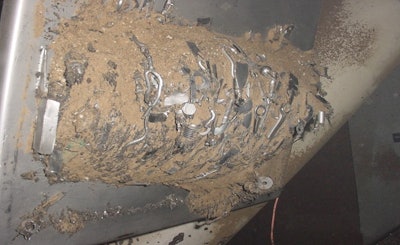
Metal contamination to products at your grain or feed facility can be dangerous and costly.
It can cause severe damage to expensive processing equipment, result in product recalls or create unwanted downtime to repair broken machinery.
Metal contamination in processed grain or feed can cause severe damage to expensive processing equipment, result in product recalls or create unwanted downtime to repair broken machinery.
“Grain processing or milling facilities that have proper magnetic separation equipment will reduce the risk of a product recall due to ferrous metal and work hardened stainless steel,” says Kyle Rhodes, vice president – Business Development with MPI.
Magnets will reduce the amount of equipment damage, maintenance and downtime from tramp metal, notes Rhodes.
High cost of metal contamination in grains
Metal contamination does not always come from the upstream supply chain, says Dennis O’Leary, chief business development officer with Industrial Magnetics, Inc.
“Capex and processing equipment itself is often the culprit,” says O’Leary. “This necessitates the use of magnets to capture metal fragments from screen material, fasteners, abrading and contact-friction surfaces, which create metal fines, among other offenders.”
Magnets, however, are commonly categorized as “auxiliary equipment.”
“The purpose of this equipment is to help, protect and support other equipment,” he says. “What makes magnets attractive is that they have a low cost to operate versus a significant cost of failure.”
O’Leary says if a plant should choose to bypass the selection and installation of magnetic separation equipment and subsequently experience a metal contamination incident, it can be financially crippling.
“Generally, a single magnetic separator may contribute 1% to 2% of a manufacturing line’s equipment cost, and even less as a percentage to clean and operate.”
What type of magnet is best for grain?
Separation magnets for grain products spans a broad range of options.
According to Al Crawshaw, president with Puritan Magnetics, Inc., the most common magnets used in the feed and grain industry are plate magnets and grate or drawer magnets.
- Plate magnets are a low-cost, easy-to-install option that can have a large reach out. They are highly effective right before the infeed conveyors or hammermills and can be installed hanging above belts or installed on the sides of chutes or other processing equipment.
- Grate or drawer magnets are designed for dry, free-flowing gravity fed products that can easily cascade through the 1-inch-diameter bars mounted on 2-inch centers.
These magnets are the most effective in gravity applications under silos or downspout areas. They provide a strong direct surface contact to capture and hold smaller metal pieces.
Because product goes around the cartridge or tube magnets in a waterfall fashion, all material comes into direct contact with a magnet.
“The magnetic tubes have the strongest magnetic circuit and provide the best separation results,” says Crawshaw.
If a customer has an angled chute, installing a plate magnet on the underside of the chute allows the product to run over the face of the plate, he says.
Marc Suderman, product manager with Bunting Magnetics, says inline magnets are also commonly used in pneumatic conveying situations.
- Inline magnets are used in pneumatic conveying and are highly effective at removing any metal being conveyed in the line that should be removed.
Ceramic magnets are commonly used in flour milling to prevent iron enrichment from being removed and collected by the magnet.
Proper magnet placement
Sources agreed there are three important areas to install magnets throughout your facility: primary, secondary and receiving areas.
“The best way to keep metal from wreaking havoc on your plant’s equipment and ending up in your final product, is to keep metal from coming into the plant in the first place,” says Rhodes.
- Primary magnets should be installed at plant receiving areas.
Suderman agrees, noting this is particularly important for milling operations.
“You want to always have a magnet on your infeed lines,” he says. “You never know what is going to come in from unloading truck or rail cars.”
Plate magnets placed before or on the hammermills and on down spout lines can capture the invading metal before it gets too far.
“Once the grain becomes broken and is starting to be turned into flour, an inline magnet would prevent any fine metal from continuing down the processing line,” says Suderman.
“You never want to have a trailer hitch pin or another large metal piece go into the processing plant.”
- Secondary magnets are used throughout the facility to protect equipment and detect equipment failures.
“Magnets installed mid-stream are ideal to ensure operational efficiency and protect capital equipment by virtue of keeping the process flow clean and humming along,” says O’Leary.
