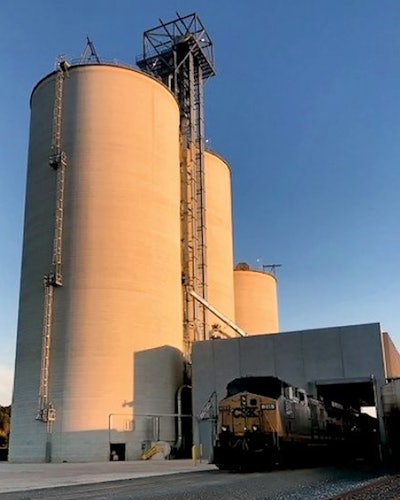
According to the National Chicken Council, on average, Americans consumed 93.5 pounds of chicken in 2018. The nation’s appetite for chicken has created a $95 billion yearly market for chicken products. Pilgrim’s, the nation’s second-largest chicken producer, provides one in five of those chickens eaten by American consumers, according to the company’s own data. In an effort to meet America’s demand for high-quality poultry, Pilgrim’s has continued streamlining and improving its processes for the past 70 years. This tradition continues with its new poultry feed mill in Ranger, GA.
Innovating & improving
Pilgrim’s was founded in 1946 when Aubrey Pilgrim and Pat Johns formed a partnership and bought a feed store for $3,500 in Pittsburg, TX. Lonnie “Bo” Pilgrim, Aubrey Pilgrim’s brother, was soon brought into the partnership. The trio began to sell baby chicks along with their feed to diversify their business. Selling the chicks that would go on to eat feed from their store is heralded as an early example of a vertical integration business model for poultry production. The vertical integration business model involves one company owning and operating multiple stages in the production process and is still used by every significant poultry company today.
Though it started as a small $3,500 company in Pittsburg, TX, Pilgrim’s has grown into a company that provides more than 133 million daily servings of food globally. It operates in 14 states as well as Mexico and Puerto Rico.
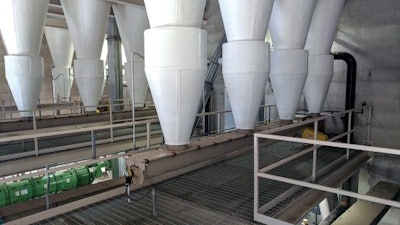
To achieve this level of growth over the past 70 years, Pilgrim’s has continued to innovate and improve its operation and expand how many production processes it handles in house. Pilgrim’s not only sells feed and chickens, it also manufactures its own feed.
The ethos of innovating and improving instilled by Pilgrim’s founders continues to this day. When the chance to replace two aging facilities with one new facility in Ranger, GA, while still meeting local poultry producers’ demands, the company jumped at the opportunity.
“There were two reasons for the new larger facility,” says Jamison Pass, feed mill manager at Pilgrim’s. “The first was to replace and combine two aging facilities, the Calhoun, GA, feed mill and the Canton, GA, feed mill, into one to better serve our customer base. The other reason, for the larger facility, was to have the availability to accept 90-car unit trains, as neither the Calhoun nor Canton feed mills can.”
Located an hour north of Atlanta, Ranger offers highway access as well as the capacity to accept 90-car unit trains. The location allows the feed mill to bring in its raw materials on a train then ship by truck NAE (no antibiotics ever) and NAIHM (no antibiotics important to human medicines) feed mixes to the surrounding farmers depending on what type of chicken they are raising for the market.
Not only will the feed mill help local contracted family farms, it will also help the local economy. “The Ranger community will definitely benefit from the new facility,” explains Pass. “Not only will it greatly increase local revenue streams from the incoming and outgoing traffic, but it has also provided nearly 50 new employment opportunities to the area.”
Drilling & blasting
Once the mill was approved and Pilgrim’s awarded the contract to design, engineer and construct its new feed mill to Todd & Sargent, work began on the new poultry feed mill in 2017. In order to begin work, Todd & Sargent had to remove 650,000 cubic yards of dirt at the site. Afterward, it needed to drill and blast another 200,000 cubic yards of stone in order to prepare the site. Luckily, the company was able to put all of that stone to use as the bed of the new railroad tracks and throughout the mill site.
