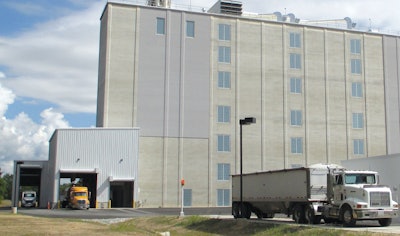
In a world where good customer service is hard to come by (ask any credit card holder or cable TV customer), it’s refreshing to hear about companies that succeed in making it a top priority. Star of the West Milling Co., based in Frankenmuth, MI, has become a leading example of what it means to put the customer first.
Johann Mathias and Johann Georg Hubinger, two brothers from Germany, came to the United States and founded their company in 1848 (with one wooden dam and a single flour mill), which then became Star of the West in 1870. From there, through continuous investment and expansion, Star of the West Milling Co. has become the 10th largest flour miller in the nation. Today it owns and operates five flour mills in four states (Michigan, Indiana, Ohio and New York) and 15 country elevators handling corn, soybeans, and edible bean processing, while providing local farmers with crop inputs.
Its reputation for quality products is overshadowed only by its record of excellent service. Upholding this value inspired Star of the West to form a supplier agreement that included building a new flour mill next door to one of its largest customers in order to better serve them.
The new seven-story 115-foot tall slip-formed concrete mill, located in Willard, OH, has a production capacity of 1 million pounds offlour/day, and uses soft red winter wheat exclusively which is sourced within a 50-mile radius of the mill. It also boasts a storage capacity of 1.2 million bushels, comprised of a 4-pack of concrete silos and three steel bins. Its most unique feature is the 8-inch-diameter pipeline that, once implemented this spring, will send 60,000 pounds of flour/hour directly to the commercial bakery next door.
In addition to meeting their customer’s needs, the decision to embark on a greenfield project and decommission its Kent, OH, flour mill (located 90 miles away from Willard) was influenced by gaining access to the CSX railroad and the area’s abundant wheat supply. But still, the decision wasn’t taken lightly or made hastily, according to Steven “Red” Michel, plant manager, Star of the West Milling Co.
“Sometime around 10 years ago we began trying to decide whether it was more worthwhile to invest in the Kent facility by doing a major upgrade or to build a new flour mill,” Michel said. “Between 2006 and 2014, there was a lot that went into the capital investment decision, the property negotiations and the long-term supplier agreement. There were also negotiations with the CSX on what we might be able to do with the railroad to serve other customers, as well.”
Relationships matter
By 2014, the planning and negotiating was complete and it was time to assemble a design and engineering team to determine the flow and layout of the mill and other buildings. Star of the West chose structural engineering firm Todd & Sargent, Inc. of Ames, IA, to provide the design work and Minneapolis-based Bühler Inc. as its main equipment supplier, explained Gary Pickelmann, corporate milling superintendent, Star of the West Milling Co.
“I’ve been with Star of the West for 43 years and we’ve always dealt very well with Bühler and done a number of projects with them,” Pickelmann said. “Obviously this is by far the largest project we’ve ever done, but that relationship has always been good and Bühler’s been a great partner over the years.”
Todd & Sargent and Bühler have built several mills together and had a good working relationship before beginning the Willard project together.
“I’d never worked with Todd & Sargent before, but I would recommend them highly anytime and look to them for help and assistance on future projects because our relationship with them is just fantastic,” Pickelmann said.
Star of the West also selected Janotta & Herner, Inc. of Monroeville, OH, to provide site engineering and preparation and on-site contractor services. Later on, for the steel bins they hired R.W. Mercer, of Jackson, MI, and Fredericks and Associates, of Toledo, OH, as the civil engineers.
Once the team was in place, construction crews broke ground on Sept. 29, 2014. The mill was completed in July 2016 and houses some of the most cutting-edge equipment and techniques known to the industry from grain receiving through finished flour load out.
Receiving and testing
The current receiving operation is all via truck until three rail spurs are completed — one each for receiving, load out and bypass. Trucks enter on the south side of the facility and pull up to a 20- by 44-feet truck receiving building for weighing and grading.
The receiving building houses a testing lab that rivals any in the industry with high-tech dockage testers, grain analyzers, mycotoxin testing equipment and falling number testing equipment. Usually one to two people staff this part of the operation, but during the busy harvest season, three employees are needed to keep it running smoothly.
