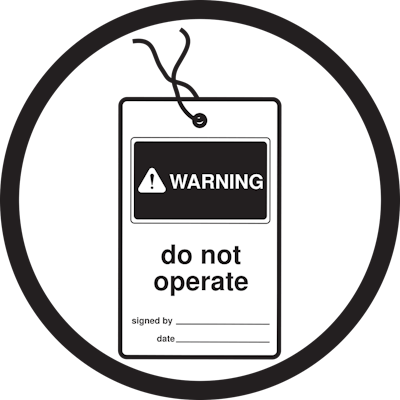
Hitting the “stop” button on potentially dangerous equipment is not enough. One of the leading causes of severe injuries and death in grain handling facilities involves the failure to de-energize equipment when performing maintenance or other servicing activities.
Properly controlling hazardous energy is achieved through effective Lockout/Tagout procedures – a crucial feature to any safety plan. Proper Lockout/Tagout procedures could potentially prevent almost all engulfments, electrocutions and entanglements that occur at grain, feed and processing facilities.
Locking out hazardous energy sources prevents loss of limbs and lives and it is one of the most frequently issued Occupational Safety and Health Administration (OSHA) citations.
Failure by employers to develop and use hazardous energy control procedures as required by OSHA’s Lockout/Tagout standard (29 CFR 1910.147) is one of the agency’s annual top 10 most frequently cited workplace safety violations. In the fiscal year 2019, Lockout/Tagout accounted for 2,606 violations, which ranked fifth out of the top ten OSHA citations. Lockout/Tagout was second only to the Grain Handling Standard (29 CFR 1910.272) among the top 10 citations at grain, feed and processing facilities.
OSHA’s standard for Lockout/Tagout, known as “The Control of Hazardous Energy,” establishes an employer’s responsibility to protect employees from hazardous energy sources on machines and equipment during service and maintenance. Many employers cited under this standard failed to establish an energy control procedure altogether. OSHA cited others for failing to provide adequate employee training, failing to conduct periodic evaluations of procedures and failing to use Lockout/Tagout devices or equipment.
Commercial grain, feed and processing facilities are required to follow OSHA standards, but the National Grain and Feed Association (NGFA) encourages the adoption of effective Lockout/Tagout procedures at all grain handling facilities. The standards set forth by OSHA and outlined below are directed toward employers, but they provide a guideline for any person working around grain handling equipment.
Establishing safety programs
OSHA’s Lockout/Tagout standard outlines controls to isolate machines or equipment from their energy source and affix appropriate locks or tags to prevent any unexpected energization, startup or release of stored energy that could injure employees. Some of the most critical provisions in the standard establish requirements for employers to develop a program to lock and tag energy-isolating devices that include:
- Implement written energy-control procedures that ensure machines and equipment are isolated and inoperative before any employee performs service or maintenance on such equipment
- Implement an employee training program
- Conduct periodic inspections to ensure the procedures are effective
Written energy control programs
Written procedures identify the information employees must know to control hazardous energy during equipment service or maintenance. If the information is the same for various machines or equipment, then a single energy-control procedure may be sufficient.
If there are other conditions, such as multiple energy sources, different connecting means, or a particular sequence that employees must follow to shut down the machine or equipment, the employer must develop and implement separate energy-control procedures.
Each written procedure for a machine or piece of equipment must include the following steps:
- Notify affected employees
- Shut down the machine or equipment
- Isolate machine/equipment from the energy source
- Apply a Lockout/Tagout device to machine or equipment
- Safely release stored or residual energy
- Verify the isolation of energy to the machine or equipment before work begins
Facilities should implement the following before removing Lockout/Tagout devices and restoring energy to equipment:
- Inspect the area to ensure the removal of non-essential items, and any machine components or guarding have been replaced
- Ensure all employees are positioned safely or removed from the area
- Verify that the controls are in neutral
- Lockout/Tagout devices are removed by the employee who placed them
- Notify affected employees of the removal of the Lockout/Tagout devices
Device checklist
Lockout/Tagout devices must be:
- Supplied by the employer
- Standardized by color, shape or size, tags standardized according to print and format
- Singularly identified
- Used only for this purpose
- Durable to the elements and not deteriorated
- Substantial enough to minimize early or accidental removal
- Identifiable to the employee(s) who apply them
Employee training
The employer is required to provide and certify that initial training and retraining, as necessary, have been conducted to ensure all employees understand the purpose, function and restrictions of the energy-control program.
- Facilities must provide employee retraining when:
- There is a change in job assignments, machines, equipment or processes that presents a new hazard
- When there is a change in the energy-control procedures
- If the required periodic inspection reveals there are deviations from or inadequacies in the energy-control procedures
Training for employees authorized to perform Lockout/Tagout procedures is to include the following topics:
- Recognition of applicable hazardous energy sources
- Details about the type and magnitude of the hazardous energy sources present
- The methods and means necessary to control those energy sources
- The means of verifying the effectiveness of energy control and the purpose of the procedures to be used
Employees who operate, use or work in an area where machines or equipment on which service or maintenance may be performed under Lockout or Tagout are to be instructed in the purpose and use of the energy control procedures. OSHA also requires that any employees who may be affected by the energy-control procedures be instructed about the procedures and importance of not attempting to start up or use the equipment, and they must not remove or tamper with Lockout/Tagout equipment.
Periodic inspection
The employer is required to evaluate the energy-control procedures at least annually to ensure that each procedure continues to be implemented properly and that employees are familiar with their responsibilities.
Periodic inspections are to be performed by an authorized employee other than the one(s) using the energy-control procedures. The employer is to certify that the periodic inspection has been performed, including the date of inspection, the identity of the machine or equipment on which the energy-control procedure was used, the employees included in the inspection and the person’s name conducting the inspection.
For Lockout procedures, the periodic inspection includes a review between the person conducting the periodic inspection and each authorized employee about the given employee’s responsibilities under the energy-control procedures being inspected.
For Tagout procedures, a review of the limitation of tags must be included between the person conducting the inspection and each authorized employee, operator or other employees working at the facility.
Safety resources
In February 2021, NGFA published a free, interactive training module covering Lockout/Tagout procedures on ngfa.org/safety. NGFA-produced training modules are issued periodically as part of the association’s continued commitment to enhance safety. These modules are funded by the National Grain and Feed Foundation and designed to provide information on certain hazards and best safety practices within the grain handling, feed and processing industry. ■