Todd & Sargent began driving piles, pouring below-grade concrete and prebuilding the slip forms in the fall and winter of 2018. Work continued through 2019-2020, with the feed mill becoming fully operational in November 2020.
The new Pilgrim’s feed mill used slipform concrete construction for all of the buildings onsite. The main feed building, truck and rail loadout and receiving, two silos of whole-grain storage, and a smaller soybean meal silo were also built with concrete.
Efficiency & capacity
The feed mill will bring in 85% of the raw ingredients it uses through a rail receiving system rated at 60,000 bushels/hour for corn and 560 tons/hour for soybean meal. The other 15% will arrive via interstate commerce to the facility’s truck receiving system rated at 15,000 cubic feet/hour or 330 tons/hour. The truck receiving building has an addition of a corn loadout system in order to distribute and sell corn to other mills within the area.
Raw bulk ingredients are routed to one of two concrete silos that hold 900,000 bushels of whole grain or the 2,600-ton soybean meal silo. Other ingredients are placed in one of 27 ingredient bins with a total capacity of 4,100 tons.
“The process of feed production begins with the receiving of ingredients,” explains Pass. “Then raw ingredients go through a batching process where they’re mixed thoroughly. The mill has two batching systems consisting of one 12-ton twin shaft mixer, one 8-ton twin shaft mixer from Scott Equipment, two CPM Beta Raven 20-bin micro bin systems and two four-bin tote systems.”
The facility’s mixing and batching lines are capable of churning out 240 tons/hour. The mill’s grinding system consists of three CPM Champion hammer mills capable of grinding 120 tons/hour of material into a fine grind or 60 tons/hour of a coarse grind.
“Once the raw ingredients have been adequately mixed, they then go through a pelleting process,” says Pass. “Pelleting requires the addition of steam/heat to allow for the pelleting process through the pelletizing equipment.”
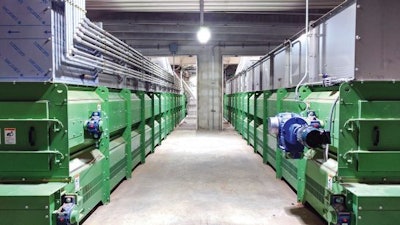
Pilgrim’s mill can produce 225 tons of pelleted feed through three CPM pellet mills capable of pelleting 75 tons/hour each.
“The pellets then run through the cooling process, allowing time for the pellet to harden and to withdraw excessive moisture from the feed,” explains Pass.
Each line has a conditioner, horizontal cooler and crumbler built by CPM.
“Once the pellets are cooled, the feed is then routed into the final step, which is the application of liquids. This process is completed with an APEC liquid coating system. Once liquids are applied to the feed, the feed is then routed to a storage bin where it will remain until ready for shipment — typically within 24 hours for quality purposes.”
The finished feed is stored in 24 bulk loadout bins placed over dual driveways. Pilgrim’s uses two trucking contractors with a combined fleet of 25 bulk feed bodies and 40 drivers. A truck arriving at the facility is weighed by Rice Lake truck scales and sent to one of the two loading lines.
Once inside the loadout building, a truck takes just seven minutes to fill with feed and is then weighed again before beginning its route to one of Pilgrim’s contracted family farms.
Grain and feed are moved through the facility with a combination of drag conveyors and bucket elevators from InterSystems, WAM screw conveyors and a turn head distributor from Hayes & Stolz. Dust is controlled with a dust collector from Schenck Process and a central vac system from Walinga. In such a large plant with this quick of a turnaround, one of Pilgrim’s most critical pieces was the automation system.
“Our automation partner is CPM Beta Raven,” says Pass. “With automation, we can manage our day-to-day business with peace of mind knowing we are providing safe and consistent feed to our customers.”
The past & the future
When Pilgrim’s was founded in 1946, it was with the spirit of innovation at its heart. That mindset continues 70 years later as the company continues to expand and innovate within the poultry industry. Its new facility in Ranger, GA, is another step in a long tradition of providing its farmers and consumers with the best products possible. ■