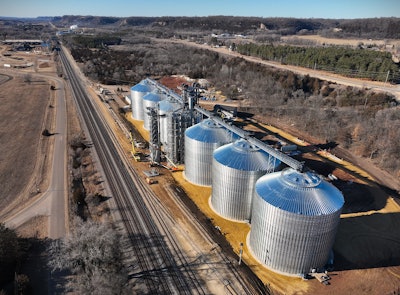
Jim Dell, CEO of ALCIVIA, recalled at the very first board meeting after Countryside Cooperative and Landmark Cooperative merged in 2021 and established ALCIVIA, one of the biggest member concerns was the grain markets in north-central Wisconsin.
“I was asked, ‘What are you going to do to improve the grain markets in north-central Wisconsin vs. what they are down in the southeast side of the state?’” Dell said. “At that time, there was probably a 40-cent basis spread between the two regions.”
Farmers in the northern region long faced logistical hurdles, including long hauls to distant grain terminals, extended wait times and unpredictable market access.
In March, ALCIVIA’s leadership answered the question directed at Dell by opening a state-of-the-art grain shuttle loading facility in Hager City, Wisconsin, located on the Upper Mississippi River just three miles north of Red Wing, Minnesota. Construction of the facility began in April 2024, and by January 2025, eight grain bins with a total storage capacity of 3.9 million bushels were completed.
The facility features three 1,500-bushel capacity dump pits for a combined handling speed of 60,000 bushels per hour and two 4,700-bushel-per-hour grain dryers. The terminal will dramatically reduce wait times for farmers during harvest periods and opens year-round market access for regional farmers with access to the BNSF main line.
“This should balance that (spread) out quite nicely,” Dell said. “Of course, there’s a cost to get it to the market, but this is our solution, and we’re very appreciative of the board and the membership standing behind us on this. As we live out our mission of advancing our customers through innovative and responsible solutions, giving them flexibility in their marketing that they’ll be able to count on more than four or five months out of the year is incredibly important.”
A perfect opportunity in Hager City
ALCIVIA’s commitment to providing reliable, year-round market access led to the planning of the shuttle loader in 2023. The discovery of a former frac sand facility in Hager City represented what Dell called the perfect alignment of infrastructure, location and opportunity.
“About a year ahead of construction, we began looking at the site from a perspective of if it could work,” said Dell. “It was a frac sand plant that stopped producing, and there was a lot of nice ladder track there.”
The existing rail infrastructure provided a significant head start for the project, allowing ALCIVIA to repurpose and expand upon the established foundation rather than starting from scratch. The 21,000 linear feet of trackage they acquired became the backbone of the 40-acre project.
The location’s value was also driven by its direct access to the broader rail network with the BNSF Railway.
BNSF, a leading transporter of agricultural products in the U.S., offers year-round market access across several U.S. domestic locations into Mexico and the Pacific Northwest (PNW). However, this region represented a gap in BNSF’s shuttle network with limited shuttle capacity, Dell said.
“This area is somewhat of a hole in their shuttle network, and so it brings a lot of potential incremental volume to them,” he said.
By identifying this gap, ALCIVIA leveraged a mutually beneficial partnership. The new facility meets the needs of ALCIVIA’s members and strengthens BNSF’s network, making it a win-win for both.
The Hager City location also complements ALCIVIA’s existing rail connections, enhancing the versatility of its transportation network.
With one shuttle loading facility on the Union Pacific (UP) rail line in Evansville, Wisconsin, and another on the Canadian Pacific Kansas City (CPKC) rail line in Fall River, Wisconsin, the addition of the BNSF-connected terminal provides ALCIVIA with strategic access to all three major Class I railroads serving the region.
Leading with speed
ALCIVIA invested in cutting-edge engineering and technological capabilities in its Hager City facility that set new benchmarks for operational efficiency in grain handling.
Designed with speed, precision and throughput in mind, the receiving system features three 15,000-bushel dump pits working in concert for a combined intake capacity of 60,000 bushels per hour. Dell said this transforms the unloading experience for farmers accustomed to long wait times at other facilities.
“The only limiting factor for a farmer coming in to dump grain is weighing and inspection as you come through, which doesn’t take very long, and then the gravity that it takes to open up the hoppers and dump the grain in.”
The emphasis on speed means farmers can spend more time hauling, potentially increasing their daily delivery capacity from “one or two loads to three or four loads a day,” Dell said.
