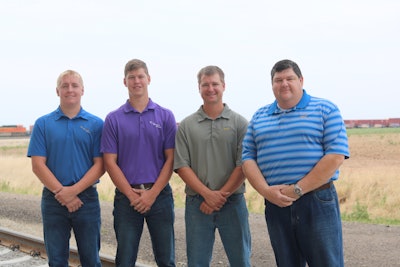
Cooperation is something that comes naturally to cooperatives. After all, it’s in the name! The mission of a cooperative is for a group of members to pool their resources and knowledge to realize a better outcome than they could have alone, and share the positive returns. Nowadays it’s even common for cooperatives themselves to team up for the benefit of all parties.
One shining example of what collaboration can achieve is Producer Ag, LLC, a 50/50 joint venture made up of partners MKC and Team Marketing Alliance (TMA), along with CHS, Inc., the nation’s largest producer-owned agriculture cooperative.
Moundridge, KS-based MKC has been serving central Kansas since 1965 with more than 40 locations, while TMA is a grain marketing firm owned by MKC and three other cooperatives: Farmers Cooperative Elevator Co, Halstead, KS; Cooperative Grain and Supply, Hillsboro, KS; and Farmers Cooperative, Nickerson, KS.
With MKC serving as Producer Ag, LLC’s operations wing, TMA providing marketing services and CHS, Inc. contributing a substantial amount of capital, an all-star team was born. The team’s mission was to bring rail access, state-of-the art equipment and loads of storage to producers in Central Kansas, which it achieved in 2015 by opening its first location, a shuttle loading facility in Canton, KS, on the UP Railroad main line.
After its success in Canton, the team recognized an unmet need for a cooperative owned rail terminal in the South and elevator space in Sumner County (about 90 miles south of Canton), an area known for producing some of the country’s highest wheat volumes.
“There are shuttle loaders within 35 miles to the south and there are some about 15 miles to the east [of Milan, KS],” explained Jeff Jones, director of Southern operations, MKC. “But those are not cooperative-owned shuttle loaders, so we wanted to be able to bring the cooperative model and value stream to the local growers in this area.”
Starting in mid-2015 MKC and TMA spent about a year planning — searching for a site, finding the right railroad partner, the right piece of ground for the loop track and evaluating bids from various construction companies.
Their analyses led Producer Ag LLC to select Milan, KS, as the site of its second location, another shuttle loading facility with 7.2 million bushels of storage capacity and access to the BNSF’s main line destined for ports in the Gulf of Mexico.
Producer Ag LLC chose SMA, LLC of Monticello, MN, to build the massive complex, including a 4-million bushel Chief Agril/Industrial flat storage building, an eight-pack of 150,000-bushel concrete slip formed bins, three 500,000-bushel concrete slip-formed bins and four 25,000-bushel/hour BCI bucket elevators. SMA, LLC’s bid impressed MKC by committing to a lightning fast turnaround.
“This company doesn’t cut corners,” Jones said. “This was an 18- month project that they completed in 13 months, which is almost unheard of. Construction started in May of 2016 and we were open by June 1, 2017, so you can tell they were pushing the whole time. At times there were well over 300 employees working on this jobsite. We were very fortunate to have found a company that could bring in enough employees for this job.”
The two-mile loop track, including switches going both east and west and a rail spur, was a completely separate project awarded to New York-based Railworks — North America’s largest provider of track construction and maintenance services.
The BNSF railroad was another integral partner in the planning of Producer Ag, LLC’s 120-car loop track.
“BNSF was excited to partner with us and have the opportunity to move Sumner County grain down the line,” said Jones. “We worked with them hand in hand as we put in the spur and loop track.”
Automation and handling
Although Sumner County is known for its wheat, the region surrounding Milan is home to an abundance of crops and the facility stays busy with canola and wheat harvested during the summer, and corn, soybeans, and milo in the fall. With such a variety of crops and the high volume of stored grain to manage, Producer Ag, LLC spared no cost on facility automation. It chose Kasa Controls & Automation to provide these services from grain receiving through routing to load out via rail or truck. The process starts with incoming trucks outfitted with RFID tags approaching one of the two inbound lanes of traffic. After the trucks are probed and sampled, they proceed to one of two 80-foot-long pitless scales where their weight is captured and dump pit is assigned.
