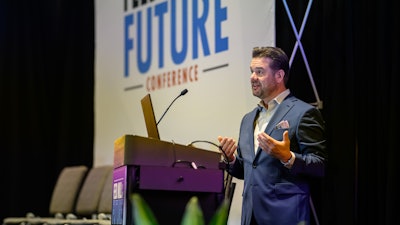
Feed mill automation is on the brink of a major breakthrough, according to Matthew Boland, sales territory manager for CPM Automation.
Drawing on more than two decades of experience in automation, including software development through direct hands-on integration, Boland presented his predictions for the future of artificial intelligence (AI) at the Feed Mill of the Future Conference at the 2025 International Production & Processing Expo (IPPE) in Atlanta.
Boland said that while AI is still in its infancy in feed mill automation, its rapid development may transform the industry sooner than ever thought possible, and preparation is vital.
“This is a good time to start talking about AI and automation because we can start to get ready now for the implementation of these AI systems in our automation,” Boland said.
Lessons from the history of automation
AI’s development pace can’t be compared with any other technology in the feed industry, he said. To make his point, Boland retraced the history of modern-day feed mill automation, which hasn’t transformed significantly in decades.
In 1968, a General Motors challenge led to Richard E. Morley’s invention of the first programmable logic controller (PLC). The next leap forward came in the 1990s with the adoption of Ethernet as the standard protocol, breaking down proprietary communication barriers and enabling seamless data sharing between plant floors and offices.
Ethernet adoption not only simplified operations, but also laid the groundwork for present-day data environments. With big data, a new challenge emerged: effective analysis of data — one AI will soon address.
Task-based to goal-based systems
Boland said current automation systems, which still predominantly use PLCs to control feed mills, operate on “task-based” models. Using the analogy of a human body, he explained how PLCs function as the brain, receiving input from sensors (like humans' five senses) and executing precisely programmed instructions.
Boland projected that in the future, feed mills will move toward AI-powered, “goal-based” control systems. Such models increase the system’s flexibility, with AI empowered to respond to inefficient equipment and processing anomalies without human intervention.
“The system essentially watches itself as it works,” Boland said. “It closes its own loop. Over time, accumulated data is utilized by the system to improve its own process, using an algorithm and inputs. It does its job, monitors how well it does its job based on the output, and then changes its parameters to do the job better. We are working to get there next.”
Considerations and challenges for feed mills
The outlook is bright for feed mill automation transformation, but the transition to goal-based control systems requires careful preparation. Boland highlighted four key considerations:
1. Infrastructure readiness: Server, operating systems (OS) and network architectures must be upgraded. AI platforms demand robust, smart networks with real-time communication capabilities for data.
“If you’re not providing the right sensors, an adequate amount of sensors, or placing them incorrectly, your AI system will not have the appropriate data to make the decisions it needs to improve your processes. I cannot stress enough the importance of sensors in AI and data acquisition.” — Matthew Boland, sales territory manager, CPM Automation
2. Sensor optimization: Strategically located high-fidelity sensors are key, as these provide the AI system’s only window into the physical world.
3. Data acquisition: Having full-fledged structures for collecting data, such as historians or complex databases, will enhance AI’s analytical powers.
4. Equipment compatibility: Using updated equipment that can integrate with new AI technology is key — older machinery could potentially become a bottleneck in the process.
Transition at the plant level comes with significant challenges, too, Boland said. Cost remains a major factor, particularly for facilities requiring extensive updates to their existing infrastructure.
Training requirements and, likely, outside expertise are also needed for data modeling. Boland said “no-code” AI products (that don’t require training in the field) exist, but these are designed for very specific applications.
Security concerns, especially regarding AI containment, presents ongoing challenges that the industry is still working to address.
“Obviously, containment is one of the biggest topics in AI right now,” Boland said. “How do we provide air gaps, so it doesn’t proliferate where we don’t want it to?”
Despite these challenges, Boland emphasized that with strategic planning, the right investments, and a focus on data integrity, the feed milling industry can successfully harness AI to drive efficiency and long-term growth.
Near-term AI capabilities
While many feed companies are just beginning to consider implementing AI-powered automation, there are examples of AI in feed milling today, Boland said.
Current software excels at monitoring critical assets, particularly motors and equipment like pellet mills, detecting subtle variations that might indicate pending failures. Integration with ERP and business systems is also becoming more common, Boland said, while AI’s ability to suggest process improvements and preventive maintenance is proving valuable.
Boland concluded by urging attendees to view AI as a powerful tool for collaboration and efficiency, rather than a replacement for human expertise. Like any tool, its impact depends on how it’s applied. While AI cannot perform physical tasks — like changing a pellet mill die — its ability to optimize processes and predict maintenance needs will transform feed mill operations in ways we’re only beginning to understand.
Facilities that begin preparing now — updating infrastructure, modernizing networks and implementing proper data collection systems — will be better positioned to adopt this technology cost-effectively and reap its benefits sooner.
“AI is growing very, very fast — at a rate that we haven’t seen in many industries before, so it’s an interesting time,” Boland said.