The facility’s outbound loading capabilities are equally important. Dell said the terminal can load a 120-car shuttle in less than 10 hours, made possible by an 80,000-bushel-per-hour bulk weigher that can be fed simultaneously from four different directions within the facility.
This multi-directional feeding system provides flexibility and redundancy, ensuring the loading process continues smoothly even if issues arise in one part of the system.
To load in less than 10 hours, "everything has to go right, but we certainly aren’t going to be restricted by the capacity of the flow of grain," Dell said.
The advanced automation controls also enhance the facility’s speed and efficiency.
“All of our testing equipment, with the exception of damaged, is essentially automated into the computer system," Dell said.
While grain probing remains manual via hydraulic systems, the facility integrates Allen Bradley PLCs throughout its operations, with CMC hazard monitoring systems providing comprehensive safety measures.
These capabilities create a grain handling system that requires minimal staffing, as a single person can operate the entire elevator portion. The facility opened its doors with just six permanent employees — five to manage train loading operations and one handling inside sales and customer traffic.
The lean operational model allows ALCIVIA to maximize value for its members while maintaining competitive operating costs.
The facility’s two 4,700-bushel-per-hour grain dryers address another critical need locally.
“This site brings a very much-needed drying capacity in that area," Dell said. “Many existing facilities in the region are getting a little aged, so we put our investment dollars into this facility to move forward.”
The drying capacity ensures farmers can deliver grain at higher moisture levels, allowing them to begin harvest earlier or continue through challenging weather conditions without sacrificing grain quality or marketability.
For farmers accustomed to older, slower facilities with extended wait times and limited handling capabilities, the Hager City terminal represents a leap forward in grain handling technology and efficiency.
Breaking the seasonal barrier
For generations, farmers in western Wisconsin and southeastern Minnesota have faced the seasonal nature of river transportation — a significant constraint on their marketing options and profitability.
The upper Mississippi River system has traditionally served as the primary transportation artery for grain from the region to distant markets. While effective during the warmer months, it essentially shuts down during winter freeze periods, creating a gap in market access, forcing farmers to sell during compressed timeframes or bear the cost of extended storage.
“The ability to have 12-month bids for our customers is game-changing,” Dell said. “It allows them to move their grain when it’s right for them and matches their cash flows, vs. waiting on the river like they’ve had to do for several years.”
Another limitation of river transportation is the growing disconnect between existing river infrastructure and evolving transportation requirements. While the Mississippi River system has served the region well, its limited draft depth increasingly restricts the size and capacity of vessels that can navigate the waters. Modern shipping continues to trend toward larger vessels with deeper drafts, which can operate more efficiently and economically — but only in waterways with sufficient depth.
“The river terminals as we know them today are built for nine-foot drafts on barge equipment and, moving forward, it’s all being built for 13-foot drafts,” Dell said. “This facility provides an opportunity for our producers to market 12 months out of the year with both solid export capabilities and domestic capabilities fitting in with the rest of our shell network.”
Rail shipping circumvents the limitations of river infrastructure and the annual freeze that has largely defined logistics in the region, making the Hager City rail facility future- and weather-proofed for ALCIVIA’s transportation operations.
Vision for growth and local impact
ALCIVIA’s Hager City facility was designed with potential future expansions in mind to streamline market access and reduce transportation burdens for local farmers.
“There’s room to increase grain capacity over time, if needed,” Dell said. “Beyond grain storage, the facility could evolve into a more comprehensive agricultural hub, offering inbound feed ingredients and, if demand dictates, even fertilizers — both liquid and dry.”
Another possibility on the horizon is the addition of liquid propane infrastructure.
“This part of the country is not getting more pipeline to draw from, and so we may be looking to bring some rail liquid propane in there to offload sometime down the road, but nothing in the near future,” Dell said.
While these expansions remain future visions, the foundation for growth is in place, ensuring the cooperative continues to meet the evolving needs of local producers.
Dell highlighted how the facility will also improve quality of life for farmers. He revealed one producer was traveling up to an hour and a half each way to deliver grain elsewhere, spending nearly three hours a day in his truck between the drive and wait times. ALCIVIA’s investment in its Hager City facility changes this equation entirely, affording farmers the ability to get home in time for dinner.
“It’s great for our local producers and their families, it’s good for the state and we’re really excited to play a part in that,” Dell said.