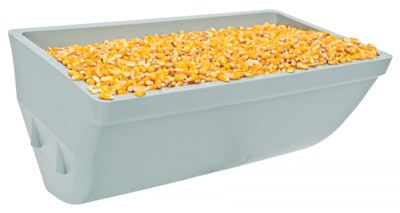
Punching ventilation holes in the bottom of elevator buckets makes the filling and discharge of materials more efficient. This is especially true for fluffy inputs or fine powders such as flour, cement, dusts and shavings.
As material enters the elevator bucket, it encounters a pillow of air trapped in the bottom of the bucket. Ventilation holes in the bottom of the bucket allow this air to escape and be replaced by the entering material.
Preventing a Vacuum
As the material exits, a vacuum can form in the bottom of the bucket which prevents full material discharge. Ventilation holes prevent this vacuum from forming and allow air to return into the bucket. Without ventilation holes, the material is stuck in the bucket as it moves over the head pulley, often discharging too late and falling down the inside of the elevator leg “down” casing.
A mild ventilation pattern, however, such as a Vent # 1, is still a good idea.
Fluffy and light materials like alfalfa or DDGs are sensitive to turbulence. Reducing turbulence within the leg casing system improves discharge out of the bucket and the transit through the head section to the spout entrance.
Air currents generated by excess turbulence can alter the material discharge from the elevator bucket and drag it back down the “down” leg.
Aggressive Ventilation
In this case, any material lost through the holes simply falls into the bucket beneath, and so on, and so on. Although an individual bucket may lose a small amount of material, in terms of the complete elevator leg system, there is no net loss.
Information provided by Carl Swisher, sales manager, elevator buckets with 4B Components Ltd. For more information, visit go4b.com.