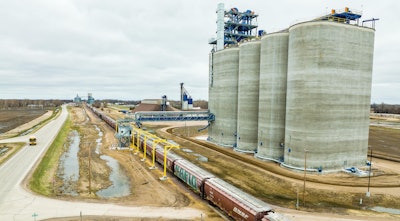
For decades, as automation in grain handling has evolved, the industry has dreamed of the idea of a “lights out” grain elevator — automated to the point it can operate without staff in the physical building.
Using clever automation, CHS has come closer than ever to that dream with its state-of-the-art grain elevator in Herman, MN..
New elevator needed to meet producer's needs
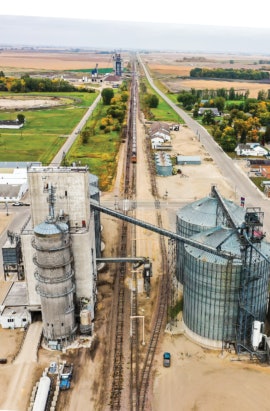
CHS had a presence in Herman for years while operating the local shuttle loading facility near the center of town.
But after several upgrades and renovations, eventually, CHS’s management concluded that due to the elevator’s age and location, it would never match the local producers’ needs.
“The producers are so quick at taking the crop off, and we weren’t able to dump enough trucks per hour at the elevator,” says Jerry Kramer, CHS general manager based in Herman, MN. “We had many days with long lines because we just couldn’t get enough trucks through. To satisfy the modern producers’ needs, we needed to get them through much faster.”
Kramer says they looked long and hard at how to upgrade and improve operations in town, but at the end of the day, it was going to be expensive and similar to what they already had. They decided the best option was to build a new grain elevator elsewhere.
“We owned some property just outside of Herman with a 32,000-ton fertilizer plant and a main office and acreage to build on,” says Kramer. “Building new allowed us to have a fresh start and do it the right way.”
The team at Herman worked with CHS’s internal construction department to design a new grain elevator with the speed and space needed to keep up with the area’s producers.
The team toured other newly built grain elevators, talked with contractors, and based their final design plans on suggestions and features seen on their elevator tour.
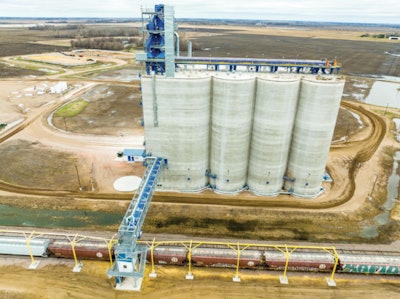
Advanced automation shortens wait times
The long lines producers experienced during peak times were one of the most important factors that went into CHS’s decision to build, so it’s no surprise speed is the star of the new location.
The new elevator has three dump pits rated at 25,000 bushels/hour per dump pit, giving the new facility a total rating of 75,000 bushels/hour, says Kramer.
They can also dump another 25,000 bushels/hour at the older uptown location, giving them the ability to dump a total of 100,000 bushels/hour of grain in Herman.
“Producers no longer feel like sand trying to go through the hourglass in the same spot,” he says. “It makes for a much better experience for our growers.”
When a grain truck arrives at the new facility, the driver swipes an RFID card to check in, pulls to where the truck will be probed and has the grain graded.
The driver then pulls forward to be weighed and proceeds to one of the three 25,000 bushel/hour dump pits based on the grain grade.
After dumping the grain, the driver pulls onto an outbound scale, swipes their RFID card, is weighed and receives their ticket.
After being dumped, the grain is conveyed to one of 17-grain bins — eight large 165,000-bushel silos and nine smaller bins — totaling 1.4 million bushels of onsite storage.
CHS also has an additional 2 million bushels of storage at its other Herman location. Grain leaves the elevator on 110-car trains loaded by an 80,000 bushel/hour rail load-out system.
During the entire process, the employees are aided by automation to ensure the best experience. The automation is so advanced that a single person could operate the entire elevator.
