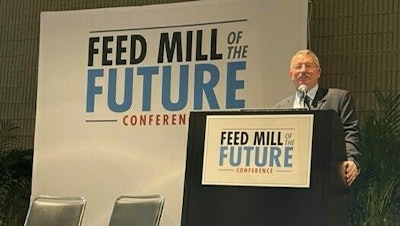
The biggest sustainability improvement you can make right now is to increase the efficiency of the equipment in your feed mill, said Wayne Cooper a feed industry consultant who spoke during the Feed Mill of the Future conference at the 2023 Production and Processing Expo (IPPE) in Atlanta.
Cooper said it’s best to focus on the largest energy users in your feed mill.
Equipment that uses the most energy
The equipment using the largest amount of electricity in a feed mill can be broken down as follows:
- 40% pelleting
- 26% milling
- 9% mixing
- 6% material handling
- 19% other
1. Pelleters
The pelleter is the biggest energy user in the feed mill, says Cooper. Not only does it use the most electricity but requires most of the gas as well.
Pelleters operating at less than 85% capacity is a red flag, says Cooper.
“The pellet mill is 40% of the energy cost in the feed mill — so it’s a major point to take care of and to control,” says Cooper. “The other thing that I continually see in the mills that I visit is that those pelleters aren’t being used at peak efficiency.”
Cooper says inadequate training contributes to inefficient pelleter operation.
“This might be an improper die selection or roller settings that are either too tight or too loose,” he says. “There’s a lot of variations in pellets, and it’s not extremely well understood.”
2. Conditioning
When conditioning is done right, pellet quality goes up and power usage goes down, says Cooper.
“You can save 20% of your power by getting conditioning right,” says Cooper.
Factors that contribute to inefficiencies in conditioning include old equipment designs, steam systems that don’t work, poor employee training and focusing on volume/tons.
“You need to look at your grinding systems, and whether your grinding system is the most efficient for the volume that you’re doing — and particularly micron size," says Cooper.
Hammermill versus roller mill
Hammermills are less efficient, says Cooper.
He also reminds if you have older equipment, check the motors to ensure they’re running at peak efficiency.
“I see ancient hammermills with worn motors and large-volume feed mills with no roller mills,” says Cooper. “And I ask, why?”
Cooper says he’d like to see more:
- Roller mills used alone for mash feeds
- Hammermills used when target is less than 500 microns
- Roller mills in front of hammermills (with larger volumes)
- Motors replaced when they fail efficiency tests
Evaluate and measure your decisions
Data helps make better decisions – measure everything you can, says Cooper. He suggests analyzing the following on a regular (monthly) basis at least:
- Kilowatts/ton for whole mill
- Kilowatts/ton at the pelleter
- Cubic feed of gas for the boiler
- Shrink
- Feed efficiency – talk to producers to see how the feed is doing
- PDI fines in the feed
- Die replacement
“There’s little points to consider all over in the feed mill, especially when you’re doing volume,” says Cooper.
Feed Mill of the Future Conference was presented by Feed Strategy and Feed & Grain magazines.
Related reading