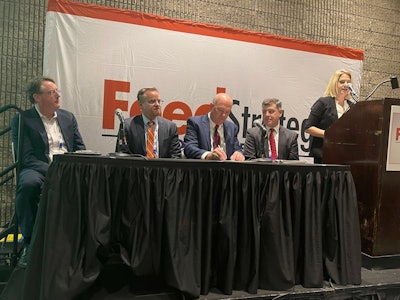
During the 2022 Feed Strategy Conference, a panel discussion, led by Feed & Grain Editor Elise Schafer and featuring leaders in the various segments of animal feed production, explored what the future of feed manufacturing may look like and what technologies may shape the feed mill of tomorrow.
Panelists included:
- Scott Anderson, general sales manager, California Pellet Mill (CPM)
- Peter Ensch, CEO, WEM Automation LLC
- Loren Field, executive vice president, Younglove Construction
- Aiden Connelly, president, AgriTech Capital
Past periods of growth in the feed industry have always been spurred by novel events. Today’s labor shortage is one such event, and panelists agreed it’s one of the top challenges facing the industry today.
“It seems we’re at a momentous moment in our history with this critical labor shortage,” said Aiden Connelly with AgriTech Capital. “While we need people to work in processing plants, we need people to milk cows and we need people to work in feed mills, it’s just not an attractive career.”
“It’s such a huge issue and we’re seeing a lot of investment in technology going here.”
Connelly noted that trends they were seeing with automation – robotics, sensors, artificial intelligence, camera vision – were greatly accelerated with the advent of COVID-19. It’s become critical to replace the people lost or who have left because of the pandemic.
“It seems clear where these trends are going,” he said. “Elimination of labor as much as we can.”
Scott Anderson with California Pellet Mill (CPM) agreed, noting that this is the challenge equipment manufacturers need to pick up.
“Looking at different business models of the future, interfacing with technologies is certainly a critical limiting factor on that ability,” said Anderson. “Things like predictive maintenance, remote support and balancing those challenges with cybersecurity concerns.”
Peter Ensch with WEM Automation noted a trend around data collection and data curation that will come into play with future feed mills.
“This is an opportunity here more than a challenge,” said Ensch. “We have a lot of data being collected right now. How do we turn that into useful information? That’s where analytics comes in. It’s easy to gather gigs of data, but you have to make that into something that you can make business decisions with.”
Adding a layer to the labor issue, Ensch points out feed mills will have to recruit employees with higher a skill set to do analytics.
With the pandemic and labor shortage, remote work is a daily reality for many businesses. Will the time come that feed mills are run out of remote offices?
“We talked with several producers during the initial stages of COVID about doing a central control location which runs multiple feed mills,” says Ensch. “There are challenges with internet and having the speed to manage the control piece of it.”
Ensch notes the central location helps share a pool of people that are used as needed.
“The technology is there, it’s pulling it together,” he says.
The ‘lights out’ concept – running a feed mill facility with no employee interaction – will push the industry to the next level of preventive maintenance.
“We continuing to engineer technologies for equipment, the pellet mill in particular, to be more reliable,” says Anderson with CPM. “Sadly, we’re a long way away from a pellet mill being truly hands-off.”
Loren Field with Younglove Construction says he hasn’t seen anyone embrace the ‘lights out’ concept yet.
“That’s a quantum leap from how feed mills are being built and operated today,” said Field. “The technology for a remote, central control room is there. But as far as the equipment maintenance function, wherever there’s a mechanical piece of equipment, there will eventually be a broken piece of equipment. And human hands will have to touch that.”
Anderson notes Field’s point dovetails with artificial intelligence which equipment manufacturers have to focus on to improve predictive capabilities of equipment maintenance in order to help customers to address situations before they get to a break down.
“Mountains of data is one thing,” he said. “But knowing how to understand it and convert it into an actionable item is key.”
For more insight into the Feed Mill of the Future, click here.