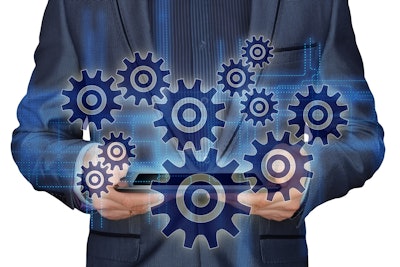
Grain and feed managers know that hiring staff can take up a large amount of your time, with mixed results. The long demanding hours and a lack of awareness among the general population about careers in the grain handling and feed manufacturing industries have led to a nearly constant labor shortage in those industries.
And grain handlers and feed manufacturers know that the labor problem will not disappear, but it can be alleviated with automation.
Upgrading the automation and control systems at your facility can save you man hours, create a more attractive workplace to new talent and even improve the work-life balance of your existing employees.
What upgrades should you make to best alleviate your labor shortage? Automation experts in the industry shared their ideas.
Some of the automation ideas below will seem basic to someone working in a new feed mill or grain elevator but are needed in large parts of the industry for facilities to continue to be operational.
“There are just so many tons of feed being produced all over the country with pretty limited automation,” explains Brady Gaalswyk, co-president/owner at Easy Automation. “Maybe they've implemented some of the basics, such as the batching system, but have a lot to gain in terms of taking existing automation and just adding something like receiving a reclaim. It's crazy the amount of feed mills where people are still watching it and running it manually. Maybe you can get an older facility to the level that new facilities are at, but there's a lot of good automation and process improvements that we can implement into an existing facility to really help things out.”
Data integration
Are there people at your facility still manually entering information into your control systems? No one at the feed mill should be entering formulas for batching, weights from the truck scale or lot numbers for ingredients. Almost every price of equipment within a feed mill can communicate with automation and control systems, auto-populating the information that once had to be hand entered.
“When I started, we would have to manually key in every material that the operator was going to use,” explains Dale Skomar, senior applied systems technician for Comco. “Now, we can actually import those things. And in some cases, we're actually importing recipes for each production run that are specific to that production run. Eliminating that type of work on the inputs to the control system, so you don't have to have somebody sitting at a keyboard, doing all of that manual data entry.”
“Employees will be freed up to actually be able to do other tasks, rather than simply monitor the equipment," Skomar continues. "The system is kind of keeping track of mundane tasks.”
Don Goshert, vice president of Sterling Systems & Controls, agrees, “When we're going to feed mill, they are not currently tracking the data automatically; it's being written down by hand. Digging through manual logs is time-consuming. Now you should be able to type in ingredient lot numbers and pull up the information to see exactly where it was used, which batch it was used for and what customers needed that. I would say probably 20% of our customers are there now, and the rest of them are catching up. They're still doing it manually.”
Equipment monitoring and maintenance
One of the best ways to control labor needs is to make sure that a feed mill or grain handling facility doesn’t experience downtime. Data integration from facility information means an automation system can keep track of how much the equipment is being used and automatically repeat that data to facility staff.
“Maintenance software tells the maintenance staff the hours of motors, when bearings need to be greased, those kinds of things,'' says Goshert. “That's the kind of a thing that people rely on more and more because they are short staffed, and it can be hard to remember everything that needs to be maintained and greased and oiled and recalibrated and so forth on a maintenance schedule."
Management and employees no longer have to keep track of manufacturer-recommended maintenance schedules. The system will raise the alarm when a maintenance task needs to be done. Fewer equipment breakdowns mean more employees get to work their shift and leave on time, creating a better work-life balance and saving the company money.
“As the pieces of equipment have gotten bigger, many more tons are getting pushed through that single piece of equipment,” explains Gaalswyk. “That single piece of equipment has been relied on to feed more animals than ever. So we just have to make sure that that piece doesn't fail, and maintenance modules help that.”
Micro ingredient systems
Adding micro ingredients by hand is a time-consuming, labor-intensive, messy and mistake-prone area of feed manufacturing that can be primarily cut from a feed mills workflow with a micro ingredient system and control system. Micro ingredient systems are nothing new, but with automation, they’re more accurate and take less monitoring than ever before.
Even when ingredients have to be hand added for a custom feed mix, molders hand ad stations weigh and record the ingredients added to the mixture. A modern micro ingredient or hand add system will make a feed mill more accurate and save employees from the backbreaking task.
“I think about that first feed mill that I was involved in,” says Goshert. “I saw three to four people just running around the place, with weigh buggies. They were working really hard. I came back to that plant a couple of years later after they had installed a micro ingredient system that cut their hand adds 80%. They were down to one operator, and some of them gained quite a bit of weight over the years.”
Eliminating heavy lifting, like 50 to 100-pound micro ingredient bags, will increase efficiency, make employees happier and create a safer work environment.
“We've seen more and more people putting in micro ingredient systems or larger micro ingredient systems,” says Gaalswyk. “No longer having to do quite so many hand adds, or going from 50-pound bags to 2000-pound bags, means less carrying and less hauling. These are the types of activities that otherwise somebody would have to do manually for every single batch of feed that is made.”
Automation efficacy reduces hours
No matter how good an employee is, there are just some things a computer will do better. One of the selling points of an automation system is that it cuts down on human error. The software will not open the wrong gate or write down the wrong number if all of the inputs are set up correctly. But by doing tasks like data entry faster than a human ever could, an automated mill or elevator can achieve the same results in less time, meaning a business can run with fewer shifts.
“Say you have 10 people/shift running a 24/7 schedule to meet demand at your facility. By upgrading or installing an automation system, you can run 24/5, and maybe have one or two people on the weekend to just do deliveries and maintenance work,” says Skomar. “You don't actually have to run that same amount of time to meet that same production amounts.”
Adding control and automation systems may feel expensive and overwhelming when coming from a low or no automation mill. When talking to an automation specialist, focus on a few areas of the facility that are currently trouble spots or bottlenecks. Remember, not everything needs to be done at once; even small changes can save a facility many man hours and make it a better place to work.