“Minimizing downtime to repair or replace capex investments, filter bags, screens and sifters due to metal damage equates to higher throughput and profitability.”
- Finishing magnets are usually the critical control point.
“The expectation of the finishing magnet is it’s working the least due to magnets upstream doing their part to remove tramp metal, and therefore, always working at peak performance to remove any metal as close to packaging or load out as possible,” says Rhodes.
As a final check, install a grate or drawer magnet right before the final inspection or bagging area. The magnet can remove all the ferrous contamination, so the metal detector or X-ray does not reject any bags due to ferrous contamination.
Magnets placed at end-of-line packaging/bulk load-out locations provide a final inspection to ensure that no contaminants – be it fines or large tramp iron like a nut or bolt – leave the processing plant where their discovery in a finished, consumable product could and has been known to have catastrophic results.
“Having all three of these locations covered by magnetic separators offers you control points – places where the entry point of metal contamination can clearly be narrowed down and pinpointed since there are multiple magnets in use,” says O’Leary.
“This makes discovery faster and return-to-production time quicker and more efficient.”
Select the right magnet features
In many grain and milling applications, the product being handled is abrasive. For that reason, when selecting a magnet, consider features that can prolong its life or are replaceable.
Magnets should be properly sized for the application, so they’re not too weak or too strong.
“A stronger magnet is not always the answer, but the magnet should always provide full coverage of your product flow,” says Suderman.
Also, any magnet should be easy to access. The easier it is to clean, the better.
“If the magnet is in an access point that is difficult to reach, or if it requires a lot of work to clean, facility personnel will struggle to regularly clean it,” Suderman says.
Crawshaw agrees, noting, “Ideally, you want the magnets installed at chest height to prevent an operator from having to reach up or bend down.”
For difficult-to-access locations, POW-R Clean options should be considered where pneumatic cylinders or other actuators can automatically cycle the magnet for cleaning with a simple push of a button.
Automated cleaning is especially important with today’s labor shortage. Non-automated solutions rely on hand cleaning, push/pull cycling of magnetic drawers and other laborious work that has been proven to have disastrous results if a full cleaning regime isn’t enforced, says O’Leary.
“An automated solution guarantees 100% cleaning as programmed to ensure all contaminants are removed from the product flow before they can build up and potentially wash back off and contaminate downstream particulates or damage capital equipment” he says.
“It also ensures the highest quality product will be presented to downstream equipment.”
Magnet technology is getting smarter
Magnetic separation equipment is in a mode of constant improvement. Sources noted rare earth magnetic material continues to develop in terms of its strength.
“Work hardened stainless steel can be removed with magnetic separators,” says Rhodes. “When stainless steel enters the products stream from wear, such as a stainless-on-stainless wear from an airlock, mill or screw conveyor, the stainless steel becomes work hardened and can be captured by a rare earth magnetic separator.”
Magnets are also getting more automated and smarter, driving performance and making maintenance easier. MPI’s new Intell-I-Mag® is an example of the next generation of magnetic separation equipment headed our way."
One thing for sure, there is a greater focus on magnetic separation equipment as an integral part to grain processing and milling facilities now than in the past.
“This means a better back-and-forth between manufacturer and end-user to set a path for a holistic, encompassing program that identifies ideal placement, ideal cleaning option and cycles, and preventative maintenance and care,” says O’Leary.
Data drives performance for intelligent magnet
MPI’s Intell-I-Mag® was recently introduced at GEAPS Exchange in Kansas City as the next step in magnetic separation innovation and facility automation.
Intell-I-Mag is the first intelligent magnet to self-monitor ferrous metal saturation in real-time and log system data.
The patented Intell-I-Mag monitors ferrous contamination of incoming ingredients, detects equipment malfunctions before scheduled cleanings, ensures fully saturated magnets are cleaned before metal events occur, reduces shutdowns for premature magnet cleaning, and ensures the separator is always working at peak performance, capturing weakly magnetic materials such as work-hardened stainless.
“Intell-I-Mag™ delivers an innovative solution for manufacturing facilities impacted by industry-wide labor shortages and cost increases,” says Rhodes.
It also helps reduce challenges due to equipment failures, inadequate magnet cleaning intervals or inaccessible magnetic separation equipment.
Data-driven feedback on cleaning cycles and magnet performance increases production line up time and promotes peak performance of magnetic separators, reducing the risk of a metal event.