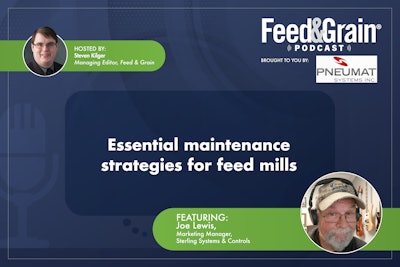
View on Zencastr
In this episode of the Feed & Grain Podcast, your host, Steven Kilger, is joined by Joe Lewis, Marketing Manager at Sterling Systems and Controls, to discuss critical maintenance strategies for feed mill operations. This episode dives deep into the importance of establishing a robust maintenance strategy to minimize downtime and extend equipment life. Tune in to learn about the technologies that drive maintenance strategies today and how to implement them without overwhelming your operations. Whether you're in the midst of upgrading your maintenance practices or just starting to consider your options, this episode provides the expertise and guidance needed to make informed decisions.
Steven Kilger - 00:00
Hello, my name is Steven Kilger and I'm the managing editor of Feed & Grain Magazine and the host of the Feed & Grain Podcast. Thank you so much for joining me today as we dive deep into the issues affecting feed manufacturing, grain handling and allied industries.
Today's episode is brought to you by the BinWhip from Pneumat Systems. The powerful Dual Impact BinWhip removes the toughest buildup and blockages in industrial storage silos without hazardous style entry.
Today I'm talking to Joe Lewis, marketing manager at Sterling Systems and Controls. We talk about the importance of having a maintenance strategy in feed mill operations, how to minimize downtime and extend equipment life with this strategy, and of course, what first steps feed mills should take when they're thinking of adopting one.
I hope you enjoy the interview. If you want to help out with a podcast or listen to this in a podcasting app, please rate us and subscribe. If you're listening online, sign up for the Feed & Grain newsletter Industry Watch to see when new podcasts drop and stay up to date with all the news from around the industry. Now onto the show.
Hi Joe, thank you so much for joining me today.
Joe Lewis - 01:01
Hey Steven, appreciate the opportunity very much.
Kilger - 01:07
Yeah, we're glad to have you on. Always a really important topic, but for anyone who doesn't know you, tell me a little bit about yourself and your time at Sterling Systems and Controls.
Lewis - 01:16
Yeah, I appreciate the opportunity. Boy, I tell you, you know, sit back and think about what I’ve done and where I’ve come from and whatnot, I’ve been around process measurement and control for over 45 years actually.
Started in the 1970s and was a systems engineer and did actually control system design using relay logic. It was before PLCs actually, just before. They have been involved with just about every facet of the business, from, you know, engineering, production, and sales and marketing, to general management. They did a couple of small business startups, which was absolutely enjoyable.
And the one thing throughout all of that, and I would say is a focal point for me, is very customer-centric and very much still around. To serve others and to do that by having conversations and if I can, depart a little bit of wisdom that I've gained over many years in business and a lot of different industries. Feed and grain for sure, food, baking, petrochemical, refining, plastic processing, all kinds of different industries.
Kilger - 02:57
Yeah, especially since you've been involved with automation and controls, like this big evolution that's happened over the last 40 years or so, where we went from basically nothing now to where we are, which we're here to talk about predictive maintenance and maintenance strategies feed mills, but I mean, wow, you've seen it all.
Lewis - 03:18
Well yeah, and one of the things I did mention is that when I first started actually I did some control systems work that were pneumatic, not just analog electronic with relay logic, but there were some pneumatic systems as well. And a lot of single-loop control and control panels that were the size of a small auditorium.
And yeah, so I mean, things have come around a little bit over, over the decades to the point where, you know, we can now talk about not just being reactive, In maintenance at a feed mill or rain processing facility, but actually preventing and, you know, hopefully in the not too distant future, if it's not here a little bit already, predictive. So I think there are some great things going on in that area.
Kilger - 04:07
Yeah. And it's something that I would argue that feed mills need, they can't do reactive maintenance anymore. It's too much downtime. You don't have the people to do it anymore. You need to really. Get this in line. Can you explain a little bit about the importance of having a maintenance strategy at a feed mill?
