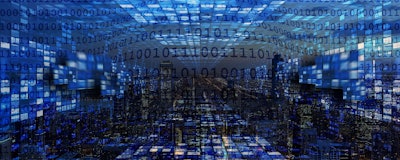
Let us set a scene. Gates open and close, allowing the perfect amount of ingredients to pass through them. Mills take those correctly measured components and start up, running with just the right speed and just long enough to mold them in to the perfect product. That product is conveyed, weighed, bagged and closed and palleted.
As the feed is made, data is gathered: how long was a machine on, how many times has it been used, where the ingredients came from (both what bin and what farm) and so much more.
All this happens without any human input. There is no chance for human error to be a factor. A person may watch it from acomputer screen while enjoying coffee in the control room or from phone screen while enjoying that coffee at the diner down the street.
Twenty years ago this would have felt implausible. Thirty years ago it would have felt like science fiction. But now it happens daily at facilities across the world. How did we get to this point? How far will we be in another 20 or 30 years?
Feed & Grain spoke with automation experts about their experience in the industry over the past 30 years and where they see automation going in the future.
A mechanical industry
The ever advancing flow of technology can make it hard to appreciate the progress the industry has made in a relatively short amount of time. When Mark Gaalswyk, owner and chief executive officer of Easy Automation Inc., Welcome, MN, started his family-owned company in 1986, processes were much more physical and mistakes more common.
“Back then employees pulled levers or pushed a button to open slide gates,” Gaalswyk says. “You would open the gate, then watch the scale, wait until the scale got up to a certain value, then close the gate. Often the ingredient would run up short or go over, and you probably never got around to writing the ingredient down, if you did it was on a notepad, marker boards or even the wall.”
Robert Kisner, owner of C.A. Technologies Inc., Greenville, MS, pivoted into agriculture from military contracts in 1989, after the end of the cold war, just as automation started to permeate the feed industry. Kisner has seen the industry go from not even wanting a computer on their desk to where we are today, and recalls the difficulty and limitations of selling back then.
“In the beginning, we tried to keep things as simple as possible,” Kisner explains. “That’s because it was up to local electricians and workers to support the facility once systems were installed and it needed to be relatively easy so they could work on it.”
Comco, Saskatoon, Canada, has designed and installed automation systems for various industries as well as provides machine and equipment automation systems across the world since 1986. Cheryl Lansink, their director of sales and located in their Ida Grove, IA, location, has seen those antiquated systems in action.
“I remember going to a facility where they stuck boards in gates to allow for blending,” Lansink recalls. “It worked, but it required more people to operate the plant. Then there was a time when I was a programmer and did a startup for a facility in Montana. I had the grandfather of the plant manager watch us load the first rail cars on the new system. He asked how long it took to load a car and told me ‘in his day’ it took a week for him to shovel enough to fill that car.”
WEM Automation LLC, New Berlin, WI, focuses solely on automation. Founded in 1916, WEM, the oldest company we talked with, can provide insight into control systems from before the late 80s, when what we consider “modern automation” started to appear in the industry.
Alan Berndtson, director of sales for WEM, was able to provide insight into those systems. “The control systems were electromechanical,” Berndtson explains. “Not necessarily a computer as we know a computer today. So using electromechanical devices, we could do some sequencing and the same task repetitively. However, over time, that evolved into what we know of as computers. In the early days of computer use, we used punch cards and paper tapes to load formulas. There was very little data storage. Paper connected everything.”
Connected by paper
For much of its time, in the feed and grain industries, automation systems were “connected by paper.” Unable to speak to one another, a system could do a single task, the onus of recording the data they provided or transferring it to another system was on the operator. Automation was limited to functions that computers could perform well.
“When automation started, it was really around the core process of mixing ingredients,” Gaalswyk says. “The systems could do things an operator could not, like figure out when to close a gate. With falling grain taken into account, mixing ratios were accurate, and the chance of a whole batch being ruined was reduced.”
These isolated systems were a boon for the industry, improving productivity and accuracy, but still left so much potential untapped. Don Goshert, vice president at Sterling Systems & Controls Inc., Sterling, IL, spoke about these isolated systems and what limited automation at the time.
“Things were very cumbersome around the turn of the century,” Goshert says. “Some facilities were manual, others had single controllers, but either way systems were independent and relying on a lot of operator interaction. There was no centralized data collection, so keeping records was very labor intensive and to research past batch information, ingredient usages, all those types of things, it took a lot of time and effort. It was this way because, in the early years, we were very limited in storage and memory.”
Processing speed and data storage have been driving forces in the computer market since its inception. It is easy to forget how far computing power has come in a relatively short amount of time. According to the article “A modern smartphone or a vintage supercomputer: which is more powerful?” on phonearena.com, Deep Blue a supercomputer made famous in 1997 for beating world chess champion Garry Kasparov, has less processing power than the Samsung Galaxy S5, a four-year-old smartphone.
“Modern PCs are so much more powerful and have pretty much-unlimited data,” Goshert explains. “We can use a SQL server and databases to give facilities flexibility for extended interfacing accessibility through systems and software.”
A web of data
A modern automation company’s ability to interface and connect the individual systems in a facility to one another allows for the collection of data on a level never before seen in the industry.
