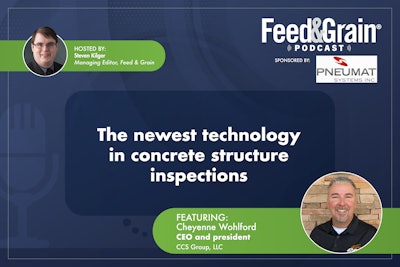
In this episode of the Feed & Grain Podcast, Cheyenne Wohlford, CEO and president of CCS Group, LLC stopped by to talk with host Steven Kilger about effectively handling human resources as a small company. They talk about concrete structure inspection, how often it should be done, what an inspection covers, technology like drones and radar scans, plus all the data that can be gathered during a visit.
Podcast sponsored by Pneumat Systems.
Transcript has been edited for clarity
Steven Kilger - 00:00
Hi everyone, my name is Steven Kilger and I'm the managing editor of Feed & Grain and the host of the Feed & Grain podcast. Thank you so much for joining me today as we dive deep into the issues affecting the feed manufacturing, grain handling, and allied industries.
Today’s episode is brought to you by The BinWhip from Pneumat Systems. The powerful Dual Impact BinWhip removes the toughest buildup and blockages in industrial storage silos – without hazardous silo entry. Learn more today at binwhip.com
In today's episode, my guest, Cheyenne Wohlford, CEO and president of CCS Group.
We talk about concrete inspections, when the concrete structures on your facility should be inspected, what to expect during the inspection process, what kind of information is gathered, and some of the newest technology that's being used in the field today.
I hope you enjoy the interview. If you want to help out the podcast and are listening to this in a podcasting app, please rate us and subscribe. If you're listening online, sign up for the Feed & Grain newsletter industry watch to see the latest podcasts and stay up to date with all the latest news from around the industry. Now, onto the show.
Hi Cheyenne, thank you so much for talking to me today. For any listeners out there who don't know you, can you tell us a little bit more about yourself and your relationship with the industry?
Cheyenne Wohlford - 01:10
Yeah, absolutely. So again, my name is Cheyenne Wohlford, I'm the president and CEO of CCS Group. I started CCS Group in 2009 and I guess my main objective at that point in life was to Start a construction company that utilizes the newest technology, the newest safety standards, and all that type of aspect and approach.
We provide silo repairs nationwide and so we're serving clients throughout the U.S. I've done some international work as well, but I say our primary focus is in the United States. Country elevators, terminals, loadout facilities and such, feed mills, ethanol plants. We also dabble in the bulk storage of coal and cement, so we're also in other industries as well, but I would say 99% of our business comes from the feed and grain industry.
Kilger - 02:04
Yeah, and you guys are very involved in the grain and feed industry. I mean, every year I see you at GEAPS and you're always involved in something. You're always moving and shaking.
Wohlford - 02:14
Absolutely. I think that's kind of the spirit of what we designed CCS around was always looking for the newest technologies, not so much The newest gimmicks or anything of that nature. Everything we bring to market is studied very heavily and critiqued and want to make sure there's a tried and true process either with equipment or materials, new repair materials, or new technology in that aspect.
So definitely keeps us busy and as an entrepreneur inside of me that's what gets me excited about getting up in the morning is seeing what's new out there and how we can utilize that in our industry which we very much enjoy. It's a great group of people.
Kilger - 02:52
Yeah, definitely. And so what I have you here for is to talk a little bit about inspecting your facilities for damage so you could get ahead of it before you have some serious happen, right? Can you tell me a little bit about how often feed facilities, and grain elevators should be like inspecting their property, not just, you know, glancing at it as you go by, but taking a walk around and looking?
Wohlford - 03:16
Yeah, we get that question a lot. And I always tell our clients are potential clients. I guess the main thing I kind of refer to it as a health checkup if you will. You know, once you get that initial once-over inspection done, which is where we go into the intense GPR scanning, drone inspections, sound testing. Kind of consider that like you're going to the doctor once a year and you're getting your physical done you're getting blood work done and that's once we get that done and we kind of know what the structure is as a design or necessarily as a build, I guess then you can kind of move into a secondary phase of doing just visual inspections going back to that kind of what you said earlier a little less intense not you don't have to do GPR scans every year primarily because the rebar is the rebar nothing's going to change in that aspect. So I always tell them, let's get the first initial cumbersome blood work done.