Lewis - 04:27
Yeah, I think when you talk about reactive, I think that there are still some that And I think that while maybe they do in some areas, I think that they're trying to think ahead and trying to understand and knowing their process and the equipment that they've got in place, trying to do things in advance of a failure, because just being reactive basically is going to shut down, not just the piece of equipment, but potentially it shut down your process that costs loads of money.
And something that if somebody's not dealing with that now, they really, really need to do it. So there really are three definite strategies and I'm going to put a question mark on a fourth that we can kind of answer when we get toward the end of our conversation.
The first you've already mentioned, and that is being completely reactive.
You don't do anything in regards to maintenance until something breaks and then at that point in time you scurry around. Hopefully, you've got some parts on hand to fix that item and you get it back up and running as quickly as possible.
But supply chain is what it is, often you don't have what you need to fix that equipment and it takes time, and that costs money. That's the first and generally, I think people have moved away from that, though some may still operate in that way, maybe smaller feed mills and Real strategy, and first of all what is a strategy?
A strategy can be defined as bold moves executed flawlessly and that's tough and that applies no matter whether you're looking at strategy from a military standpoint or you're looking at it from a business standpoint or anything else but when you look at that how do we come up with a good strategy for maintenance and as we evolved out of just being purely reactive The first thing that's obvious is how do we prevent these failures from happening to begin with?
And that is what I think, even today, is still one of the best, if not the best strategies available, and that is preventative maintenance. The reason I think that is still very high on the list in terms of a realistic strategy to employ at a feed mill is because you've got the tools that you need to absolutely put it in place today. You know your process, you know it better than anybody else, and in addition to that you know the equipment that you have.
And if whatever equipment you have, you've got support from manufacturers of that equipment that can help you identify what kind of preventative maintenance maybe should take place. And now all you really need is a tool that can help you do that in terms of, you know, maybe a simple software tool. I think preventative maintenance is first, the first step away from being just totally reactive. The other step that you could take is to be predictive. And what does that mean? Well, that means you're trying to foretell the future. And while that's still very difficult to do, there are advancements that have been made in that area to accomplish that.
And I’ll give you an example. And it's somewhat commonplace today. There are systems out there that are purchased and put in place at feed mills that monitor, for example, the temperature of bearings. And what is that doing? That's trying to predict when a failure is about to occur or has begun to occur so that you can take some appropriate action.
And most of those systems, and there's a handful of suppliers out there, have either analog outputs or relay outputs. And if you could have one that actually had an Ethernet IP port that a control system manufacturer could tie into, It would be amazing how much data could brought in and incorporated into the process control system to help you prevent if not predict when some of those failures might be getting ready to occur. So some of that does exist.
However, when you think about the way people define predictive maintenance or prediction today, They're really talking about the use of artificial intelligence and other types of algorithms to look at how various pieces of equipment are performing and predict that there's a pending failure in a couple of weeks and we ought to do XYZ to make sure that doesn't occur any, you know, no possibility of The reality of it is that gathering that data can be very expensive and the investment can be pretty significant in terms of what's called the IIOT or Industrial Internet of Things and various software systems that are out there that are promoting how they can basically help you in creating that IIOT. That can be very costly to do.
And I think what you've got to do in the long run is really look at what are the advantages and the return on that versus doing some type of preventative maintenance program today, which is doable and cost-effective. It doesn't require a tremendous amount of sensor data from various machines. It really is based on what you know about your process and what you know about the equipment that you have.
Kilger - 09:45
Yeah, definitely. I mean, all those sensors and things were getting there right in the industry. As you get new stuff, you see more that are connected to the Internet of things and all that. But if you're not quite there, there's this middle step, right? The industry itself might not be there.
Lewis - 10:27
That's a really good question, Steven.
And one of the other things would throw out there is when we talk about preventative maintenance, we're talking about being proactive. And that's important to understand.
When we talk about predictive, we're trying to foretell the future. With preventative maintenance, you can be very proactive in making sure that you do not have failures of equipment by just scheduling in advance certain maintenance requirements and parts replacements and so on and so forth.