The staff is able to analyze samples quickly thanks to its two testing labs, both equipped with moisture meters, dockage testers and mycotoxin testing equipment and supplies. Next, trucks proceed along the route to the receiving building with three 1,200-bushel/hour receiving pits. A fourth receiving pit rated at the same speed is located just outside the building and opened when they need to keep operations running smoothly or
are handling multiple crops, such as wheat and canola.
Once dumped, the grain is directed either to one of three HI ROLLER 25,000-bushel/hour enclosed belt conveyors or a 60,000-bushel/hour enclosed conveyor and ascends one of its four identical receiving bucket elevator legs to be conveyed and distributed into storage at the top. Trucks are scanned and weighed again on the outbound scale after dumping, with the whole process taking approximately 8 to 10 minutes from scale to scale.
Quality storage measures
At maximum capacity, the Milan facility can hold 7.2 million bushels of grain. More than half of this volume can be held in its 4-million-bushel flat storage building. The contents of the 700-foot-long by 200-foot-wide structure are carefully maintained with more than 100 temperature cables and 47 AIRLANCO fans for aeration and a CMC Industrial Electronics temperature monitoring system, explains Lawson Hemberger, grain operations manager, MKC.
“All the fans are tied into the automation system, so they can be set to automatically maintaina certain temperature, humidity and other settings,” Hemberger began. “There is even a dryer and a cooling setting that work with our temperature cables. We have plenty of temperature monitoring, so if there ever happened to be an issue, the system would catch it and give us an alarm.”
The building has two 20-foot stem walls, which were designed to give them the option to hold three different commodities or to segregate different grades of a commodity. Hemberger said the facility hadn’t had the opportunity to use this feature since the incoming wheat harvest was so abundant this year. The building was 85% to 90% full of wheat at the time of Feed & Grain’s visit in August.
Grain enters the building on two conveyor belts and the automation system uses lasers and trippers to signal where inside to release the grain. To remove grain from the building, they use a front-end loader to push it onto an underground conveyor belt into a tunnel below the building. Jones commented on the difference in quality between grain piled on the ground and grain held in their flat storage building.
“Many grain bunkers in this area are only protected by tarps,” Jones said. “But here we have concrete floor, the aeration system with fans that we can monitor and automate. The difference between this and a pile is night and day. The quality is very similar to grain stored in an upright concrete bin.”
The other 21 concrete bins are equally well managed and monitored. A group of 5,000- to 151,000-bushel cement slip-formed bins, referred to as the blend house, allows for the opportunity to keep a variety of different grades separate if they start receiving wide variances in quality or moisture. The three half-million-bushel bins are used for large volumes of uniform grain, and the flat storage is considered long-term storage.
Hemberger said the design is working well for their current needs, but there is room for growth if needed. A three-phase plan was put into place from the beginning, which made room for another two 4-million bushel flat storage buildings and multiple additions of steel, jump-formed, or slip-formed bins.
Loop track operations
In July 2017, Producer Ag, LLC began loading railcars. The loop track is capable of holding a 120-car unit and an additional five cars on the spur. Currently the largest shuttle on the BNSF is 110 cars and it takes a six- to seven-person crew between 7 and 8 hours to prepare the train, load it, and properly close the cars before departure.
All of the four grain receiving legs also serve as shipping legs with a click of the automation system. Grain destined for rail passes through a C&A Scales bulkweigher, which is integrated with Cultura’s one-Weigh scale automation system. Employees utilize safety restrains outfitted by Fall Protection Systems Corp. while working above the railcars. With the speed, space and technology of some of the largest players in the industry, Producer Ag, LLC has become quite a successful venture for its parent companies. But Jones emphasized that Producer Ag, LLC has also brought local cooperative value to its growers by building on MKC’s motto of “Shared growth. Shared Success.”
“We’ve helped a lot of farmers be successful this year with the basis increase in this area,” said Jones. “And it’s not just for MKC growers, but it helps all the growers and other cooperatives here. That matters to Producer Ag, LLC because we’re a locally owned terminal, not a large corporation. Our leaders and employees are local to this community and deeply invested in Sumner County.” ❚