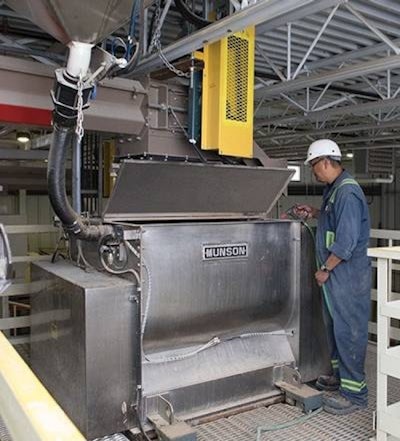
Country Junction Feeds has produced animal feed products in Alberta, Canada, for over 100 years. Today it offers a full line of organic wet and dry feeds for cattle, hogs, poultry, horses, bison, elk, goats and sheep.
To improve batch consistency and prevent damage when adding liquids to fragile ingredients, the company installed a fluidized-bed type mixer on its “wet feed" production line.
To blend dry ingredients with liquid additions in batches up to 660-pound, the company installed a Munson model MF-18-SS fluidized bed mixer.
"Fluidized bed mixing brought more batch-to-batch consistency than the previous auger mixer," explains Mark Shantz, Country Junction’s maintenance manager, adding that it imparts less shear than the auger mixer, reducing product degradation, particularly with fragile materials.
How liquid additions are mixed with dry blends
To initiate a mixing cycle, an operator enters a pre-programmed recipe at a plant workstation. Individual ingredients, stored in outdoor granaries, are transported by chain drag conveyors to the aforementioned dry mixer for pre-blending.
Blended batches discharged into bins are then conveyed by either of two drag chain conveyors to the fluidized bed mixer. Load cells supporting the mixer transmit weight gain information to a PLC, which stops the conveyor once the preset batch weight has been gained, with +/- 2.2 lb (+/- 1 kg) accuracy.
Once mixing begins, a fluid volume of oil or molasses equivalent to 3% to 10% of the dry premix weight is automatically metered from a 44-pound capacity vessel and gravity discharged into the top center intake of the fluidized bed mixer.
Fluidized mixing zone improves dispersion
The machine's fluidizing effect is achieved by twin paddle agitators rotating at 36 rpm within twin "U" shaped troughs at the bottom of the mixing vessel.
The counter-rotating agitators cause material from the troughs to become airborne along the centerline of the vessel where it intersperses rapidly with liquids sprayed into the "fluidized zone."
Mixing cycle times range from 10 seconds to 2 minutes depending on recipe.
Full-length drop-bottom gates open to discharge blended batches into a hopper, which feeds a filling line for 44-pound plastic fiber bags. Immediately after the bottom gates close, dry premix is loaded into the mixer, a pump refills the overhead liquid hopper, and a new cycle begins.
"We lift the lid and wash out the inside with water," Shantz says. "The interior is smooth and free of obstructions that trap material, which eliminates the need to manually scrape away residue. It’s easier to clean than the auger, and not as time consuming."
Country Junction Feeds is a division of Wetaskiwin Co-op, a cooperative whose local operations in the area include a home center, agro center, food store, bulk fuel and equipment sales, and related services. Country Junction’s feed is sold in Canada, but Shantz says the company is looking at international sales.