“We have evolved from a machine or process specific controls to a plant-wide or even a business ecosystem model,” says Jay Davis, director of business development for Repete Corp. “True full mill automation is an intelligent platform that is allocating work, schedules to process areas based on production priorities, equipment optimization, safety and tracking requirements and manufacturing dependencies. It supports broader business automation by executing production and reports the results through seamless integration with enterprise resource planning. Today’s automation will provide key data to support flexible, ad hoc reporting, business metrics and benchmarking between process areas and even plants.”
Lansink adds with the number of company mergers over the past number of years, companies are building largely centralized locations to replace the numerous smaller facilities that they may have had throughout a region.
“There is more equipment that needs to work better together and much more tracking, reporting and information are required out of the systems than ever before,” she says. “They also need to run longer with fewer people. We are no longer just making facilities ‘run’ – we are designing systems that also provide management teams the necessary information so that they can run better and now also smarter.”
Having more data not only helps a plant run and stay optimized, but will also help a company navigate the uncertain waters of regulation, or act as a life preserver during a catastrophe.
“What our customers used to do manually and with volumes of paper and file cabinets, we can do that electronically,” Berndtson says. “That becomes more and more important with the enactment of Food Safety Modernization Act. Having quick access to information is critical.”
However, automation companies do not see the adoption of facility-wide automation happening soon enough. Repete Corp., Sussex, WI, an independently owned automation company that serves both big and small companies across the world, has seen many companies who are being slow to adopt the new technology.
“Unfortunately, these systems are not common in the industry,” Davis says. “Many feed mills are not fully automated and certainly not optimized. Many plants lack the ‘connective tissue’ of routing between process areas that are required to support full traceability. ‘Islands of automation’ from different controllers in different process areas mean that work cannot be automatically scheduled, coordinated, optimized and reported. That reduces the efficiency of the mill and introduces risk.
“Improperly mixed feed, rework and even safety concerns can result when islands of automation exist, or a system is not properly designed, defined and tested,” he continues. “These risks are shared by large and small enterprises alike.”
Gaalswyk thinks that the lack of knowledge is the issue. “I don’t know whether people understand the level that automation can be tied together as one. They think that running four independent operations is normal — taking a call, writing it down, entering it into the accounting system, then entering it into the batching system — is normal versus having all systems working seamlessly together.”
The future of automation
More data collection: Thirty years ago, few would have guessed the sophistication of automation, nor its place in helping mills and elevators run at peak performance. Imagining the future of automation in the facility is like trying to guess the course of technology itself — nearly impossible. However, based on current trends, experts predict what could happen over the next few years.
“The network is going to provide connectivity to everything, everywhere, which makes more data available to everybody,” Kisner says. “We are going to be able to do greater performance measuring on equipment, people and the facility. It will be relied upon by the companies. It is going to become tied into the vernacular. You have real-world performance measuring at the plant level. Automation will help enhance employee productivity. Automation rarely replaces people. It changes their jobs, makes them more efficient and productive, but rarely does it displace anyone.”
Goshert agrees that more data collection is in the near future.
“I think our focus will be based on data collection,” Goshert says. “Information handling, process safety, equipment health and efficiency, predicting downtime, and minimizing production costs are possible now and will continue to improve with the more data we can collect.”
Artificial intelligence: There is an endgame for all the data collection that goes beyond optimization and employee efficiency.
“We already see more built-in intelligence into the system,” explains Berndtson. “It can react to situations in the plant without needing human interaction or intervention. We are going to continue to see more and more of that. Facilities will not require a human to continue to tweak the systems.
Soon, this may evolve past intelligence in individual systems to full facility intelligence.
“We often refer to intelligence and agility,” Davis explains. “Intelligence is the ability of a system to analyze the vast amount of production data and learn and adapt as it goes along. Intelligence allows systems to autonomously improve the performance of machines, processes and plants as part of smart manufacturing ecosystem. Agility refers to a system that can adapt to a changing environment, whether that means the easily changing the process by adding equipment and devices or by publishing data to support a produce a metric to solve a unique problem.”
How far we have come
In the beginning, Kisner admits that automation was a tough sell. However, as the old guard left, the newer generations began to see it as an increasingly useful tool.
“We really had to sell automation and technology in the beginning. Now, the new generation is running the place, and everybody is looking around and wondering why this is not on his or her phone yet,” Kisner explains. “Automation is a central tool in the industry, whereas before it got viewed as a necessary evil. Now, companies look at it like they are going to war — they need the best tools to fight the battle.”
Automation companies are there to help guide the industry and their customers into making the right decision in the present and prepare for the future.
“We want relationships with our customers for life, even into the next generations,” Gaalswyk says. “Customers are counting on us to research where technologies are going, where rules are going, and what we need to be doing. We need to be able to say we are ready for Veterinary Feed Directives or cell phone ordering.”
Lansink agrees. “Systems will continue getting leaner, faster and more reliable,” she says. “Lights out systems are becoming more important as facilities need to run longer with fewer people. Support services are more crucial to ensure downtime is minimal. We pride ourselves on being the best support resource our customers have.”
No matter what the future challenges the industry faces, technology, and creativity will provide the tools to overcome it — as soon as we are ready to embrace it.