Kilger - 10:47
If I'm thinking of it right, it's kind of like with your car, right? And your car, you get all this manufacturer thing, like change your brakes every 20,000 miles, oil change every 3000 miles, whatever it must be, where predictive maintenance would be monitoring your brake pads and then having a warning come up the moment that they were down to a certain point. Is that about, right?
Lewis - 11:10
That's a good analogy and I think that if we look at preventative maintenance programs there are some tools in place and some situations where you may not just want to be proactive in maintenance but there are certain situations that can occur that are safety related and catastrophic where you really need to monitor the equipment such as rotating equipment, particle size reduction equipment as an example.
You can get monitoring sensors and controls that will monitor not just the bearing temperature but acceleration and vibration and be able to set alarms that will begin to indicate that a problem, a catastrophic problem could be in the near future.
And allow the control system to start the shutdown process on the mill to allow you to perform whatever maintenance may be needed. So sometimes being able to see in advance what's coming, makes sense and it is doable today. And combining that with a preventative maintenance program overall, I think really is a good approach to take.
Kilger - 12:20
Yeah, especially if you have it on your more common points failure throughout your system, you monitor those a little closer. Especially that vibration monitoring technology, which I'm sure you've seen as well, but it notices things that the human eye would just never pick up. Little movements, micro-movements that you just could never see in real life. So that stuff's all very cool, but that's all probably a little in the future, especially for a lot of people.
So back to that question about like, how does this help, you know, minimize downtime, extend equipment life, all that kind of important stuff.
Lewis - 12:53
By anticipating and being proactive, the maintenance requirements of your equipment, which your equipment manufacturers can help you with, which your own experiential knowledge of your process can help you with. You can replace parts and schedule other maintenance activities before there is a failure and that's going to eliminate that failure in that downtime and that's the big plus a preventative program is not that difficult to put in place whereas the predictive programs require more investment and more complexity to actually put it in place.
Kilger - 13:28
Yeah, definitely. And I mean, it's a lot better to be able to schedule your downtown, right? You have to take a conveyor apart. A lot better to do it when it's not in the middle of the batching process.
Lewis - 13:38
Yeah, you can schedule it when it's the most convenient for you, so to speak.
Kilger - 13:42
For feed mills that are looking to kind of modernize their maintenance strategies, what are the first steps they should take? Should they reach out to someone like you and kind of walk them through the process? Should they have a list ready to bring to you to like, tell us this is my pain points, this is what I want to fix?
Lewis - 13:59
I think that the first thing is to assess their situation, to understand what they do today. If they're being very reactive, even in part, they need to understand that and then determine what their challenges and pain points really are. Are there parts of the process that are giving them problems more than others? And then I think probably the best thing to do from there is to begin to understand the technologies involved with the maintenance strategy options that exist out there, whether it's preventative or predictive or some combination of the two, and begin to determine what the cost of implementation is going to be.
And sometimes working with a Potential supply partner, whether it's Sterling Systems or someone else, can help them walk through that. I know one of the things that we do for our customers is to review their objectives, their requirements, and help them find custom solutions to whatever those objectives are.
Lewis - 14:59
And I think that once they do start to hone in on what type of strategy they want to put in place, I think that one of the things they might want to consider is a pilot program.
If they've got a couple of pieces of equipment or one particular area of their plant in particular that they would like to try out a particular maintenance strategy, they could put a pilot system or pilot program in place to do that.
The other thing I would tell people is not to forget the three T's and that is training, training, and training. Okay. Make sure that your people, your personnel understand our buying in there's change management in terms of changing from the way you used to do things to the way you're going to do things now And I think training is an essential piece of that.
Kilger - 15:45
Yeah, all that equipment in the world is helpful if people don't know how to use it and aren't actually doing it. For a feed mill who may be kind of interested in parts of it, but worried about the cost, is there a good way to balance that kind of cost of implementing the technology versus long-term benefits? It seems like maybe you could go and do a piecemeal, right? It seems like you need it, it could help to get just rid of the idea of like, oh, this is an all-or-nothing approach to doing stuff.
Lewis - 16:12
Well, I think that is one of the reasons why I believe that moving from the reactive to a preventative maintenance program may be the best choice for most people. Is because it does tend to be more cost effective.
