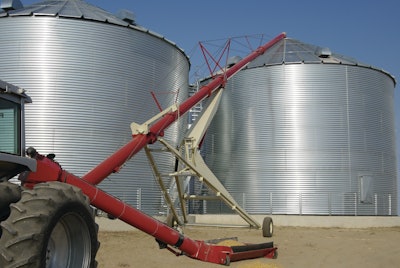
A great person once said, “If you help others get what they need, you’ll get what you want.”
This concept is true across many industries, but it’s especially true in the grain business. Those who can truly provide a value to their customers will be rewarded. Grain companies are aware of this and work tirelessly to provide a place for their farmers to dump their grain at a competitive price, work 24-hour-days during harvest, provide logistic support and transportation when they can, create good policies for their farmers to market their grain, provide forward contracting opportunities and much more when it comes to friendly customer service and speedy payments. That value is tremendous and necessary to make our grain industry efficient and prosperous for all involved.
And we have seen some prosperous times in the grain business over the last decade or so. As I drive through the country, I constantly see shiny new bins built by both commercial grain businesses and by farming operations. Growth and opportunity abound!
Unfortunately, this is where some folks in the commercial grain business begin to feel threatened and get nervous over the growth of farming operations. But why?
From the outside, it seems logical. If you’re in the business of putting a farmer’s grain in your bins, then farmers building their own grain bins would seem to be an obvious threat to your business.
Providing value
I can tell you this from experience, whether you think farm storage is or isn’t a threat, you’re right. I’ve seen grain managers with declining bushels shrug their shoulders and use on-farm storage as an excuse to explain away their businesses issues, while the yields and usage in their area soar. I’ve also seen grain managers out working hard on their relationships and growing their businesses exponentially without running any more physical grain through their facilities.
It comes back to our original point: can you provide value and help a farmer with grain bins get what he needs? As a basis trading grain business, of course, you can. It may not be through the traditional way of taking harvest pressure off him, working long hours and having the fastest grain leg in the county, but in giving him access to the best markets, providing logistical flexibility, marketing flexibility and much more.
Think about it, do you know how to best make money off grain bins? It’s what you do! You have knowledge and expertise that your farmers don’t have. That’s not an oversight on their part, they know how to make money farming and are good at it. That’s the focus of their business and it should be because where they truly make their money.
So how can you go about providing value to farmers with on-farm storage? The first way is to help them understand where the value is in their grain storage and how to capture it for their farming operation.
To a producer with new farm bins (and their banker), the new storage should give them added return, but how do they go about figuring exactly what that is? That’s a loaded question, and there’s not a precise formula, but there are plenty of misconceptions about what goes into that answer, so let’s separate fact from fiction regarding common thoughts on the use of farm bins that you can communicate to your coustomers.
Logistical Efficiency: Fact
When harvest conditions are upon us, it’s go time. Twenty minutes to town, an hour in line (or worse), and 20 minutes back to the field is a grind and it’s maddening when there’s rain in the forecast. Most won’t have the space to hold their entire crop, so the added time of going to a commercial grain handler won’t be completely avoided, but every little bit helps. Farm storage can save time and can save the farmer from weather that can diminish the quality of their crop.
More Time to Sell: Fiction
First of all, is more time really needed anyway? A good commercial grain company will have a market ready to buy farmer grain for one-two years before harvest. Besides that, if you still need time after harvest to sell your grain, there are plenty of options available to farmers: storage, price later, basis contracts, minimum price contracts, etc. All of which can be done without having your own grain bin.
Picking Up Market Carry: Fact
This can be done, but must be done in a decisive, intentional way in order to avoid falling under the previous category of waiting to sell grain. There are two ways to do this. First is for a farmer to hedge their bushels, lock in carry spreads and lift the hedges when they make the cash sale. Of course, this requires trading a futures account. Many producers do not have futures accounts due to fear of margin calls or other risks, but there is another way to capture carry without having a futures account.
The second way is for the farmer to make their harvest sale for a deferred delivery slot. Let’s say it’s harvest and the local elevator is paying $3.50 for spot bushels. Rather than selling for $3.50, they can still sell to the elevator that day, but for Jan/Feb/March delivery at a higher price. This higher cash price comes from a carry in Dec/March futures as well as a higher basis in non-harvest time. So, instead of selling $3.50 corn at harvest, the producer sells $3.75 corn to be delivered Jan/Feb/March. Keep in mind, this is not a delay of marketing the grain, but rather in the delivery of it.
Avoiding Storage Costs: Fiction
This seems a bit counterintuitive, I know, but follow me for a bit. Yes, if they’re waiting to price post-harvest and it’s in commercial space, they are paying a fee whereas they wouldn’t be if it was in their own space. However, those storage fees are partially something they are paying to transfer risk (quality and shrink) to the elevator. If they are keeping the grain themselves, they are assuming that risk. No matter how good a farmer is at taking care of their bins, this is a real risk. Even the greatest grain handlers/operations experts have had their issues at some point. A commercial elevator has the advantage of spreading the risk out among many bushels of varying quality and a full-time staff of professionals keeping tabs on everything. Just 1% shrink on $10 soybeans is 10 cents. In exchange for not paying someone a fee, they are taking that risk or more.
On-farm grain storage can obviously be very beneficial to a farming operation. However, it has the ability to hurt the overall farm marketing program if not managed correctly. Teaming up with a merchandiser at a local grain elevator to understand the many marketing and delivery options is always a good idea. You can help your customer extract as much from the market as possible and provide a lot of flexibility. That’s a big-time value and a need that you can continue to fill for your customers even if they are building more of their own bins and don’t need as many of your services at harvest time. ❚