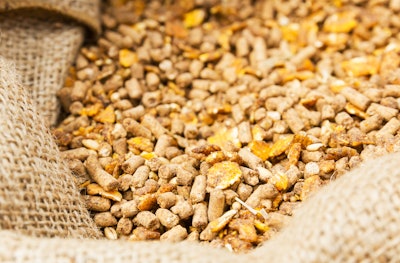
At the heart of the process for milling high-quality animal feed is the ability to efficiently crack or grind grain and reduce its particle size for more efficient and consistent nutrition intake. However, this process is energy intensive, making it crucial to explore ways to maximize efficiency while maintaining high product quality. By leveraging advancements in particle size reduction technology, such as roller mills, hammermills and integrated monitoring software, feed mills can reduce energy consumption and optimize operations.
The importance of particle size in animal feed
Animal feed quality is directly linked to the size of its particles.
"Particle size is vitally important to nutrient absorption, with each animal’s digestive system harnessing those nutrients to benefit their growth or productivity," said Darrell Malczewski, regional sales manager, Prater Industries.
Smaller particles allow younger animals, such as chicks, to ingest feed more easily, while more mature animals may benefit from larger particles. The ability to control particle size ensures optimal nutrient uptake, which is essential for the animals' health and productivity, whether in the form of milk, eggs or meat.
"Feed mills use two primary methods to break down particles: roller mills and hammermills. Each piece of equipment has its place depending on the application requirements, making it critical to work with a reputable OEM (original equipment manufacturer) that fully understands the facility constraints and future growth needs," said Blake Sandnes, general manager, RMS Roller-Grinder.
Sandnes said by selecting the right machine for their specific feed production needs, feed mills can maximize efficiency and reduce energy consumption.
Two major types of equipment dominate the particle size reduction process in feed mills: roller mills and hammermills. Each offers distinct advantages based on the type of material being processed.
Roller mills: These are widely regarded for their precision and energy efficiency. A typical roller mill is approximately 20-30% more energy efficient than a hammermill in most grinding applications. Roller mills crush grains between rotating rollers, allowing for controlled and consistent particle sizes. Newer designs include direct-drive systems, which eliminate belts and sheaves, resulting in an impressive 40-50% energy savings compared with traditional hammermills.
Hammermills: While hammermills are less energy efficient, they are versatile and widely used in feed mills. They pulverize grains by using rapidly rotating hammers, which can process a broad range of materials, from fibrous products to grains.
"Feed mills typically grind corn, oats, wheat, rye and even bakery ingredients," said Sandnes. "In rare occasions, feed mills grind alternative ingredients because that is what they have available. RMS has designed and manufactured solutions across multiple industries, offering assistance with unique applications."
Both systems have their place, and mills often select their equipment based on the specific ingredients being processed and their energy usage needs.
Energy efficiency and monitoring software
Energy consumption remains a significant concern for feed mills, as it directly impacts operating costs. In addition to energy, the performance of particle size reduction machinery can be affected by product attributes such as moisture content, particle size and abrasiveness, which can alter milling speeds.
"Energy input directly affects the feed mill’s cost per pound, so they will always look for ways to operate most efficiently and profitably," Malczewski said.
Implementing a robust maintenance plan and monitoring machine performance is essential for maintaining operational efficiency. One of the most promising innovations to monitor grinding in feed milling today is the integration of automation systems and grinder monitoring software.
"Software and automation allow business owners and operators to gain valuable insight into what is happening within their facility. Data is key, allowing for more informed decisions and helping to avoid costly mistakes," Malczewski said.
Monitoring systems enable operators to track particle size in real time and analyze historical data to maintain consistent quality. Traditional methods of sampling only at the beginning and end of shifts can leave gaps where product quality may fluctuate. With continuous monitoring, feed mills can ensure feed meets specifications at all times, preventing costly out-of-spec production.
"The control and automation system should include control and monitoring of the grinding function to ensure optimal loading and machine operation," said Joe Lewis, marketing manager, Sterling Systems & Controls.
Systems use programmable logic controllers (PLCs) for control and real-time feedback, which improves operating efficiency and reduces downtime by enabling proactive maintenance. This real-time feedback prevents overloading, minimizes wear on equipment and reduces the energy used per ton of material processed.
"Monitoring motor amps, mill classifier speed, and bearing conditions allows mills to fine-tune the grinding process, reduce energy costs and extend the lifespan of their machinery," Lewis said.
Trends and innovations in grinding technology
The particle size reduction industry continues to evolve with new technologies that enhance performance and reduce energy costs. Sandnes highlights RMS’s Endurance Roll Program as an innovation designed to prolong equipment life.
"Endurance Rolls have demonstrated to last 3-5 times longer than traditional cast iron rolls," Sandnes said, adding that the program also provides regular inspections and training for operators to maintain peak mill performance.
In terms of real-time monitoring, Sterling Systems & Controls is advancing with its enhanced predictability software.
"Predictability software can provide real-time data on a mill’s load, vibration signature and operating temperature, helping to highlight performance changes for more streamlined maintenance," Lewis said.
Tips for feed mill operators
Feed mill operators looking to improve their grinding processes can take several steps to maximize efficiency and reduce downtime. Malczewski advises operators to establish a specification for incoming grains, checking attributes such as particle size, moisture content and hull presence, which can increase wear on mills.
Having a robust control system is key to optimizing operations. Regular maintenance, proactive repairs and continuous monitoring prevent unplanned downtime and keep the feed mill running smoothly.
"Managing key mill parameters — such as motor amps, speed and pressures — and monitoring the machine's health through sensors at the bearing points ensures the grinding process operates efficiently," Lewis said.
Sandnes stresses the importance of partnering with equipment manufacturers to ensure operators receive the training and support they need.
"The roller mill is a critical part of your facility, so don’t let it go to chance. Become familiar with your machine and work with a manufacturer or service provider that can answer questions and help you address issues," Sandnes said.
In an industry where energy costs are rising and production demands are growing, feed mills must continuously seek ways to improve particle size reduction efficiency. Whether through advanced equipment or through integrating real-time monitoring systems, feed mills can achieve consistent, high-quality results while controlling costs.
By partnering with experienced OEMs and leveraging the latest in software and automation, feed mills can future-proof their operations, reduce energy consumption, and ensure that they remain competitive in an evolving marketplace. The key to success lies in understanding the nuances of the grinding process, investing in the right technology, and continuously optimizing operations for maximum efficiency and profitability.