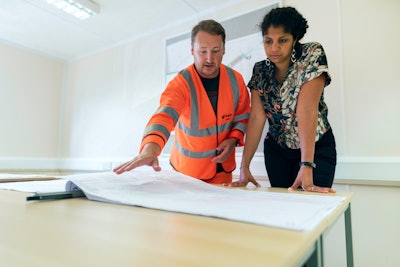
For the past few decades, technology has played a critical role in the feed and grain industry’s growth, paving the way for increased safety measures, throughput, compliance and automation.
When selecting an electrical design-build contractor for a facility upgrade or new build, it’s important to review their qualifications and capabilities, as well as the industry experience they bring to the project.
Sure, hiring an electrical or automation contractor will get the job done, but hiring one with feed, grain and National Fire Protection Agency (NFPA) knowledge is a game changer.
Safety procedures such as Lockout/Tagout (LOTO), energized work permits and arc flash/electrical safety policies were created as a secondary means of protection to reduce accidents from happening while equipment is being serviced or repaired. By properly designing the electrical and control system with NFPA compliance in mind, we can eliminate the risks for putting people in hazardous situations.
Installing smart motor control centers (MCCs) allows remote troubleshooting and monitoring via the plant control system or by a handheld interface, eliminating the need to open the MCC bucket or PLC cabinet.
Smart MCCs can monitor system voltage, amperage, reset overloads and view input status from machine-mounted sensors without the need of arc flash gear or using a meter.
Smart MCCs also allow your machine-mounted sensors to be wired back to the MCC bucket versus the PLC, proving one point for lockout of a 480-motor power and 120V control power.
This wiring can help eliminate the frequent OSHA violations through good design, such as failure to LOTO on 120V circuits and completing energized work permits required in NFPA 70E.
Installing remote-operated main circuit breakers in standalone sections isolated from feeder breakers allows you to isolate your highest rated arc flash equipment from the equipment that the plant will normally operate, mitigating the risk to them should an incident occur. It also allows the commonly labeled RHC dangerous main breakers to be operated remotely and out of the flash protection boundary.
Working with a knowledgeable design partner and taking the time to plan an upgrade or new facility build strategically will save you headaches, time, and money in the long run. ■