Wohlford - 04:10
Let's do all the GPR scanning. Let's see what your roof beams look like internally inside your bins. Let's inspect your hoppers. Let's get your tunnels and do the once over. And that's, that's a pretty heavy, intense inspection. From there, then you can move to every year or every year type of aspect or every other year, excuse me. And during that initial inspection process.
Wohlford - 04:32
You might uncover some areas that either the facility manager or the outside superintendent or something didn't notice. So, once you get that first initial one done, then you can kind of direct them to monitor different areas, either throughout the year or when you come back to do the secondary visit, say a year down the road. So again, the first initial one is the more intense, there's a financial burden with that, you're going to pay to have somebody come in and give it a once-over. But what I like about that, Steven, is that information then can be shared with third-party engineering, you can send that out for review and get everybody kind of on the same page, I guess.
Kilger - 05:09
Yeah, and while there might be a financial component, you know, it's a lot better than having a bin collapse or something like that. That's the big, big issue.
Wohlford - 05:17
I always explain that the preventative maintenance side of things is a fraction of the cost when it comes to ruptures or silo collapse. Of course, you've got The safety aspect of it first and foremost is to make sure that you got a healthy facility so that you have healthy employees and safe employees that comfortable coming to work every day and the morale and yeah it's the preventative side is really where we like to spend our time.
Kilger - 05:43
Yeah, well, just like humans, right? Going to the doctor is a pain, but it's a lot better if you catch things early than have to get surgery later. So how does the inspection process work, especially for that first kind of inspection, the one where you do a really thorough overview? What should people expect when they call you and they have someone come out to the site?
Wohlford - 06:03
Yeah, so the initial meeting is we do a lot of data collection upfront. We try to get our hands on the blueprints or the as-builts. We know what the structure should be and we try to visit with them and answer any questions that they might have up front as far as what the process looks like. Do the bins need to be empty? Do they need to be full? Can we be receiving grain? Can we be shipping grain?
Wohlford - 06:26
Just try to get on the same page of what is your operations doing that particular day. How can we be as less intrusive as possible? If we, you know, need to have a boom lift set up and do GPR scanning and stuff, then we'll have to have some sort of traffic control or something. But again, just kind of getting into the nuts and bolts of what are you seeing as a client. Show us the areas that you're concerned about and just do a good walkthrough with them of what they have going on, and what the history of the facility is. Finding out what the facility was built for, whether was it just a storage facility, and now all of a sudden we are using it as a kind of centralized loadout type of situation for that client. So just a lot of fact-gathering meetings I guess upfront if you will, phone calls, Meetings with the operations team, the marketing team.
Wohlford - 07:11
And then the second phase of that is now what do you want to use the facility for in the future? So as we start the inspection process, we kind of have that in the back of our heads of saying, okay, they're going to add a larger leg, or they're going to put a discharge in somewhere, or they're going to try to increase their rail load outsize or whatever. So just then getting a futuristic view of, What are your intentions for the use down the road? And so that kind of is the kickoff meeting that just allows us to kind of get an understanding of what you have and where you want to go.
And then from there, you know, we just start the process, kind of try to stay out of sight, out of mind. We move into a majority of the time doing GPR scanning.
So that's ground penetrating radar, where we're doing scans from top to bottom, utilizing a boom with scanning and checking for every Horizontal piece of rebar that's in that facility.
Wohlford - 07:58
And then that typically moves into the drone inspections. And from there, you know, the drone inspections are always kind of fun because you start with a plan, and typically doesn't end the exact way you planned it. It's like, Oh, so since you can see this so well, then. I think we should drop the drone into a different silo over here. Can you answer this question for me? And so oftentimes we go in with a very detailed plan of which silos we're inspecting, what areas we're looking for. And I would say oftentimes it ends up going in a, not in a different direction, but an additional direction of saying, okay, I didn't realize you guys could capture those photos or the videos so well, or that we're getting an actual LIDAR map.
