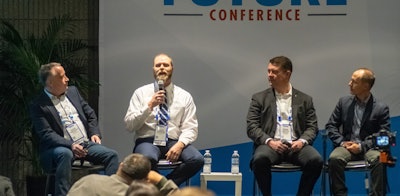
As sustainability drives initiatives across the food and ag value chain, a panel discussion during the Feed Mill of the Future Conference, held in conjunction with the 2023 International Production & Processing Expo (IPPE) in Atlanta, examined how feed manufacturing equipment, feed mill design and nutrition advancements can impact animal agriculture’s overall carbon footprint.
Moderated by Feed & Grain Editor Elise Schafer, the panel include Ryan Lane, president, North American animal nutrition business with ADM; Gero Zimmerman, head of technology – animal health with Bühler AG; Alex Kerrigan, vice president of project development with Todd & Sargent; and Marcelo Dalmagro, a broiler producer in Brazil and poultry strategic marketing & technology director with Cargill Animal Nutrition.
Here are a few highlights from the panel discussion of how animal ag can reach net zero by 2050.
Q: How can raw materials be used more effectively for feed production? What is the role of alternative ingredients, such as single-cell proteins or feed additives, for example?
A: Ryan Lane, ADM: Consumers both in the U.S. and globally are changing their behaviors to select products that are more sustainable, or what they perceive as sustainable. Our consumers are looking for nutritious, safe, sustainably raised and sourced animal proteins. When we look at as a supplier of ingredients, macro ingredients, micro ingredients, and those micro ingredients range from amino acids to feed enzymes, we need standardization. We need benchmarks and baselines to show the progress of what we're trying to achieve so everyone is on the same page. Do we have all the answers? The answer is no. We're on a journey together as we progressively look at sustainability.
Q: Can you share some examples of manufacturing process optimization or machines that can be adapted and reduce carbon emissions?
A: Zimmerman, Bühler AG: About five years back, we partnered with the biggest feed miller in Switzerland. We began by focusing on one pelleting line with a production capacity of 90,000 tonnes per year. The mill is running 40 to 50 different products on this line.
We installed some digital sensors in this line to gain insight into the state of the process and into the condition of the product. We could observe what was happening during the process at a given moment. We had to make sure the data was good quality. This is a very important step. It’s crucial to have good quality data.
We then integrated this data to a machine learning algorithm, an AI-based digital twin, and started to train this algorithm. In 2020, we switched over to a fully automatic operation based on this digital twin. Comparing this line to similar lines in the same plant, yield is better. The availability of this line is 20% higher over the years, so the mill is producing 20% more product on this line over one year.
Q: How does predictive maintenance dovetail into energy efficiency and optimization at the feed mill level?
A: Kerrigan, Todd & Sargent: You must take a holistic approach. Sensors can help bring insight and data on vibration analysis or when to check the filters or the baghouse filter, but you really need to focus on the entire operation, the entire feed mill.
What I’m saying is it's not just sensors. You should also get feedback from all sides – fresh eyes can make a big difference. That predictive side doesn't just need to be sensors. It needs to be the ease of checking equipment and how that will interface with your automation system as well.
Q: Marcelo, as a broiler producer, what kind of questions should be asked when conducting a supplier Sustainability Assessment of your feed suppliers?
A: Dalmagro: We trust our feed supplier to put together the best management practices, and the technology, behind nutrition to evolve. We have a very close connection to our supplier. We provide feedback and work to improve nutrition, especially with what we can touch at the farm level and on the physical quality of the feed.
We all play the same game, right? We are all working to convert feed into meat and to be more efficient and sustainable while doing it. We count a lot on the feed industry. As an integrator, we have been putting some technologies at the farm level to have more control of our operations, especially when measuring progress of the birds over time, feed consumption, and to make our buildings or equipment more efficient.
Feed Mill of the Future Conference was presented by Feed Strategy and Feed & Grain magazines.