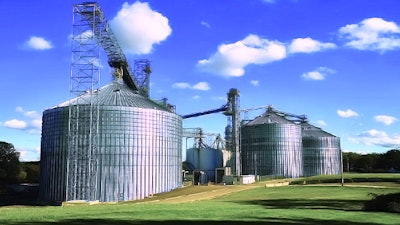
When it comes to commercial grain facilities, planning involves selecting specific pieces of equipment, sizing their capacities, organizing them into a functional system, and then properly locating the system.
The importance of planning cannot be overemphasized. It requires considerable time, effort and thought. Good planning results in a system that works well now and can expand for future needs. It is important to understand the whys and hows of developing a total system for grain drying, handling, processing, and storage.
Consult experienced engineers, knowledgeable equipment suppliers and facility managers with systems similar to the one you are planning. Develop your system with the goal of protecting everyone — owner, operator, employees, customers and visitors.
Locating & developing a grain center
Existing facilities need to be carefully examined relative to present and future needs. It is important to not allow existing facilities to influence the decision on how to build a new grain receiving, conditioning, and storage system. The capacity and condition of the existing material-handling equipment, under-sized dryers, dryers without desired features, and bin size and location may limit efficient, economical use of facilities.
Consider the following factors as you examine each probable site:
Drainage - Avoid areas with surface water runoff problems and high water tables. Select a site with surface drainage in all directions.
Soil - Verify the load-bearing capacity of the soil before the start of construction. Hire a local geotechnical engineer, or verify that the contractor has tested the soil and that soil information is included in the design.
Snow and Ice - Evaluate the snow drop from the grain facility, shelter belts and other buildings. Consider the effect of snow and ice on grain conveying equipment. A southern exposure permits the sun to warm surfaces and assist with melting snow and ice during the cold seasons.
Wind - Determine the predominate wind direction and the impact that wind will have on the facility. Where will grain dust accumulate and/or travel, both on- and off-site? Will blown dust affect any neighbors? Will the wind affect grain unloading or loading? Will it affect dryer performance and the potential for fires? Position the dryer opposite to the prevailing wind to limit the wind’s effect on the dryer’s performance.
Noise - Because fans and other equipment generate noise, create a sound barrier between the grain center and residential areas. Select fans that produce less noise, and, if possible, position them so the sound travels away from houses, neighbors, and other areas occupied by people.
Traffic/Roads - There will be lots of large trucks driving into and around the grain center site. Provide convenient access to the main road and consider the weight of grain transport vehicles. Plan adequate space for snow removal equipment and snow piling. Provide smooth traffic flow through and around all facilities. Plan straight access roads from the main road to the receiving/load-out area for easier maneuvering of loaded trucks.
Security - Reduce the risk of vandalism and theft with safeguards such as locked gates, locked unloading auger motors, lighting, motion-activated cameras, and other trespasser warning devices.
Lighting - Loading and load-out often are carried into the night at times during the year. Effective lighting not only makes the job easier but also improves safety and security at the site.
Electrical Service - Electrical service is a significant factor in site selection. Contact an electrician and power supplier to discuss the availability and total costs for electrical service. Locate the grain center service entrance and control panel near large electrical loads.
Dryers - Dryers are typically near the system hub for easier conveying. Grain dryers and drying systems have many features to be considered, so consult with someone who is able to assist with planning, selection and evaluating the options and proposed system who is not influenced by the sale.
Management Center – The management center can house controls, grain testing equipment, and records or documents. Space is needed for moisture-testing equipment, grading screens, desks, file cabinets, communications equipment, and computers. Likely in an adjacent room are the electric controls and panels in what may be referred to as a motor control center.
Arrangement and Layout - In your plan, always consider the need to remove screw auger flighting for a variety of reasons, including replacement, plugging, or inspection. Arrange the system for easy visual and/or electric control monitoring.
Selecting equipment suppliers and contractors
Find out how long equipment suppliers and contractors have been in business and check with others to find out their experience with the equipment supplier or contractor. Problems often result from poor communication. Verbal communication is easy to misinterpret. Always put the agreement in writing, and have it signed and dated. Too often the only signed and dated paper is the invoice of equipment to be supplied and the price. Other important points to be agreed on in writing are that the equipment will be installed according to the manufacturer’s specifications and that it is guaranteed to operate as specified on the agreement.
Examples of important points of an agreement:
- A dryer will dry a specified number of bushels of grain per hour removing a specified amount of moisture under specified ambient air conditions.
- Conveyors will move a specified number of bushels of grain per hour. In addition, chain or screw-conveyor speed should be specified. Consider the cost of various conveyor sizes relative to conveying speed, because the service life of flighting and bearings is related to chain and screw speed.
- Each conveyor in a conveying series will move 5% to 10% more grain than the previous conveyor to minimize plugging and grain damage.
- Drying, cooling, and aeration fans will deliver a specified airflow rate (cfm/bushel) at a given static pressure.
- Bucket elevators — the buckets’ (cup) capacity should be calculated based on a level fill. Review capacity versus belt speed. Consider features such as access platforms or ladders/stairways.
Before construction starts, also secure an agreement in writing to the following conditions:
- All construction will be completed and equipment installed, in working condition, by a specified date
- A payment schedule and procedure is specified
- Disputes will be resolved by a mutually agreed upon arbitrator
- Topsoil will be removed, and the soil will be prepared according to the equipment manufacturer’s or an engineer’s specification
- Structures require special soil preparation and foundation design and construction to prevent uneven settling and even structural failure
- Concrete will be placed on a properly prepared soil. Concrete will crack due to settling on an improperly prepared surface
- Unless otherwise agreed upon, concrete bin floors will be at least 12 inches above grade
- Building floors and concrete pads under dryers, fans and hopper bottom bins will be at least six inches above grade
- Concrete will be reinforced with appropriately designed reinforcement such as rebar or welded wire
- The mix, curing procedures, and finishes (troweled, broomed, floated, etc.) of all concrete floors will be agreed upon
Plans, specifications and contracts
Detailed documents help provide needed communication, understanding, and agreement between owner, builder and lender. Specifications support the plans; they describe the materials to be used, including size and quality, and they should outline procedures for construction and quality of workmanship.
The agreement is a legally binding contract between the builder and the owner; it includes price of construction, schedule of payments, guarantees, responsibilities, and starting and completion dates. If using a design and construction firm, have the working drawings, specifications and contract reviewed by someone with expertise in designing and building commercial grain drying, handling and storage facilities. It is also recommended to have someone with that expertise provide construction inspection.
Consulting engineers
Consulting engineers commonly offer these services:
- Direct personal service (technical advice, etc.)
- Preliminary investigations, feasibility studies, and economic comparison of alternatives
- Design
- Cost estimates
- Engineering appraisals
- Bid letting
- Construction supervision and inspection
Consulting engineers usually do a project in three phases: preliminary planning, engineering design, and construction monitoring. They may be help with one or more phases. To select a consulting engineer, consider the following:
- Registration — States certify and license engineers of proven competence. Practicing consulting engineers must be registered professional engineers in their state of residence and must be qualified to obtain registration in other states where they offer their services
- Technical qualifications
- Reputation with clients
- Experience on similar projects
- Availability for the project
For additional information refer to MWPS-13 “Grain Drying, Handling and Storage Handbook” available from the Midwest Plan Service at Iowa State University. Topics covered include: planning guidelines, locating and developing a grain center, grain handling, grain drying, grain storage, safety and health in grain drying, handling, and storage, and automation in grain drying, handling and storage.