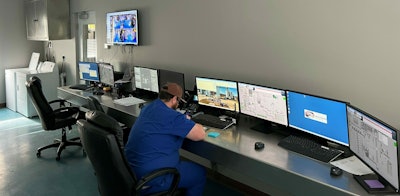
Nestled deep in the pine-tree covered hills of Tennessee lies one of the most biosecure feed processing plants in the world.
Protected by a tall chain link fence studded with security cameras around the building’s perimeter, no rail access, and nearly no visitors allowed inside, one might wonder what’s hiding inside the Pikeville, TN, feed mill.
But the answer’s no secret. Huntsville, AL-based Aviagen, one of the world’s leading poultry breeding stock companies, produces feed there for its own farms across three southeastern states.
While biosecurity is critical for all feed manufacturers, it’s paramount for Aviagen.
“As a global poultry breeder, we understand the downstream effects of our breeding program, and take seriously our responsibility to keep harmful pathogens out of the food chain,” said Richard Obermeyer, director of feed production, Aviagen. “Pathogen control begins with biosecurity, and our biosecurity, veterinary care, and health monitoring procedures are second to none.”
Eliminating biohazards from its newest feed mill was Aviagen’s guiding principle for everything from siting the mill and designing its layout to selecting the manufacturing equipment and cutting-edge automation, to developing its operating and pathogen detection procedures.
The 156,000-ton/year feed processing plant is ideally located to prevent contamination and allows the growing company to carry out its mission to supply the highest quality broiler breeding stock in the world.
Isolated setting offers perfect feed facility location
Global market growth over the last decade drove Aviagen’s need for additional feed production capacity. In 2020, the feed production team, along with engineer/contractor WL Port-Land Systems, Inc., began plans to build a greenfield feed manufacturing plant.
Reasons for siting the new facility in Pikeville include its proximity to local grain and Aviagen’s poultry production base — reducing hauling distance from mill to farm — while being far enough away from other potentially pathogen carrying poultry or livestock operations. The wooded terrain also offers a natural buffer from public crowds and residential traffic.
Groundbreaking on the site took place on July 20, 2020, and the construction of four specially designed steel structures, including 80,000 bushels of grain storage, went on for nearly two years. The Pikeville mill produced its first batch of feed in March 2022.
“WL Port-Land was amazing,” Obermeyer said. “They did a fantastic job keeping us on schedule throughout COVID despite supply chain delays by shifting delivery schedules and working with the product they had on hand whenever possible.”
Separating operations to reduce pathogenic spread
The plant’s biosecure design is modeled after Aviagen’s feed processing locations in Athens, AL, and Sallisaw, OK, with slight modifications and more distance between operations to further enhance biosecurity.
Operations are split into two distinct sections: the unobtained or “dirty side” and the obtained or “clean side.” The facility layout consists of four individual steel-walled structures with various functions:
- A corn, soy and ingredient receiving building with 80,000 bushels of grain storage. This includes a single dump pit receiving system rated at 100 tons/hour.
- The grinding, mixing and batching building, including an area for sealed ingredient storage bins.
- A mash heating, pelleting and cooling building.
- The finished feed loadout area.
The first two and part of the third buildings are considered unobtained. After feed is sanitized with a conditioning thermal treatment system, it reaches obtained status.
The obtained area and the finished feed loadout building can only be accessed by authorized employees after showering and donning company-issued clothes.
To reduce the risk of feed contamination from the outside, fencing serves as a barrier around the entire multi-structured feed mill.
“The idea of physically separating operations stems from controlling ‘people flow,’” Obermeyer said. “How we separate the movement of people on foot around the facility and how we handle truck traffic are practices we've learned from 23 years of producing biosecure feed in the United States.”
Aviagen separates not only processes and people at its feed production plants, but also closely controls the air movement.
The plant constantly filters the air with state-of-the-art equipment and each production stage has its own ventilation and HEPA filtration system. Meanwhile, spot filters are installed at each transition point along the conveying equipment and a vacuum system eliminates airborne dust.
Biosecure feed production and processing
To limit exposure to pathogens in transit, nearly all ingredients are locally sourced and are exclusively delivered by truck. Incoming traffic is monitored with closed circuit cameras while signage assists with traffic flow.
At receiving, the ingredients are unloaded from delivery trucks through an enclosed chute to prevent dust from spilling out. Then, moving along a 200-ton/hour GSI elevator leg, the ingredients are routed to storage.
A CPM hammermill grinds the corn, and it proceeds to the batching tower, featuring 21 bins and 48,000 cubic feet of ingredient storage. Ingredients are mixed with a Hayes & Stolz Ind. Mfg. Co. double ribbon mixer and liquid ingredients and microingredients are introduced directly to the mixer.
A CPM hot start conditioner uses boiler steam to hygeinise the feed and holds it for the prescribed time to eliminate pathogens. Post-sanitization, feed may be cooled as mash or conveyed to either a 30-ton/hour pellet line or a 10-ton/hour pellet line and is finally cooled to remove excess heat and moisture.
Pellets may be left as is or crumbled, depending on the age of the flock it will feed, and the pellets or crumble then go through an EBM Mfg. screener to sift out unwanted material.
Finished feed awaits shipment sealed inside 29 bins for a total of 1,000 tons of storage capacity. Once ready for delivery to a flock, the feed is weighed and loaded with a WL Port-Land Systems, Inc. lorry scale into Aviagen’s biosecure feed trucks, which are carefully maintained and washed regularly.
“The loadout building is a controlled area and the loading process is done with cameras and automation remotely,” Obermeyer said. “The operator controls it from the production office and the truck driver must stay inside the truck at all times when in the loading area.”
Automation aids with feed biosecurity
To simplify operations and improve efficiency, the processing facility is automated by CPM Automation.
All mixing, batching, pelleting and loadout operation automation is overseen from a centralized biosecure control room. Before entering, employees must shower and change into provided clothes. To reduce foot traffic to the obtained side, there are no pellet mill controls inside the pelleting building itself.
“The less traffic in those controlled areas, the less risk there is, so no one goes in or around the pellet mills for the entire shift,” Oberymeyer said. “If we operate literally with the lights out and no one present, it greatly reduces risk. This plant is as close to lights out feed manufacturing as you can get in present times.”
Pathogen monitoring and testing is key component
Once a week, Aviagen employees perform facility monitoring, which includes pathogenic testing on the buildings, equipment and finished feed.
“We’ve spent significant time advancing our testing techniques and procedures,” Obermeyer said. “How samples are collected and where they are taken from is paramount to the results, so our monitoring method is a critical component of biosecure feed production.”
Practices like segregating unobtained and obtained sides, restricting production area access and conducting weekly pathogen detection puts Aviagen at the forefront of biosecure feed production.
Adding cutting-edge automation and centralized process controls propels the Pikeville facility into the future with nearly lights out manufacturing capabilities. With room to expand production at the Pikeville feed plant, Aviagen is well-positioned to continue serving its growing breeder stock customers for decades to come.