Many companies would be content with that level of elevator automation, but the team at CHS wanted to push the technology even further and operate it with the “lights out.”
Automated truck probing needed for unmanned operation
Perhaps the hardest step to overcome when creating a fully automated grain elevator is the first one — truck probing.
To assign a grade to a shipment of grain, multiple samples must be taken at several points throughout the load. But with dozens of different types of trailers delivering grain, the chance of an automatic probe hitting a truss or bottom of the trailer is high.
CHS had to create a system that could reliably provide a proper grain sample and not damage any equipment.
The workflow of a completely automated grain elevator would be virtually the same as a typical elevator, explains Kramer.
The difference is in fully automated mode, each truck will have a small puck, usually just behind the front of the trailer. The first time that trailer is probed by a human, the puck stores data on the spots where the probe was lowered and how far down the probe was moved, along with the position of the trailer on the scale.
“When that truck returns, the probe will transmit that data back to the probe, telling the probe where it should take samples based on the truck’s new position,” says Kramer.
The fully automated system then tests the grain and sends the driver to the correct dump pit based on the test results.
The driver proceeds to the appropriate traffic route. “We’re also setting up safeguards for common issues that may come up,” says Kramer.
For example, what happens if a driver goes to a different dump pit than they were told? The puck on that truck will communicate with the puck reader at the dump pit.
“The system will then catch the driver’s mistake, instruct them to wait, clear out the system and reroute the conveying system so grain makes it to the right bin despite the mistake without a single employee getting involved,” says Kramer.
One benefit of a fully automated facility for CHS’s producer customers is extended delivery hours without worrying about the local grain elevator’s hours. But the biggest advantages will be felt by the elevator employees.
Grain elevator automation improves work-life balance
The grain industry often asks a lot from its employees. During peak seasons, 12-hour days, weekend shifts and holiday shifts are common.
With less rural labor available, work is spread across fewer hands, forcing managers to schedule longer shifts and place higher expectations on individual output.
“When we talk about this plan, everyone assumes we want to lower the number of employees we have,” says Kramer.
“We don’t want to reduce our employee numbers. We want to provide them a proper work-life balance.”
Proper work-life balance ensures employees aren’t fatigued, making them safer, more productive and more content.
“Our goals were to give employees a better work-life balance and improve our customers’ experience,” says Kramer. “Elevator automation should accomplish those goals.”
Building a high-tech grain elevator during the pandemic [Sidebar]
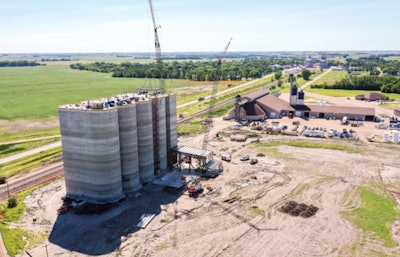
CHS started the construction of its state-of-the-art facility in Herman, MN, in the late summer to early fall of 2019, but the actual elevator was scheduled to be slipformed in May 2020.
Of course, in the spring of 2020, the first large wave of the COVID-19 pandemic hit the U.S., creating unique challenges for the build.
“Back in May 2020, we were still learning about what the pandemic was,” says Jerry Kramer, general manager, CHS.
The slipform should have taken about six and a half days, says Kramer, but they couldn’t get a full crew.
“Workers were nervous about coming into a place they knew nothing about,” he says. “And the local people around Herman weren’t excited about us bringing in a bunch of outside workers.”
The slipform concrete pour took 12 days instead of the six-and-a-half they hoped for.
A longer pour wasn’t the only obstacle. CHS also needed to separate the construction crew from the city’s residents to help make employees, contractors and the community comfortable in an uncertain time.
The company fed employees at the worksite at the start and end of their 12-hour shifts, keeping them out of the local eateries.
“We had several conference calls with local health professionals ahead of the slip just to make sure we had the right protocol in place and we’re doing things as safely as possible,” says Kramer.
It took longer and required more creative problem-solving than normal, but CHS was able to build a grain elevator that would give plenty of speed and space.