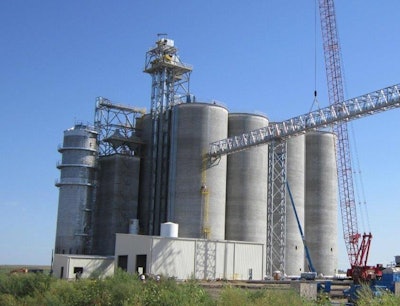
Dan Kowalski, senior manager of CoBank’s Knowledge Exchange, recently published a report looking at shuttle loaders and some of the challenges and issues grain handling facility operators need to consider when building new or upgrading old loading facilities.
Knowledge Exchange is one of the better sources of information on the agricultural service sector that sits both above and below production agriculture. If you have not availed yourself of CoBank’s work, make it a point to visit cobank.or/Knowledge-Exchange and browse through some of their research reports. Reports are well written and reflect the sound approach to business CoBank is known for. Their specialty areas run from the general economy to farm supply, from dairy processing and marketing to grains, oilseeds and ethanol.
Kowalski’s report, titled “Shuttle Loaders Approaching the Saturation Point” begins by looking at the history of shuttle loading facilities. Clearly, there are incentives for railroads to have the most efficient car handling systems available. So began the drive for facilities to quickly load large numbers of cars for movement from the interior grain production regions of the country mainly to export destinations. It was probably not surprising then that the first of these facilities went up in Illinois and Iowa. At the other end, unloading facilities were built in the Gulf.
Deregulation rears new model
Deregulation of the railroad industry in 1980 lead to a substantial restructuring of the industry. Many local lines were abandoned and restructuring was the rule of the day for several years. On the demand side of the house, the United States faced considerable competition from Europe, South America and others which lead to a major decline in exports and the need for grain handling. By the late 1980s and the early 1990s, railroad consolidation was fairly complete, demand had started to pick back up and the incentive for the larger load-out facilities began to resurface. One of the major differences from earlier times however, was that railroads themselves were no longer making that direct investment. Local grain handlers, whether they were cooperatives, independent elevators or multinationals were looked to for the development of new facilities.
The biggest growth came during the 2000s. Coinciding with a large growth in grain production a significant number of operations went in in the western grain belt such as Kansas, Nebraska and the Dakotas.
Why build a shuttle loader?
Kowalski laid out the three reasons for building a shuttle loader as greater shipping capacity, equipment for faster grain handling and access to new markets. One could also add the potential for shipping rate savings.
The reasons to invest in a new shuttle operation vary by the grain handler. Cooperatives for example are probably looking at a facility to gain access to new markets for their membership. By having a shuttle system in place they are able to market directly to export markets or to distant feed lot operations. But Kowalski also points out that for cooperatives in particular, they need to make this as a fully informed and conscious decision and not just build an operation as an attempt to ”keep up with the Joneses.” He posits three questions the cooperative leadership needs to ask: does it make sense, can we afford it and will the return be sufficient. Very careful due diligence, consideration of a joint venture or a merger/acquisition of an existing facility are all options that should be talked through.
For independents or multinationals, decisions around a shuttle loader facility may be quite different than for a co-op. A larger grain merchandiser already has access to export markets and infrastructure. These firms are probably looking more for grain acquisition than marketing options. Traceability, specific customer sourcing requirements and assured supplies can all drive some of these organizational decisions.
Investment considerations
Building a loader is not cheap. Kowalski reports that a 1.5- to 3-million-bushel loading facility will cost in the neighborhood of $25 million to build and will need to see an annual turn in the 17to 20 million bushel range.
Deciding factors
The title of Kowalski’s report, however, focused on shuttle loaders reaching a saturation point. Based on the shuttle facility experts he interviewed for his report, all agreed, “there are very few locations west of the Missouri River that remain suitable for an additional shuttle facility.” Fairly grim views were also expressed for new facilities in the northern Plains states as well as expansion of loaders east of the Mississippi, although the report talked about some optimism for Ohio, Indiana and Michigan. There was also discussion regarding the advantage of unit trains moving from the Western Corn Belt to the west coast as opposed to movement to the Gulf.
Some important fctors to consider on the build or not to build decision Kowalski summarized with:
- “All storage gets filled at harvest. It’s the turns after harvest that matter”
- If you build it, what are you going to do different from a marketing standpoint than you do today? If you’ve lost market share to other nearby competitors, how are you going to buy that share back?
- Fully understand your competition
- If you can get the additional grain, have you thought through all of the factors needed to handle that increased throughput, and not just the loading facility?
- Your grain suppliers may well look toward factors other than a couple cents a bushel when deciding who to market their grain through. Do you have — and will you have after this major capital investment — the financial stability producers will need?
- Be sure to make reasonable margin projections
- Stress test those projections. What happens if the volume drops, what happens if energy costs change, what happens if the rail costs jump or the timing on rail stock availability drags out for extra weeks?
- Will the shuttle loader help to leverage the value of other assets the company owns?
China’s role
The interplay between two competing forces are going to play a critical role in the shuttle loader investment decision process moving forward — ethanol and China.
We have reached the domestic demand plateau for ethanol due to the 10 percent blend wall. The major question moving forward is the behavior of the export market for ethanol. By many calculations, ethanol is the cheapest source of octane enhancement for gasoline. This has made it a very attractive product not only here at home but in international markets as well. Canada and Brazil have emerged as fairly steady markets over the last several months. Future growth in corn demand for ethanol use is probably going to drive more through export markets than what goes on here at home.
Paraphrasing Kowalski ”…success of these facilities is heavily contingent on one buyer: China.” China brings in more grains and oilseeds than the next four importers combined. And their share of overall grain and oilseed imports in only expected to grow. Recent movements by China to limit both grain and ethanol byproduct imports due to lack of approval for specific genetically modified traits has certainly raised concern. The real question is how long they can hold that position.
Since 2007, China has increased their floor price every year. Today, it is roughly the equivalent of nearly $9/ bushel. Over that same time, Chinese corn planting has increased 18 million acres. Their production has grown from 6 billion bushels in 2007 to an expected 8.7 billion bushels in 2014. Their feed use is projected at 6.4 billion bushels and they say they hold 3.2 billion bushels in reserve. So in the short term, at least it looks like they can use excuses such as MIR-162 (the trait of concern) to hold out U.S. product. But the price gap that exists today between their domestically produced corn and what is available on the world market is no doubt going to cause someone to ask about their roughly $20 billion per year subsidy program.
If China continues on their historical growth path while ethanol demand remains flat, shuttle facilities will certainly have a greater likelihood of success than if ethanol demand expands and China decides to look to continue their massive feed grain support.