You don't have to have all of the IIOT machine sensors connected, have any kind of special analytical algorithms running, and things like that, which can be also very expensive to put in place. And then the training on that could be a little bit more extensive than it would be on a preventative program. With preventative maintenance, there are software applications today available that would allow a feed mill to put the software application in place and set up various facilities and areas within the plants and facilities. The machines within those areas and schedule the maintenance and you have parts ordering involved with it, you know, they're pretty comprehensive and not overly expensive. We're not looking at tens of thousands of dollars.
Lewis - 17:10
We're looking at something a lot less than that and many may even be available without subscription costs. And can be also integrated into an overall feed mill automation and control system too. So that is a pretty good step for people to take and I think would be very cost-effective by comparison to trying to do something more predictive.
And I think that then it allows them to move away from being reactive and it will save them some money.
They'll be able to see the effects of having a better maintenance program in place. And then decide when the technology evolves more and the costs come down a little bit more whether or not going to a purely predictive system is a better way to go. And I would suggest that there's actually a fourth approach and that is going to be I think a combination of preventative and predictive and what I call a holistic approach.
And that's not there today, I don't think, though some people might suggest or promise it. I don't think it really is there today, but I think it's coming and it's coming in the not-too-distant future. But I think it's a holistic approach. It's not either preventative or predictive. I think there's going to be a combination of both of those.
When you bring in the sensor monitoring capability that you might have like a bearing temperature system, Or a mill monitoring system and you bring that into your preventative maintenance application that allows you to schedule things and interact with your vendors and your parts supply and so on and so forth.
I think you might have actually a better long-term solution.
Kilger - 18:45
Yeah, maybe next time you need to replace all your bearing monitors you talk to your provider about ones that connect to the Internet of Things you just slowly move there. Nothing has to be an all-and-out let's change everything at the feed mill one day.
Well, I know you're really well informed on this topic I know you're keeping an eye on it I have to ask you are there any new technologies or innovations and maintenance that you're like excited about you think are really going to game changers?
Lewis - 19:10
I think I'm more excited about seeing feed mill operations not get too enamored with the buzz and cautiously do what they do best and that is make feed, understand their process, investigate the technology that is out there or being promised, make sure that it's real, understand the cost of it and then come up with the best strategy for them and I think that one of the ways to do that actually is to stay involved with organizations such as Feed & Grain and Watt Global because you guys bring a lot of news to the table, a lot of technology information to the table and if I were to say one thing for the feed mill users out there, operators out there, stay in contact with what's going on in the industry and you'll probably be on the forefront of whatever new technology is going to evolve.
Kilger - 20:03
Yeah, I mean, it does get kind of annoying the term AI on everything to fix all their problems, right?
Lewis - 20:10
An AI is nothing but a series of very sophisticated and intelligent algorithms. We've been using algorithms and process control for decades. Yeah, it's different, but we've got to be careful not to get enamored too much with the buzz and look at the reality of it and proceed cautiously, but proceed nonetheless, make sure that you're evaluating everything before you jump in the whole body, so to speak.
Kilger - 20:35
Well, for anyone out there who likes what they hear and wants to learn more, how can they get in touch with you, experts at Sterling Systems, to answer more questions?
Lewis - 20:44
Well, I appreciate that question. Anybody that has any questions for me or wants to reach out just to have a conversation, that would be great.
My number is 815-863-8759 or they can email me at [email protected]. And you can also go to our website, www.sterlingcontrols.com. We did just launch a new website early in June and a lot of resources and information there, white papers, case studies, a bunch of testimonials, a lot from feed mill operators, and whatnot. And yeah, we just love to hear from people, even if it's just to have a quick conversation or ask some questions, that'd be great.
Kilger - 21:28
Yeah, of course. And that website will be linked in the description podcast and I can attest, it looks very good and has lots of information on there. So make sure you head on over and take a look. Joe, thank you so much for taking the time to talk to us today. I really appreciate it.
Lewis - 21:44
appreciate the opportunity as well, Steven. It's always a pleasure to be able to talk to the readership of Feed & Grain Magazine and try to help out a little bit.
Kilger - 21:52
Of course. We'll have to have you on again until then. Thank you everyone for listening. Stay safe out there.