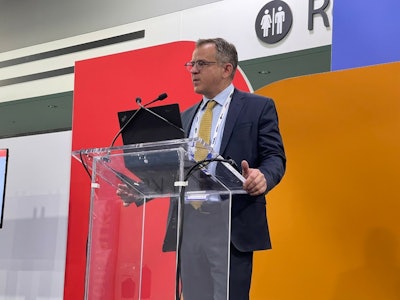
At a TECHTalk Thursday afternoon during the 2022 International Production and Processing Expo (IPPE), Peter Ensch, CEO, WEM Automation, explained how an MES system can improve a feed mill’s energy management.
First Ensch explained how an MES system can manage, monitor and synchronize the execution of real-time physical processes involved in transforming raw materials into intermediate work-in- process and then finished goods. They coordinate the execution of work orders with production scheduling and enterprise-level systems.
“MES was designed to provide flexibility between the interfaces that make up the production process and the management of reporting using analytic tools and dashboards,” explains Ensch.
Specifically, MES focuses on digitally logging events as they occur. MES logs the flow of each step within your production process including receiving, grinding, batching, pelleting, material transfer, loadout, warehouse and order fulfilment confirmation. MES also interfaces with other systems in your organization to move data up and down as directed by your operation.
What is energy management?
Energy management is the process of collecting information about where, when, how and why energy is being used in a facility, so you can increase efficiency, reduce cost and improve sustainability.
The process involves collecting accurate, real-time energy data using IoT sensors, analyzing this data with software to highlight areas of inefficiency and taking action based on the results.
According to Ensch, there are four steps to implementing energy management.
- Build a strategy
- Gather the data (real-time and historical)
- Analyze the data to transform the energy usage data into useful information
- Interpret the results and agree to an action plan
When building a strategy, Ensch says the first items to consider is the goal and scope of it. This would include cost reduction, production uptime, sustainability – or a little bit of everything. Set goals with measurable target values.
“If you want to control something, you have to measure it,” says Ensch. “Energy management starts with monitoring.”
He says to use the 80/20 rule to start. “Most facilities, 80% of your energy is consumed by 20% of your equipment,” he notes.
To gather data, install meters, submeters, current transducers and sensors. Connect these to a PLC (programmable logic controller) and SCADA (Supervisory Control and Data Acquisition) system so data can be directly input to the control system and tied to production data.
Interface the MES software to tie data to both transaction and production data. Then use SCADA for real-time trending and historical for long-term trending.
The next step is to analyze the data to transform the energy usage data into useful information, says Ensch.
“We recommend hiring an energy consultant,” he says. “There’s a lot of resources out there to help you figure the data out.”
Ensch notes many states have programs and grants to support local projects in the manufacturing sector. He also suggests using EMS (Emergency Management Software) for data analysis and ongoing monitoring/alerts.
The last step is to interpret the results and agree to an action plan.
“With any continuous improvement project, use data to drive your decisions,” says Ensch.
Treat it as a project with a detailed action plan.
“You need to follow up, follow up, follow up,” he says. “Monitor your progress and adjust as needed.”
For more information, visit WEM Automation.