decontamination study.
During the meeting, the AFIA also named Kent Nutrition Group’s Marshall, Missouri, plant as its 2022 Commercial Dry Feed Facility of the Year.
“Now, more than ever, we need to ensure we have access to all the tools in our toolbox, specifically formaldehyde, to continue providing safe animal food,” said Gary Huddleston, AFIA’s director of feed manufacturing and regulatory affairs.
“Feed Education Program attendees heard firsthand about the challenges we are facing and how formaldehyde shows promise as a potential way to decontaminate feed manufacturing equipment in the event of an ASF outbreak.”
Regulatory update
The program discussed upcoming priorities for the Environmental Protection Agency (EPA), Department of Labor (DOL) and Occupational Safety and Health Administration (OSHA); the Food and Drug Administration’s animal food manufacturing facility inspection plans for 2023; upcoming educational opportunities from the AFIA; and more.
One reminder Huddleston had for attendees involved the existing requirement in the current lockout/tagout (LOTO) regulation to conduct periodic inspections.
Employers need to conduct periodic inspections of the energy control procedure at least annually to ensure the procedure and the requirements of [1910.147] are being followed. Huddleston said this would include all feed mill equipment, impacting 20 to 30 pieces of machinery per mill on average.
Basic requirements for inspections are:
- It should be performed by an authorized employee (as defined in the standard) other than the one(s) using the energy control procedure being inspected
- It shall be conducted to correct any deviations or inadequacies identified
- It shall include a review, between the inspector and each authorized employee, of that employee's responsibilities under the energy control procedure being inspected
- Each set of machine-specific procedures must be inspected annually
ASF decontamination study
In regard to the recently completed ASF feed mill decontamination study, Chad Paulk, Ph.D., associate professor at Kansas State University and one of the lead researchers, said that the study showed using formaldehyde when flushing equipment demonstrated reduced detectable viral RNA of the ASF virus on feed equipment. Safety precautions for personnel, however, must be considered when using high concentrations of formaldehyde, Paulk noted.
Researchers at KSU recreated a feed mill environment within a biosecure laboratory to study how ASF spreads within the mill. They investigated possible strategies for feed mill decontamination in the case of pathogen contamination.
Using the model feed mill, researchers focused on two possible solutions. The first approach is a flushing technique like those used to prevent cross-contamination after production of medicated feeds.
Flushes, which are commonly a small batch of a single ingredient that is pushed through the mixer to collect any left-over product, create a “throw-away” batch of feed. They collect the remaining residue that may be present in a piece of equipment and pull it out into a batch that will be discarded at the completion of the batch.
Initial results from this solution show the virus, however, is still present in the model feed mill after flushing the equipment up to four times. Flushing with a dry, abrasive product may prove more effective, because it may better eliminate contaminated dust from mill equipment.
In case flushing does not work, researchers also plan to test strategies that would involve closing the mill for up to 48 hours and essentially fumigating the equipment, or even using portable heaters to try to kill the virus.
Flushing a feed mill with a mixture of corn and a high concentration of formaldehyde is one strategy KSU researchers intend to test as a possible means of whole-mill decontamination.
If effective, this kind of flushing strategy could be implemented at weekly or other intervals to serve as a sort of preventive maintenance or incorporated after the use of a potentially high-risk ingredient.
The 2024 AFIA Feed Education Program will take place Jan. 26 in Atlanta, Georgia, during the International Production & Processing Expo (IPPE). For more information, visit afia.org/events.