Wohlford - 08:38
I had no idea that you could get these pictures. Would you mind dropping the silo into bin number 10? Because we have a lot of water leaking into that bend, can you tell us where it's coming from? And it just so happened on a rainy day that we could drop down and see right where that water was coming from because it was cleaning the dust off the interior wall of the silo where that water was entering the bend.
So again, those kinds of those additional moments where you kind of go into it with a plan, but then they're like, oh, by the way, since you're here and we were able to launch our external drone and get him the picture that he needed then to start drawing his plans out and such. It's always kind of fun to do those additional services and make people's day and hopefully make that project a little bit easier for them. So that's kind of the typical day in the life of the inspection process.
Wohlford - 09:44
And then obviously wrap that up at the end of the day by sharing the information that we found. Oftentimes we'll pull up the videos right there with the client and show them what we looked at, what we found. And if we didn't quite get the picture we wanted or the video that wasn't clear and we need to go back, then that's the great part it's such an easy entry that all you have to do is go back up to the roof or go in through the side of the silo and relaunch the drone and get exactly what the client's looking for or what we're needing for our inspection process. So it's kind of neat there too to review your information right off the bat and be able to go back in and get a better video or better footage of something that might've been suspect.
Kilger - 10:23
Yeah, and that's one of the things that when I saw you've been putting out some really good marketing you guys do great marketing too by the way just you know tell your marketing team they do a good job but you've been putting out this marketing from about you know using drones for these inspections which when you see it you're like yeah obviously that's a genius idea because it's got to be able to see things in ways that just no one else can do from a ground perspective. Can you talk a little bit about the advantages of using these drones for these inspections?
Wohlford - 11:04
Putting a tripod in a Bozeman's chair and a winch system and dropping me down inside of the bend. So I knew there had to have been a better way to complete that inspection. I always wasn't satisfied with either the picture quality or the placement of where I was at within the bend. So there's a lot of information that kind of, I guess, just got left on the table when we used to do the old way of dropping somebody down inside of the bend. And of course, then you have the safety issues. You're in the bin, you're in a confined space, you've got a fall protection rescue plan. There are usually multiple, multiple people involved with that, including the local fire and rescue in the event of an accident.
Wohlford - 11:40
So it takes quite a team to drop somebody down safely and to do it the right way. And so as I started to see this technology come down the pipeline, it got me excited because that just meant I didn't have to be lowered inside of the bins anymore. And again, it's such an encompassing Process that once you got out of the bin and got home and realized that you didn't get the exact angle that you wanted to the picture or it was dusty and camera that you had, you know, wasn't able to capture exactly what you're seeing with your eyes intrigued me when I saw this drone technology. So, a couple of things to note is it allows us to do it much quicker. We can, you know, obviously the, about the time that it takes to pull a manhole cover off. And drop down inside of a bandit is anywhere from 10 to 15 minutes per inspection.
Wohlford - 12:27
So that's kind of nice if it eliminated that from being a two-hour process to about a 10 to 15-minute process. I touched base on it a little bit earlier, but the safety side of it is huge. No more human entry. And as we know in our industries, that's kind of our goal is zero human entry. That's where we're going with all the different loading systems and hoppers and augers and such as we don't want to have anybody in those bins if possible. So that's been a nice addition for us as well. Other nodes would be the whole time the drone is deployed and in the bin, you're capturing 4k video.
Wohlford - 13:00
So oftentimes we get home and we're reviewing those videos in high definition on a flat-screen TV and we see more than what we saw on a little 12-inch tablet while we were flying the bin in person. It's kind of neat to get back and review that video with those 4k and high-definition videos and see the different things that you didn't see even when you were on site. And then of course, while you're doing that, you're able to catch what we call POIs, which are points of interest. So if we are on the bend deck and we're flying around and we see a major horizontal cold joint or a roof beam or a truss that isn't positioned right or potentially failing, not only can we take 4k videos of that, but we also can take some still photos of that so that those photos can be shared. Very easily and again high resolution so they can be blown up and studied so that's another nice objective that is the POIs as you're flying throughout the bend.
And then last probably but not least is the entire time that we're using our lidar drone That drone is collecting a point cloud which is millions of data points or thousands of data points and so as you're creating a 3D map of that interior silo as you're flying around in there. And so that's neat when you come back out either when you're studying a silo that has a potential roof failure or beams that are misplaced, things of that nature, anomalies if you will, you're able to go back and get exact precision measurements of the beams and that's where that tool has become handy for us is sharing that information with engineering.
