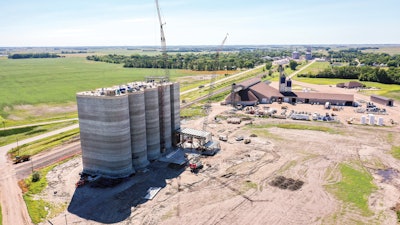
A labor shortage in rural America is one of the biggest challenges affecting grain handling and processing industries.
The traditional solution of enticing employees with better pay and benefits only works if there are actual employees available, and in many rural communities, the population just no longer exists.
For many companies recruiting employees has become a constant headache. That was the case for CHS in Herman, Minnesota, according to Jim Gales, PMP, who presented CHS' "Lights Out," Automation for After Hours Delivery, at the National Grain and Feed Association's 2022 Country Elevator Conference in St. Louis, Missouri.
Labor shortages impacting grain handling industry
Gales’ presentation focused on CHS’s new grain elevator and how it may be the closest grain facility in the U.S. to truly earn the label of “lights out."
When CHS started to think about building a new facility in Herman, the labor shortage became an issue for the company. Why spend millions on a new facility if there was no one to run it? To help negate the effects of a reduced workforce, Gales and others at CHS worked on automating one of the most labor-intensive processes at an elevator, grain receiving.
Grain sampling creates an obstacle
The biggest obstacle to automating grain receiving was automating the grain sampling process. Grain samples are how grain elevators direct truck traffic and determine a shipment’s value.
Every truck that goes through CHS’s grain receiving has a box that transmits data on the truck’s type, position, driver and who its hauling grain for back to the grain receiving system.
After the driver electronically confirms their information, the receiving system uses the data and probes the truck, tests the grain and directs the truck to the correct receiving bay.
Construction of the new elevator took place during the height of the Covid-19 pandemic, slowing construction. Even after the elevator was built, the system took almost a year of testing to perfect but now offers CHS customers greater flexibility, allows the elevator to operate with less staff, and provides employees’ work-life balance.
Now that it has been accomplished, Gales called on the rest of the industry to build similar systems. Not only does it create the best experience for customers, but it will also ensure the industry can meet its labor needs.