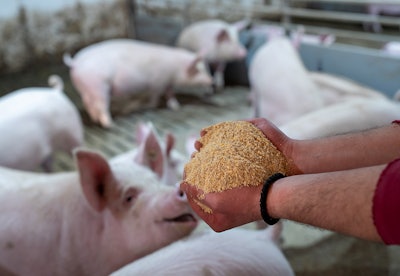
“While the African swine fever virus (ASFV) has not been detected within the U.S., if it were ever to be introduced, there would be severe economic consequences to the U.S. swine industry,” says Dr. Cassandra Jones, professor and ASI Teaching Coordinator, specializing in animal feed safety, livestock feed manufacturing and feed ingredient stability at Kansas State University (KSU).
As this time, the USDA classifies ASFV entry into the U.S. through feed and feed ingredients as low to negligible.
“Regardless of the specification, biosecurity within feed mills and throughout feed delivery is an important preventive step for any endemic or foreign animal disease,” says Jones.
The trouble with viruses, experts say, is that once they find their way into a feed mill, it is hard to get rid of them.
Based on previous research, once introduced through the feed, viruses like Porcine epidemic diarrhea virus (PEDV) or other endemic disease have been found through the entire feed manufacturing facility, especially on surfaces associated with employee movement.
Flush and decontaminate feed manufacturing equipment
The current available solution to “return to normal” if a feed mill has been contaminated includes power washing and disinfecting all interiors and exteriors of feed manufacturing equipment then heating up the facility to a high temperature – at least 140°F for 48 hours.
Researchers at KSU have recreated a feed mill environment within a biosecure laboratory to study how ASF spreads within the mill. They are investigating possible strategies for feed mill decontamination in the case of pathogen contamination, says Jones.
Using the model feed mill, researchers are focused on two possible solutions. The first approach is a flushing technique like those used to prevent cross-contamination after production of medicated feeds.
Flushes, which are commonly a small batch of a single ingredient that is pushed through the mixer to collect any left-over product, create a “throw-away” batch of feed. They collect the remaining residue that may be present in a piece of equipment and pull it out into a batch that will be discarded at the completion of the batch.
Initial results from this solution show the virus, however, is still present in the model feed mill after flushing the equipment up to four times. Flushing with a dry, abrasive product may prove more effective, because it may better eliminate contaminated dust from mill equipment.
In case flushing does not work, researchers also plan to test strategies that would involve closing the mill for up to 48 hours and essentially fumigating the equipment, or even using portable heaters to try to kill the virus.
Flushing a feed mill with a mixture of corn and a high concentration of formaldehyde is one strategy KSU researchers intend to test as a possible means of whole-mill decontamination.
If effective, this kind of flushing strategy could be implemented at weekly or other intervals to serve as a sort of preventive maintenance or incorporated after the use of a potentially high-risk ingredient.
Biosecurity and bioexclusion for feed manufacturing processes
“Given the challenge associated with stopping production and implementing these disinfection procedures, most feed mills choose to focus on bioexclusion and biosecurity,” says Jones.
Biosecurity practices and procedures reduce transmission of disease-causing organisms (pathogens) between agriculture facilities. A biosecurity plan can protect your feed mill from external pathogens and minimize the transmission of diseases within your system.
Bioexclusion of source ingredients may help mitigate the spread of contamination. Strategies may include quarantining imported feed ingredients at predetermined temperatures and length of time, thermal processing, or sequencing or flushing batches of feed.
Another option includes using a feed mitigant – additives such as organic acids, medium-chain fatty acids, essential oils and even formaldehyde which are effective at preventing viral contaminants in feed from infecting the animals that consume it.
Feed contamination with a disease-causing pathogen can be introduced at myriad points throughout the manufacturing process, including through using contaminated ingredients, during receiving at the feed manufacturing site, cross-contamination within the feed manufacturing facility, and by delivery vehicles and delivery personnel.