Wohlford - 14:34
We're looking at going back and adding additional roof trusses or different supports or something and they want to know what the measurements are on the roof beams or how far apart they are or how long it is. That's neat as well. And that LiDAR map did something a few weeks ago for us that we didn't even realize possible, but we were asked to come to inspect a bin that had fire damage from an explosion slash fire.
And as we were flying that bin and looking at the potential damage, we were also able to help that client determine how much grain was still on the bin from a volumetric standpoint, so that when the team showed up to do the bin cleaning, They knew exactly how much grain they had to contend with, where it was bridged up, and it really kind of opened our eyes and the client's eyes to determine what are we going to do with this grain once we get it all out, how much is still left in there, how much of it is burnt and or smoldering, and so it was a nice perspective to be able to do that zero human entry and drop down inside of there and see that there was a large wall of grain that was bridged up and could have potentially So we kind of learned something almost every time we use that. Our drones are a different perspective or different tool. So that's kind of fun and neat as well.
Kilger - 16:09
Yeah, definitely. And I have a hard enough time filming like an interview, concentrating on both talking and filming at the same time. So I can't imagine dangling in a silo and trying to catch good footage as well.
Wohlford - 16:22
So yeah, obviously safety is the number one piece of that and not having to worry about that anymore is great. Something that I failed to mention earlier is we have a secondary tablet that we bring with us that we can connect to the drone so the client or the engineer Can have a tablet in front of them as well, a little bit larger than like tablet that I have. So they're seeing things that they might ask me to go back and get a better picture of or get closer to. And that's kind of nice because trying to control the drone and get to where you need to be, has always been a tough challenge before the secondary tablet client was always looking over your shoulder. And much as I want to share that information with them too, I got to successfully make the flight and get the drone back up out of the silo as well. So. The secondary tablet was a great addition for us and our clients love it so that's been a great addition.
Kilger - 17:12
So it sounds like the tech out there has evolved even in the last couple of years since I've been in the industry. It's really exciting but is there anything else tech-wise that you see coming down the pipe that you maybe have your eye on?
Wohlford - 17:25
You know, as far as new technologies that are coming down the pipeline, we're always studying and going to different conventions and such. And you know, one of the things that it's not directly related to concrete repair, but a lot of our facilities that we work at have steel, either steel bends or steel tanks for bulk storage. One of the new technologies that's coming out that has our attention right now is the ultrasonic thickness testing of steel.
And so, although again that's not a new tool in the industry as far as being able to measure the thickness of a tank, what is new to our industry is that now an additional hub that you can add to the drone. So you don't have to have a boom left on site to do the precision measurement of a steel tank maybe 80 feet up in the air. You can deploy this drone and the drone has an arm that sticks out that has the gel capabilities and everything so it just performs a UT test right there on the steel tank. It's got a magnetized head.
Wohlford - 18:23
And allows you to take pinpoint measurements throughout that steel tank, if you will.
And if you do it on the inside of the tank, while the tank's empty, you can collect that LIDAR map that I talked about earlier all at the same time. So you can collect a 3D LIDAR map and do some precision testing on the inside of that steel tank.
And with every test that you take, you'll be able to pinpoint exactly what elevation, What location, was it the north wall, south wall? So that's kind of got us intrigued right now.
They just did a big launch in Switzerland on that technology and here in May, they're going to do some training on that in the States. So we're looking forward to getting our hands on that technology because oftentimes like I said, we have clients that either in the ethanol industry or Different aspects where they're doing bulk storage of some sort of material in these welded steel tanks. So we're looking forward to seeing what that has to offer for us and our clients.
Kilger - 19:20
Yeah, it sounds cool. You'll have to come back on when you get that technology in use and we'll be able to talk about it. So, if people want more information, where should they go?
Wohlford - 19:30
For more information on all the aspects of the repairs that we offer, the drone inspections, and GPR, you can go to our website which is ccsgrouponline.com and you can follow us on all our socials as well.
Kilger - 19:44
Yeah, and there will be a link to that in the description below. Thank you for joining me so much today.