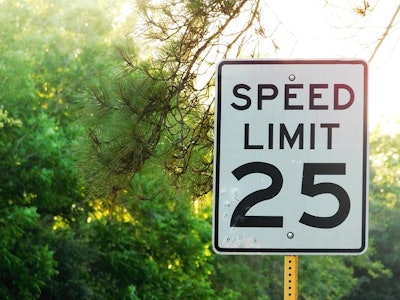
There have been several reports recently that the conveyor belt speed used by the belt scale system controller does not match the belt speed when checked by another method. The reported difference has been as much as 4-5%. I decided to investigate the cause(s) of the difference because any belt speed error in the controller is an equivalent accuracy error for the belt scale system unless a correction is made.
There can be several factors that contribute to belt speed errors including but not limited to:
- Incorrect scale factors used to convert the speed sensor signal to the belt speed
- Faulty speed sensors or speed sensor installation
- An error in the comparison method used to check the belt speed reported by the controller.
This article will focus on factor one: incorrect scale factors used to convert the speed sensor signal to belt speed.
First a little background information. Many belt scale systems include two sensors: the load sensor, or the weighbridge, and the speed sensor. The signal from each sensor sent is sampled multiple times per second by the controller, or the integrator. The integrator calculates the instantaneous rate output using this formula:
R = L x S, where
R = instantaneous rate
L = instantaneous belt load sampled from load sensor (weighbridge)
S = instantaneous belt speed sampled from the speed sensor.
The instantaneous rate output from the controller is one of the process variables of interest to the plant operator. The controller integrates the calculated instantaneous rate values over time to determine the total amount of product that has passed across the scale. Total production across the scale is another process variable that may be of interest to the plant operator. From the above formula, it is reasonable to conclude that any error in the conveyor belt speed compounds any error with the load signal. The first way to resolve your belt speed issue is to acquire the belt speed accurate prior to addressing any of your load sensor accuracy issue(s).
There are many types of speed sensors used on conveyor belt scales. The speed sensor is commonly coupled to the shaft of a non-drive pulley in contact with the conveyor belt at all times. The output signal is a square wave voltage pulse measured in hertz (Hz). The belt scale system controller reads the frequency signal and re-scales it to represent belt speed. The scale factor is called a “speed constant.” Instructions on how to program the “speed constant” is located in the manufacturer’s user manual. The pulley circumference and the pulses per revolution (PPR) are the two variables that influence the “speed constant.” The PPR is listed on the nameplate for the speed sensor. What should be used for the pulley circumference?
Belt scale manufacturers recommend using diameter of the coupled pulley to calculate the circumference. One may interpret this statement to mean the pulley diameter that is measured at one end of the pulley or whatever diameter is listed on the conveyor spec sheet/drawing. This may not always be accurate.
To ensure accuracy, consider these points:
- Some non-drive conveyor pulleys are crowned to help track the belt. The diameter of the pulley is larger in the center than compared to the ends (See Fig 1 and 2). The pulley circumference is based on using the largest pulley diameter.
- One manufacturers’ standard “hydro-crowned” pulley is tapered 1/8-inch per foot of width on the diameter or 1/4-inch maximum. The nominal pulley diameter is given at both ends and will have a larger diameter in the center.
- Machined-crown pulleys from another manufacturer use “1/8-inch x 8-inch that tapers off the radius each end on pulleys wider than 24-inches.” The nominal pulley diameter is given at the center and the pulley will be smaller at the ends.
- A belt manufacturer recommends using the “pitch line diameter” for calculating the pulley circumference. The pitch line diameter is further explained to be the measurement taken at the centroid of the belt when it is wrapped around a pulley.
- The belt manufacturer further explains that the centroid of the belt is where the belt is neither in compression or tension when it is wrapped around a pulley. Since the belt carcass cannot stretch or compress, consider using the centerline of the carcass as the centroid distance. Please reference figures 1, 2 and 3.
Let’s quantify the accuracy error by using the above points in an example. For example, if:
- Coupled pulley details: 16in dia x 38in wide, machined crown, 3/8in thk lagging
- Belt details: 36in wide, 2-ply, 220piw, 3/16x1/16in SBR covers, 11/32in overall thickness
- Speed sensor is a 256ppr encoder.
When the speed sensor is coupled to a pulley in contact with the belt bottom cover (Figure 1) belt centroid distance from the bottom cover (Figure 3) = ((S1-S2-S3)/2) + S2 (Formula 1)
= 0.109in
When the speed sensor is coupled to a pulley in contact with the top cover per Figure 2:
Belt centroid distance from top cover (Fig 3) = ((S1-S2-S3)/2) +S3 (Formula 2)
= 0.234in
If the belt scale commissioning agent uses the circumference at the end of the pulley, then the
circumference measurement may be based on as little as 15-3/4in diameter for the pulley details given above when the lagging thickness is also ignored.
“Speed Constant” = (256pulses/rev / (π x 15.75in/rev)) x 12in/ft. = 62.1pulses/ft.
When the installation is per Figure 1 and formula 1 applies:
- Pitch Line Diameter = 16 + (2 x (3/8 + 0.109)) = 16.97in
- “Speed Constant” = (256 / (π x 16.97)) x 12 = 57.6pulses/ft., which is a 7.8% difference
The difference can be even more for an installation where formula 2 applies:
- Pitch line diameter = 16 + (2 x (3/8 + 0.234)) = 17.22in
- “Speed Constant” = (256 / (π x 17.22)) x 12 = 56.8pulses/ft., which a 9.3% difference
The above analysis is one explanation for why the reported belt speed comparison to another
method can be different. It may not be practical to gather all the details needed to calculate the circumference based on using the “pitch line diameter.” Hence, for most belt scale installations, it is prudent to have another method of checking the belt speed to compare with the belt speed
per the controller.
Make adjustments to the “speed constant” in the controller as needed to get the belt speed right prior to working on load sensor signal accuracy differences.