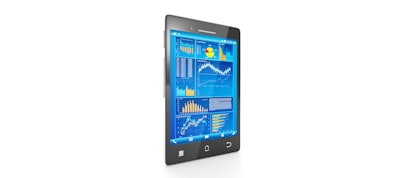
What do you need to run your facility?
It’s a complex question that is becoming simpler to answer, and part of the solution might already be in your pocket. Over the past 20 years, both the feed manufacturing and grain handling industries have been going through a process of computerization and automation that has changed almost every facet of day-to-day operations. Computers can now monitor any process performed in a facility, changing input levels, turning on and off aeration systems and shutting off components before they have a chance to fail. But until recently, this ability has been reserved for a desktop in the control room and the person watching the monitor. Now, with the smartphone many already own, that is no longer a limiting factor.
According to the Pew Research Center, as of January 2014, 58% of adults have a smartphone of some kind, a percentage that has been rising year after year. The smartphone, and other mobile technologies such as tablets or laptops, have become a part of daily life for a majority of Americans. It is making itself a part of the daily lives of those in both the grain handling and feed manufacturing industries. The list of problems that can be solved with the device in your pocket or bag grows every year.
Expanding automation
The introduction and widespread use of the smartphone is just another step in the ongoing process of automation for both feed and grain businesses, a process that has come a long way in a relatively short amount of time.
“When Bill Clinton became president in 1993, he convened an economic summit of top business leaders, labor leaders and scholars to discuss ways to grow the economy,” reflected Mike McGeever, vice president of Grossman & Associates. “Their report generated reams of paper but the word ‘Internet’ was never used. Software is becoming smarter, and it’s now possible to warehouse and analyze big data in ways people never thought possible.”
Cheryl Lansink, sales and marketing at Comco, added,“In the past 15 years it has gone from, ‘I can start that conveyor or I can stop that conveyor,’ to advanced facility control.”
Having automated technology running operations in facilities has been an industry standard in the feed industry for years, and the grain industry is rapidly catching up. The advantages of the technology are numerous and evolving. Automation improves equipment life expectancy, employee safety and productivity, facility efficiency and ultimately profitability.
Mobilizing automation
The advancements to automation over the past few years have been spurred by improvements on technology outside of the industry, including wireless networks and mobile devices, giving the access to new levels of flexibility.
“The internet has become so stable and fast, it allows us to use remote access to provide real-time troubleshooting and remote support to assist our customers, but we also allow our customers to use this technology,” Lansink explained. “If a manager is in charge of multiple facilities, we can give him a login, and he can check on, or pull numbers from, any facility no matter where he is. This is a real time saver. ”
Wirelessly accessing a facility that is running through automation software allows companies to run a facility with little to no staff.
“Repete continues to drive toward supporting true ‘lights out’ automation,” said Jay Davis, director – business development at Repete Corporation. “Meaning facilities will have the capability of operating with almost no direct labor, aside from maintaining equipment and managing exceptions.”
Running a facility with no staff can be key in areas with limited workforce, or at smaller operations that can’t afford to employ someone continuously on-site.
“This remote access technology doesn’t just help big companies; it allows small guys, who don’t have long hours, run operations after they close,” Lansink said. “We have a customer who runs his dryers 24/7 and at night just monitors it on his phone.”
Having the ability to access information on a facility remotely and instantly can connect operations that are spread out across several buildings or even several miles.
“If a co-op has a serious agronomy department, they have a fertilizer building somewhere, and a blending unit somewhere else, but probably not in the same building as the main office,” explains Chuck Jenkins, director of marketing and sales for AgTrax. “Cloud-based software can reach out to those other locations so that their day-to-day operations can be seamless, and in real time, be included in the financials that are being managed in the main office.”
Mobilizing operations management
Automation companies aren’t the only ones taking advantage of remote technology; the programs that are used to run the day-to-day operations like accounting and contract organization also benefit.
“All our customers manage their software through some sort of remote access or cloud solution,” explained McGeever. “This year we completed an extremely large national rollout involving hundreds of users, switching from numerous remote systems to a single cloud-based solution sharing a common database.”
These programs can be seamlessly integrated with other automation software already running in a facility.
“Three years ago, we decided to stop trying to be everything to everybody,” Jenkins explained. “So if a feed mill has already spent $10,000-plus on a management program, we’re not going to ask you to throw that out because you want new accounting software.”
Even cloud based programs can be set up without the need to invest in servers or technology staff.
“We host systems here in our office so companies who don’t want to take on the cost or carry the IT needs on the staff can use our software via the ‘cloud’,” Michelle Blomberg, president/CEO of AgVantage Software.
The use of remote technology is becoming increasingly accepted for both private and commercial use. As an industry where every second counts, the time-saving benefits are becoming clear to the industry’s customers.
“As farmers get used to making purchases and conducting their banking online, they similarly expect to be able to settle grain and make contracts at their convenience,” McGeever said.
Automation partnership
With the speed that technology moves, it can be hard to keep up, for both consumers and automation software providers. New innovations can become out of date within a few years, and in an increasingly competitive business world, being out of date can put a company out of business. Luckily, automation providers form a partnership with their customers in order to make sure they’re getting what they need. Sitting down with an automation software provider will allow customers to see what is available.
“Technology is moving so rapidly,” Jenkins explained. “We don’t have feed experts, agronomists or document imaging specialists on staff, but we can bring the tools of other companies who do to our users and make it like they’re only running one program.”
“We’ve gotten great feedback on availability, which refers to our ability to keep the plant producing a product at the highest level of output, quality and consistency,” Davis said. “Our customers also told us that they need seamless integration with business and nutrition software, and we responded with solutions to meet these demands.”
The partnership goes both ways, as companies are constantly on the lookout for what the grain and feed industries need.
“We have a customer in Ohio who consulted with us to develop a system to tackle a long-standing issue in the grain handling industry,” explained Blomberg. “We developed a system that allows an electronic signature to be attached to a grain contract, including the approval process from the farmer. This allows the contract process to be expedited at warp speeds, compared to the paper signature process. Using Web tools to speed up the process of contracts has been a game changer.”
Mobile technology allows providers to offer new levels of customer service, with the ability to access your system from a remote location and walk a facility through a problem. Service like this reduces downtime to a minimum and keeps the cost down.
“It’s like a team member is ‘virtually’ sitting next to them and resolving issues in real time,” Davis explained. “Our team can diagnose, resolve and coach our customers in several different languages. We can also support monitoring of multiple plant performance metrics, allow benchmarking to lower cost and increase production.”
How far we’ve come
In just over 20 years, the Internet has changed the way we do business, and in the past 10 years mobile phones have changed it even more. If it seems like technology is changing faster than it’s possible to keep up with, you’re not alone. But in an industry where winning a customer often relies on what services you provide and how fast you can provide them, no one can sit idly and watch technology pass by. It pays to keep in touch with those who provide your automation and operations management technology, and form a partnership to help keep you at the front of the technology pack.
Subscribe to Magazine