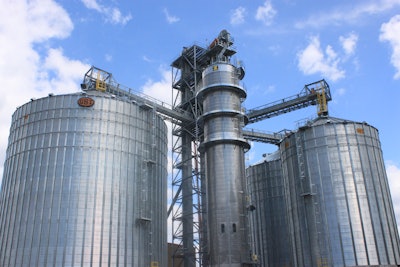
No river in the United States is as important to agriculture as the Mississippi River. Ol’ Man River stretches 2,320 miles and — along with its tributaries — handled 34,946,000 tons of grain in 2014, according to the U.S. Department of Agriculture, Agricultural Marketing Service Grain Transportation Report.
Both facilities came online in August 2015 with the capacity to handle almost constant barge loading activity. Barge transportation is the most cost-effective way to transport grain due to economies of scale. These economies provide for large volumes of grain to be shipped to the Gulf of Mexico where export elevators can ship them worldwide.
“We want to have a tugboat at our dock at all times, bringing us empties and removing loaded barges,” explains Steve Everett, Tunica facility manager. “Ideally, we will take grain during the day and be required to load barges 24 hours/day just to stay ahead of the flow of the producers’ grain.”
Expanding in the Mississippi and Arkansas Delta
CGB has a long history in the Mississippi Delta, taking grain in the early 1980s at its former facility in Osceola, AR, and has been in the West Memphis, AR, market for the last six years. The long-term relationships with producers in the area, along with the rich soils in the Delta, made expansion an appealing prospect for the two new locations. Though historically known for its cotton, the fields surrounding the facilities are now filled with more traditional grain crops including corn, soybeans, sorghum and rice. The transition from cotton acres to corn and soybeans, along with irrigation, genetics and farming, has contributed to steadily increasing yields and greater potential for success in these areas.
“Yields in the area continue to improve,” says Everett. “J
Equipment List |
|
SUPPLIER | EQUIPMENT |
Allen Bradley |
PLC (Programmable Logic Controller) |
ASM Engineering |
Engineer |
Avery Weigh Tronix |
Scales |
CMC Industrial Electronics |
Hazard Monitoring System |
Donaldson Torit |
Integrated Dust Handling System |
Graber Construction |
General Contractor |
Graber Construction |
Barge Loading Spout |
Grain Bins |
|
GSI |
Grain Legs |
GSI |
Enclosed Belt Reclaims |
Hayes & Stolz Ind. Mfg. Co. |
Distributors |
Air Compressors |
|
KDJ Sales and Service |
Electrician |
Lemar Industries |
Structural Support Towers |
Lemar Industries/Intersystems |
River Belt |
Dust Collection |
|
Southern Marine Construction |
River Work |
Union Iron (AGI) |
Truck Probes |
Wintech International, LLC |
Barge Haul Winches |
Zimmerman |
Grain Dryer |
ust a few years ago we were getting 35 to 40 bushels/acre for soybeans, and now we are averaging around 55 to 60 bushels to the acre. Additionally, the farmers’ equipment has also grown, allowing him to fill a semi with corn from his combine every eight minutes. That’s almost faster than you can get a semi out onto the road.”
Since yields in the area continue to grow, CGB has planned for the future. Both locations have plenty of room to expand as the need arrives, and are built to handle almost anything Mississippi Delta producers throw their way.
Ol’ Man River influences construction
Despite raising the facilities’ foundations, high water levels still affected the construction.
“The deep and fast running Mississippi River created many challenges for contractors while they were placing river cells and dolphins,” says Tim Simmons, facility manager at Osceola, AR. “Additionally, the river towers and conveyors were delayed as their bases were under flood waters.”
When building the river structure, water levels are key to what jobs can be done safely and on schedule.
“The river is either too high or too low,” says Everett. “For some jobs, high water is desired while other jobs require the river to be low.”
Even with the challenges, CGB has nothing but praise for Graber Construction (general contractor), Southern Marine Construction (river work), and KDJ Sales and Service (electrical work). Both facilities were completed in just 11 months and were open in time for the 2015 soybean harvest.
Twin facilities
CGB built both Tunica and Osceola for the same reason — speed.
The facilities utilize identical equipment and are designed to get grain onto a barge as quickly as possible. Each facility has 600,000 bushels of storage and is built to move trucks as quickly and efficiently as possible.
“The high-speed capacity at both new locations is intended to reduce producer transportation costs by more efficiently receiving their grain,” says Ed Ide, general manager, CGB. “This in turn reduces costs in truck transportation and increases combine productivity.”
CGB designed the facilities with a race track in mind, providing a route for trucks to transit the facility without having to cross one another. As they enter the facility, the producer will stage his truck in front of the Union Iron probe. At that point, the producer will scan a CGB provided RFID tag that will identify the producer and the hauler of the load. A sample will be taken and as the truck progresses toward the Avery Weigh Tronix scales, the sample will be graded by CGB employees.
“By the time the truck gets to the scales, we have them graded and are able to direct them to one of the four pits,” explains Everett.
Each dump pit is integrated with a Donaldson Torit dust handling system to control the dust from the high-volume operation. Each pit is capable of holding up to 2,500 bushels of grain.
“The pits are huge, even by industry standards,” says Simmons. “Each can handle over two truckloads of grain in the pit without needing to direct it to the river or the facility.”
The goal of both facilities is to dump the producers’ grain as fast as possible. By design, much of the grain will be unloaded immediately onto a waiting barge. If necessary, all four dump pits can be directed onto a massive 60,000-bushel/hour river conveyor belt co-built by Lemar and Intersystems and fill a 1,750-ton barge in a mere hour.
Two of the dump pits can also be directed to send grain through a pair of 24,000-bushel/hour GSI elevator legs and into one of the facility’s three GSI steel bins. If necessary, the grain can then move through a 7,500-bushel/hour GSI elevator leg and into the 4,700-bushel/hour dryer from Zimmerman. The truck then completes the loop as it proceeds to the Avery Weigh Tronix scale and back to the farm.
Transportation differences
Though very similar in look and design, it was a convenient coincidence that the facilities were built at the same time. CGB had been evaluating both locations for months, and the investment happened to fall into place simultaneously for both.
Due to differences in location, the facilities have slight variations in layout and strategy. Osceola was built on a smaller plot of land north of Memphis, TN, which led to a tighter truck traffic loop, closer to the water.
“Everything sits in a much tighter area in Osceola,” explains Simmons. “So even though both facilities look the same, there are technical differences of each in moving product to the river.”
Another major difference between the two facilities is their local barge fleeting services. The Osceola facility was built in an established barge fleeting market, and was able to utilize existing infrastructure to provide its barge fleeting for the facility. Tunica, on the other hand, is 30 miles from any available fleet operation and was required to install its own fleeting capabilities. The one advantage of Tunica is the plan to avoid the busy Port of Memphis when moving barges on the river.
“CGB built these two facilities to help its producers achieve success in their farming operations in Tunica and Osceola well into the future,” says Ide.