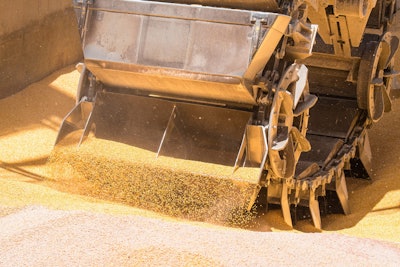
Covering 70% of the Earth’s surface, the ocean is the largest transit highway for millions of tons of commodities chartered and loaded every day for destinations around the world. Ships moved more than 41 percent of the value (nearly $1.8 trillion) and more than 70% of the weight (1.6 billion tons) of international freight into and out of the United States in 2018, according the U.S. Department of Transportation’s Bureau of Transportation Statistics.
Oceanic freight is a reliable and economical long-distance transportation option for U.S. coarse grains and co-products going to to growing world markets. Because of decades of investment into this system, ocean ports across the United States have maintained trade flow even as COVID-19 concerns spread earlier this year.
“Vessels are still moving, and they are still loading unimpeded,” said Jay O’Neil, an international commodity consultant. “We are here to work 52 weeks out of the year and supply what is needed to the world.”
From the Field to the Shore
U.S. grain arrives at export ports primarily by rail or barge. Railcars bring grain directly into an export facility, whereas grain arriving by barge may be placed in a fleet of barges awaiting an order to move into the export elevator. Once that order comes, a port tugboat heads out to the staging area to move the barge into the export facility for loading.
These grain transport and export facilities are privately owned and operated. However, the U.S. government is involved in grain inspection services through the U.S. Department of Agriculture’s Federal Grain Inspection Service (USDA’s FGIS) or vessel inspection by the National Cargo Bureau (NCB).
FGIS inspectors, or their designated agencies, take samples for quality testing at each stop in a kernel’s journey from the farm to the port. FGIS conducted more than 3.3 million export grain inspections in 2018, according to the agency’s annual report to the U.S. Congress.
“Every time we touch grain, we analyze it for quality,” O’Neil said. “When grain is brought in by the farmer to the local grain elevator, they take a sample and test it. When that grain is loaded out into a rail car or barge, it is tested and analyzed for quality. Once that grain arrives in port, it is tested upon arrival and then again when we load a vessel out. We’re testing, we’re taking samples, we’re analyzing grain quality at every step of the process.”
When grain arrives at an export facility, it does not stay long. Export facilities are not designed to be long-term warehouses for grain. Instead, they operate as put-through facilities, dependent on receiving grain and loading it out onto vessels within a week or even days.
Safeguards for Vessel and Cargo
Before grain can be loaded, however, its oceanic transport must arrive. Coming into port in the United States is more complex than pulling up a fishing boat to the dock at the local waterhole.
There are different geographic areas of control before a vessel can physically anchor or dock in a port. These control points can include transiting across the bar (where the river dissipates into the ocean) and various river districts, eahc of which is under the jurisdiction of different pilot associations. For safety reasons, these local pilots board incoming and outbound ships and assume navigational command of vessels as they move up or down various stretches of a river system or through a port district on their way to their assigned anchorage.
Upon arrival in port, grain vessels must undergo a cargo hold inspection by the NCB. When the vessel goes to anchorage, an NCB inspector goes to the ship to inspect it for cleanliness and declare whether or not the vessel is “ready in all respects” to receive cargo. The inspector will physically climb through the cargo holds to inspect them, looking to ensure there is no moisture, no chipped paint, no residue from a previous cargo or anything else that might be hazardous. If any infractions are found, the inspector will fail the vessel and require cleaning.
If the cargo holds are clean, dry and ready for cargo, the inspector will issue a NCB vessel pass certificate. That certificate is required for a vessel to file its notice of readiness (NOR) with the loading facility. The vessel agent then can take this pass, along with crew health and other necessary documents, to the export facility. If all is in order, a vessel can make a berth application and be accepted into the facility vessel line-up for loading in normal rotation, meaning it must wait its turn to be loaded with grain, then be on its way to its next destination.
“These safeguards - the inspections and checks and double-checks - are mandated by the U.S. government,” O’Neil said. “Whether that is FGIS on weight and grade or NCB on vessel inspection, these are independent, third-party verifications and certifications at every step of the way. That should reassure buyers of the safety and validity of those documents and the care that is being taken when we load vessels.”
Backed by government agencies charged with maintaining quality and cleanliness and systems built over centuries of trade, buyers around the world can be assured U.S. coarse grains, co-products and ethanol remain available and able to meet their needs - day in and day out.
How Oceanic Freight Reacted to COVID-19
These systems governing how U.S. coarse grains and co-products are delivered to the world’s market via oceanic freight have been honed over centuries of trading. Even with strong contracts and practices in place, both buyers and sellers had significant apprehension about how grain shipments might be affected by the COVID-19 pandemic in the first quarter of 2020.
The grain trade, however, has operated without significant disruption while working to address newly emerging issues. For example, vessels have had trouble with exchanging crews due to ports around the world refusing to allow crew members to disembark and transit to their foreign homes. As a result, some crews have remained on their vessels far past their normal window to exchange with fresh crew members, even as the grain vessels keep operating.
On a more positive note, there has been an increase in the use of electronic documents and electronic signatures. Historically, the documents related to grain transit have been delivered physically by a person or the ship’s captain. Following the institution of COVID-19-related measures, many elevators made accommodations to maintain social distancing, either by limiting direct contact with ship personnel or by providing electronic bills of lading, electronic signatures and even obtaining electronic phytosanitary certificates.
Because electronic documents are more efficient, more world markets are likely to adopt their use over time. But, O’Neil cautions buyers to watch during this time of transition that customs officials will accept these electronic documents upon arrival at destination.
O’Neil has a final word of caution on how COVID-19 will affect international grain contracts themselves. In the history of modern grain shipments, no pandemic has required the same level of attention and modification as COVID-19. Neither the North American Export Grain Association (NAEGA) or the Grain and Feed Trade Association (GAFTA) contract -- the two most widely used international grain trading contracts – directly address a pandemic, because they have not had to do so before. So, buyers, sellers and contract arbitrators like O’Neil are still discussing how COVID-19 or future pandemics could contractually impact a buyer’s or seller’s performance.
“COVID-19 is new and unique, so all need to be watching and reading their contracts carefully,” O’Neil said.
Despite these challenges, the flow of U.S. grain itself has stayed the course. Backed by government agencies charged with maintaining quality and cleanliness and systems built over centuries of trade, buyers around the world can be assured U.S. coarse grains, co-products and ethanol remain available and able to meet their needs -- day in and day out.
Learn more about how grain trade has continued throughout COVID-19.