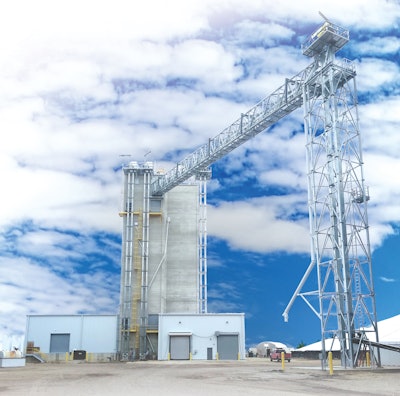
Founded in 1916 as Chickasaw County Equity Cooperative Association, Five Star Cooperative has grown to have more than 2,000 members and locations throughout Iowa. The cooperative has been able to thrive by offering its members what they need in the ever-changing agriculture industry. To do that, it continuously evaluates what its members need or will need in the future. With a client base primarily made of large swine producers, Five Stars’ New Hampton, IA, feed mill was no longer able to keep up with demand.
“Five Star has an existing feed mill in New Hampton that was built back in the ‘60s,” says Jeff Hageman, assistant feed department manager, Swine Business Development Coordinator and HACCP Coordinator for Five Star Co-op. “The old mill’s design simply could not keep up with the volume of feed we need today. We’ve even remodeled the mill a couple of times to bring it up to date, but 600 to 700 tons/hour is the capacity limit of the old mill running 24 hours a day.”
The mill created a bottleneck that Five Star decided to address, but there was still debate about how to handle it.
“We didn’t have room to expand the facility we had, so we had to build new,” explains Hageman. “We had two options, to build on the site we already owned or to do a green space build. The green space option became expensive as we priced out options, and we had assets we could utilize at our current site. We would have liked to go into a green space, but it financially just didn’t work.”
Five Star chose to build its new feed mill at its current New Hampton site. The location housed the older feed mill being replaced and had other assets that Five Star would be able to use with the new mill.
Fitting into place
Once Five Star determined what it wanted to move forward with, it turned to Empire AG LLC as its general contractor.
“Empire has been a fantastic group to work with,” explains Hageman. “If they thought they could do a better design than what we had, they were very upfront in telling us how things work to our advantage. If we had any issues, they were very receptive to what we were saying. We would work with them again in a heartbeat.”
Together, Empire Ag and Five Star built a unique feed mill perfectly suited to the location.
Harnessing assets
Five Star Cooperative’s New Hampton location was home to a grain elevator, agronomy center, retail center, fueling center, the cooperative’s head office and other services. While this makes the location a busy site, it offered the new feed mill plenty of advantages, none more important than having a nearby grain elevator.
The bulk grain used at the mill is brought to the elevator by cooperative members, where it gets tested, graded and sent to one of six bins. One of those bins has a drag conveyor from InterSystems that delivers grain across the site to the new mill. This arrangement requires cooperation between the grain and feed departments.
“The grain department controls the grain that we receive,” says Hageman. “We tell them what we have for guidelines and what we expect out of the corn that’s coming to our direction, but they are in charge of getting it to us. We want good quality, non-damaged dry corn because this is going back to a producer paying good money for this. We want to send them the best product we possibly can.”
Unique design, familiar process
Grain moves from the grain elevator through a conveying system with parts from InterSystems, Schlagel and Mitchell Mill Systems and into a 5,000-bushel holding bin at the top of the feed mill. That holding bin feeds two roller mills, one from Lone Star Enterprises and another brought in from the old mill.
“We have two roller mills because we have two different sized grinds,” explains Hageman. “A fine grind at the 525- to 575-micron range and a courser grind in the 800 to 850 range. Many of our customers want a courser grind for bigger pigs and sows.”
After the corn is ground, it moves into a five-ton bin above a five-ton high-speed twin shaft mixer from Scott Equipment Co. A second five-ton bin also sits above the mixer with the feed formulation’s micro-ingredients inside. The micro-ingredients arrive at this bin through an Easy Automation system that gathers the required ingredients from two Easy Automation 16-bin micro-ingredient systems and Easy Automation four and six tote bulk bag systems.
“We have the capability to produce anywhere from 1,200 to 1,400 tons a day, possibly more depending on order sizes” says Hageman. “Double what we were producing in our old mill.”
After being mixed, the feed moves into one of 16 finished feed bins, each capable of holding 32 tons of finished feed.
A loadout system, comprised of parts from Cleveland Vibrator, Tom-Cin Metals and C & A Scale Services, loads the finished feed into one of Five Star’s 10 trucks. Hageman expects the mill to be mixing feed 20 hours/day if there is high enough demand, with trucks loading finished feed 24 hours/day.
One-person operation
A new mill running on a 24/7 schedule would generally require an increase in staff. Due to the automation system from Easy Automation and through cross-training staff, Five Star Cooperative’s New Hampton mill is able to operate with a staff of one.
“The new mill’s design allows one person to operate it,” says Hageman. “We’re hoping that one person will be able to mix and keep the minor micro-ingredients bags loaded by themselves. Then we’ll bring in a second person from somewhere else at the location to help unload trucks and with maintenance items.”
Running the mill with such a small staff is possible because of the way Five Star has empowered its truck drivers to load trucks themselves.
“There is a camera system in the mill that allows a driver to take an iPad in his truck and operate the loadout system,” says Hageman. “He’ll be able to load the truck himself, watching a visual camera through his iPad for opening and closing his gate and will be able to move that truck by himself. At the old feed mill, we needed a driver and someone loading with manual cables.”
The camera system also makes the feed mill’s need to pull staff from other buildings on the site more manageable.
“We hope to have the camera system set up on other computers at the site,” says Hageman. “If a truck comes in, other employees can see it and help unload.
“The mill worker can keep mixing the feed with others helping out with different tasks, so we don’t slow that process down,” he continues. “We’re hoping once we get up and going that we can mix enough feed in 10 to 12 hours a day to do what our current business is, with room for expansion.”
The ability to adapt and develop innovative ways to use existing assets sets Five Star Cooperative up for success at its new mill. With it in their arsenal, Five Star Cooperative will continue its 104 year long mission to serve its members’ needs. ■