“It’s like clockwork when these guys are busy,” Michel said. “In one nine- to 10-hour-day they did 60 trucks, and we were doing the weights and grades, Vomitoxin and falling number. We put water in here to give us the capability to run the same tests that they can do in the lab, but we didn’t want them running all the way up to the mill for every truck sample.”
Every single incoming load of wheat is tested, taking 12 to 13 minutes/truck, but Bobby Carrick, elevator operator, said the lab was designed to be able to test two trucks simultaneously.
“We try to do two tests at a time because that’s how the machines are set up,” Carrick said. “You’re running the dockage tester while another person’s probing the truck; then another guy is working on the centrifuges and then you are probing the next truck.”
Michel added, “It works like a Swiss watch in here with three people running two tests.”
After testing, trucks cross the scale to the 15,000 bushel/hour dump pit and exit on the south side of the facility.
Grain storage and processing
The total grain storage capacity at the facility is nearly 1.21 million bushels, including a four-pack of slip-form concrete silos (33 feet in diameter, 136 feet tall) each capable of holding more than 83,000 bushels. There is also an interstice with a storage capacity of 24,000 bushels.
Additional grain storage of 834,000 bushels is made up of three GSI corrugated steel tanks rated at 278,000 bushels each (60 feet in diameter, 117 feet tall).
Before the wheat goes into storage, it’s streamed through the Magnetic Products, Inc. in-line magnets before it hits the 250-ton/hour Bühler TAS 206A-6 LAAB universal pre-cleaner.
“We pre-clean before we go to the bins, and again when we come out of the storage bins before it goes into the cleaning house,” said Pickelmann. “There are a lot of magnets in the system to get outany tramp metal that could be in the grain. We also have optical color sorters from Bühler, which removes foreign material. Those features are really a workhorse in the new cleaning house nowadays. They do a great job of getting impurities out of the wheat.”
The automated tempering process utilizes a Bühler MOZL dampener turbolizer with a bi-rotor whirling system for consistency in moisture, allowing the product to mill properly through the rolls. Michel said they run the tempering equipment for about eight hours.
Next, the wheat streams to the second floor, where there are 19 Bühler MDDR single-high Antares and four MDDT double-high Antares roller mills, in addition to four Bühler MPAK Sirius 10-section plansifters, one six-section plansifter and two Bühler Polaris purifiers on various floors.
From there, the flour either goes through the pneumatic pipeline to one of their neighboring customer’s two bins, or to one of Star of the West’s 13 finished flour storage tanks, ranging in capacities from 55 to 150 tons.
The impressive finished product and bagging station is located on the first floor of the mill, in the warehouse. It incorporates a 30-ton-hour Bühler MPSH blowthrough air lock, a Bühler MSDL automatic hopper scale and a 10- to 12-bag/minute Bühler MWPG MAIA bagging station designed for filling 25- to 50-pound bags. The bags are then routed to the robotic Technipes palletizing line. Meanwhile, on the fifth floor, a 33-ton/hour Bühler MPAK foursection plansifter re-sifts the flour before it’s bagged or goes to bulk load-out.
Unique arrangement
Bühler and Todd & Sargent shared a role in engineering the pneumatic pipeline that will directly feed their customer with about 50% of the mill’s current production. Initial trials revealed a few areas that need tweaking before it can be put into use, but it’s anticipated to come onboard within the first quarter of 2017.
Until then, Star of the West Milling makes deliveries via truck, but the pipeline will add a whole new level of service and reliability to their arrangement.
“We’ve been talking about a better way to service them, and the ability to run a pipeline directly to it was one of the big advantages of our positioning the mill on the adjacent property,” Michel said. “You’re seeing a little bit more of that recently in the industry, but I wouldn’t call it ‘the norm.’”
Future projects
Because Star of the West is always looking to the future, there is already a strategy in place for growth at the Willard mill.
“We’re currently averaging five and a half days a week at 24 hours, but obviously we want to fill our running capacity,” Michel said. “We actually put plans in place that if we need to add a B-mill, we can do that.”
There is also room on-site to double the wheat storage capacity.
“In the next three to five years we plan to put more steel storage at the Willard facility,” said Pickelmann.