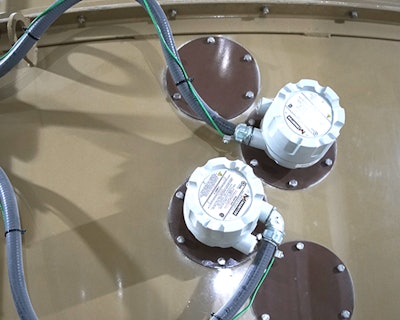
Grain handling facilities have long relied on sensors for hazard monitoring and explosion prevention. Meanwhile, in feed production, sensor adoption has lagged. That’s changing, however, as interest and investment in sensor applications and technologies has grown rapidly in recent years.
Though sensor technologies have come a long way, initially, feed mill operators struggled with sometimes erratic, unreliable older ultrasonic laser and radar products, e.g., noncontact sensors that were affected by dust suspended in the air or wide-beam angles that would intersect with the walls of the ingredient or loadout bins, reports Nathan Grube, BinMaster regional vice president of sales for the central U.S.
“Feed mills that have invested in continuous measurement devices in silos want to be assured that what we’re providing is going to work. They want it to be accurate, repeatable, stable and dependable,” he explains.
Today, not only have feed mill sensors been optimized to overcome these obstacles, but they have also been proven to add additional gains to feed mill production, efficiency, operations and maintenance.
Feed mill sensor applications
In feed manufacturing facilities, sensors are used as measurement devices and level indicators in ingredient bins and liquid tanks, and in finished feed and loadout bins. They are also used for speed, hazard and maintenance monitoring for open belt conveyers, bucket elevators and enclosed belt conveyors, i.e., screw and drag conveyors.
Sensors provide real-time feedback, collecting and displaying data to provide an instantaneous operational benefit.
“With sensors monitoring bearing temperatures and belt alignment, performance issues can be caught early, preventing longer downtimes, additional maintenance and repairs, and loss of productivity,” says Anthony Leali, the business development manager for electronic products at 4B Components Ltd.
Sensors provide performance information to enhance preventative maintenance programs, ensuring facilities run efficiently, with fewer repairs and prolonging the life of the equipment. Leali notes small- to medium-sized mills without multiple feedlines especially benefit from this reporting.
“Very often it takes an incident — whether it’s catastrophic or even a small fire, explosion or safety issue — to make operators realize that they really do need something,” he says.
Automated control systems and facility upgrades further promote the integration of sensors into feed production for safety and to ensure proper equipment operation.
“Sensors ensure the safety of the personnel, the facility and the product,” Leali says. “Sensors provide so much information to really help keep things running smoothly and prevent problems. Once [feed mills] have them and see what it can do, it’s like, ‘How did we do this before?’”
Emphasis on automation
Feed mill automation control suppliers, e.g., WEM Automation, Repete, Easy Automation and CPM’s Beta Raven, have integrated sensors into their programmable logic control (PLC) systems, giving operators a single unified view of the entire operation and the opportunity to react appropriately when issues occur.
“The batching systems control everything that’s going on in the mill,” Grube says. “The trend definitely is to take our signals — whether it’s a Modbus [RTU] or analog 4-20 mA signal — and drive them into the mill’s PLC system to integrate them with the whole facility and everything going on in it.”
As the next generation of feed mill engineers, operators and managers enter the workforce, many may bring their education from the universities with programs specializing in feed manufacturing. With this comes a certain level of expertise — and expectations.
“They want everything to be automated,” Grube says. “It’s hard to find people and it’s a time-consuming process. If you have 40 to 60 vessels that need an inventory — that can be two or three hours of labor everyday — and feed mills can’t find anybody there to do that.
“The old-school way isn’t what they want to do,” he adds. “They want their mill to be efficient, they want it to be safe and, you know, they’re running with fewer people all the time.”
With shortages in qualified applicants and small labor pools, sensors — and automation overall — relieve the pressure to fill positions. ■
Announcing the Feed Mill of the Future Digital Supplement
In January 2022, WATT’s feed brand’s Feed Strategy and Feed & Grain magazines joined forces to launch the monthly Feed Mill of the Future digital supplement.
Each edition aims to provide animal feed industry stakeholders with forward-looking content, market insights and a spotlight on the leading-edge technologies shaping the global feed industry of tomorrow.