A biosecurity plan is essential to keep your feed mill secure.
How to develop a feed mill biosecurity plan
A well-designed and maintained animal food safety plan – when followed – will help mitigate disease risks and increase biosecurity.
In its “Developing Biosecurity Practices for Feed & Ingredient Manufacturing” guidance, the American Feed Industry Association (AFIA) says although a feed manufacturing facility may have systems in place to ensure that biosecurity risks from incoming ingredients are controlled, the facility should also implement processes and procedures.
- Ensure housekeeping practices maintain a clean and safe work environment
- Ensure the integrity of stored materials (i.e., ingredients, intermediate materials or finished products)
- Establish processes to review the facility’s compliance with its biosecurity plan and other procedures that act as barriers for animal diseases entering the property
- Ensure that all employees have adhered to the company personal hygiene policy prior to entering the manufacturing area
- Restrict access to key manufacturing areas to employees only
According to the AFIA, the first step when developing a biosecurity plan is to identify and prioritize the pathogenic agents of greatest concern to the facility. These might include infectious bacteria, viruses, fungi and others.
Once these agents are identified, appropriate personnel should become familiar with their pathogenesis, ecology and epidemiology, paying special attention to routes of transmission, susceptible species and age groups, and environmental factors favoring transmission.
Next, assess the facility to understand how the layout, traffic patterns, geography and staffing can increase the risk of disease transmission.
Also, consider consulting with a local veterinarian or a regional veterinary diagnostic laboratory that can identify potential feed-borne pathogens.
The most likely source of transmission: humans
Jones says through the research with the model feed mill at KSU, there was one place ASFV was always found every time they sampled: workers’ shoes.
The good news is that most feed mills have already made strides toward managing the flow of people in their facilities in order to prevent the spread of pathogens.
“When it comes to best biosecurity practices, focus should be on the biosecurity procedures involving people,” says Jones. “Research has shown that while, yes, feed could serve as a source of pathogen entry, people really do good job at moving it around and spreading it.”
How automation can help in a feed contamination event
Tracking an ingredient from receiving to loadout allows a feed mill to have concrete data on that product or ingredient and all the places it touched and was used while in the facility.
“Tracking provides the opportunity to go back into records and trace all batches and bins that a product or ingredient was used in,” says Brady Gaalswyk, co-president at Easy Automation.
For example, if a product is a part of a hand-add station at the facility, the product is assigned a lot number that is associated with the pallet it came on and that lot number is used and recorded for every batch that it is added into.
"This is important in the event of an audit, but also if there is a recall or an unexpected effect on the animals from the feed,” says Gaalswyk. “The feed mill can go back in their records and see everything added into that feed and where it originated from.”
Automation is also important on the receiving side of a mill to keep track of drivers, trucks and scale tickets in a digital format instead of a paper trail, which could save time in case contamination occurs.
Truck receiving automation allows mills to link the purchase order, record the truck and driver, make record of previous product hauled in the truck and FMCSA requirements, and verify signatures from the driver.
“Having this information in an automation technology system rather than in a stack of papers can help the response time in the event of contamination,” explains Gaalswyk.
If your feed mill ever does become contaminated, automation technology can help in two important ways.
- The ability to identify all batches that used the contaminated product quickly and efficiently to take actions in communicating the contamination to customers. This reduces the overall loss related to the potential recall because the mill can pinpoint exactly which batches were affected rather than just guessing around a potential contamination.
- The ability to program an automatic flush batch after a questionable or contaminated product. “There are settings we have used today for medications that prompt operators to utilize flush batches after medicated feeds and the same could be used in the event of a viral contamination at a mill,” says Gaalswyk.
“To date, we don’t foresee the automation technology we provide to ever test or identify contaminated products themselves, but we have the ability today to set parameters around an ingredient that require a higher degree of safeguarding like we have done with medication,” says Gaalswyk.