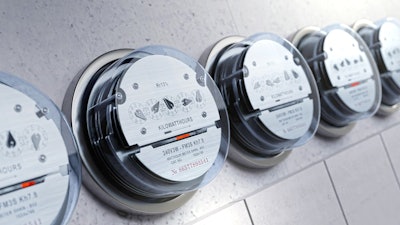
The production of animal feeds through pelleting is an energy-intensive process that can become prohibitive during times of high energy costs. As the demand for high-quality pelleted feeds for all species continues to rise, there is a growing need to optimize energy usage during pelleting. Implementing efficient strategies can not only benefit the environment, but also contribute to the overall profitability of feed mills. Here are various techniques to minimize energy consumption during the pelleting process of common animal feeds.
1. Equipment optimization
Regular Maintenance: Ensuring that pelleting equipment is well-maintained is essential for energy efficiency. Regular inspections and preventive maintenance can identify and rectify issues that may lead to energy wastage. This may appear as common logic, but there are many feed mills that skip maintenance calls to reduce operational expenses.
Upgrading Pelleting Machines: Investing in modern, energy-efficient pelleting machines with advanced technology can significantly reduce energy consumption. These machines often have improved heat distribution, reduced friction, and enhanced pellet quality. On the other hand, a new pelleting machine is a major expense that needs to be offset by sufficient volume of production during its expected lifetime or sooner.
2. Raw material preparation
Particle Size Reduction: Properly grinding raw materials to an optimal particle size before pelleting can reduce the energy required during the process. Smaller particles require less energy to be compressed into pellets.
Moisture Control: Maintaining the right moisture content in raw materials is crucial. Excessive moisture can increase the energy needed for pelleting, while insufficient moisture can lead to poor pellet quality. This is also related to particle size as smaller particles may absorb water faster. Implementing precise moisture control measures can optimize energy consumption.
3. Process control
Pellet Mill Conditioning: Efficient conditioning of raw materials before pelleting can enhance the gelatinization of starches and protein denaturation, reducing the energy required during pelleting. Proper steam conditioning ensures the formation of durable pellets.
Pellet Mill Parameters: Adjusting pellet mill parameters such as die thickness, compression ratio and roller speed according to specific feed formulations can optimize energy usage. Fine-tuning these parameters can enhance pellet quality while minimizing energy consumption. However, when it comes to pellet size (diameter) this is rather difficult to adjust as it is a factor dictated more by marketing rather than anything else.
4. Heat recovery systems
Implementing heat recovery systems in the pelleting process can capture and reuse thermal energy. Heat exchangers can recover heat from exhaust gases, preheating incoming air or water. This not only reduces energy consumption but also contributes to a more sustainable operation. Again, the installation of such equipment should not result in increased production cost, and thus they are only recommended in high-volume pellet production lines.
5. Batch size optimization
Adjusting batch sizes based on production demand can lead to energy savings. Smaller batches can reduce idle times and minimize the need for continuous operation, optimizing energy efficiency. On the other hand, one has to produce what is required. For that, it is best to schedule production in a manner that reduces downtime due to die changes etc.
6. Energy-efficient motors and controls
Motors are a forgotten part of pellet mills yet, they are the real energy consumers. Upgrading motors to high-efficiency models and implementing advanced control systems can significantly reduce energy consumption. Variable frequency drives (VFDs) allow for better control of motor speed, matching energy usage with production demands. This might be a more affordable solution compared to buying a new pellet mill.
7. Feed additives
Adding certain ingredients or additives can aid the pelleting process resulting in less energy consumption. This can be done through different approaches according to basic feed formulation. Raw materials such as oil and molasses, or additives such as kaolin can act as lubricants, reducing the friction inside the die — something that is a major energy sink, especially for hard-to-pellet feeds (those high in fibers).
8. Feed formula adjustments
Some raw materials can aid pelleting, as mentioned above, whilst others can make it more difficult, requiring more energy for processing. If possible, selecting raw materials during formulation that will not impair pelleting is something that a nutritionist can accept if this does not go against animal requirements. Discussing the issue with a nutritionist can bring about huge savings.
9. Employee training
This is presented last, but, in my opinion, needs to be done before even considering buying a pellet mill. Providing training to operators on best practices and efficient operation of pelleting equipment is absolutely crucial. Well-trained staff can identify and address issues promptly, ensuring that the equipment operates at its optimum efficiency.
In brief, reducing energy consumption during the pelleting of animal feeds is not only beneficial for the environment, but also for the economic sustainability of feed mills. By adopting a holistic approach that includes equipment optimization, raw material preparation, process control, heat recovery, batch size optimization, and employee training, feed producers can achieve significant energy savings. Implementing these strategies not only aligns with sustainable practices but also contributes to the overall efficiency and competitiveness of the animal feed industry.