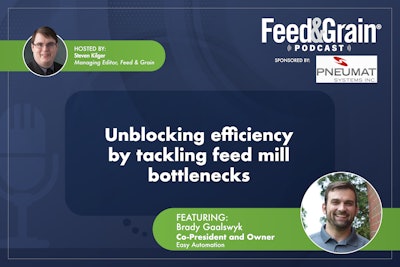
In this episode of the Feed & Grain Podcast, host Steven Kilger, managing editor of Feed & Grain Magazine, talks with Brady Gaalswyk, co-president and owner of Easy Automation. This episode dives into the practical challenges and solutions surrounding bottlenecks in feed facilities—a key issue that can lead to significant downtime and inefficiency.
Podcast sponsored by Pneumat Systems.
Transcript has been edited for clarity
Steven Kilger - 00:00 Hi, everyone. My name is Steven Kilger. I'm the managing editor for Feed & Grain Magazine and the host of the Feed & Grain. Thank you so much for joining me today. As we dive deep into the issues affecting the feed manufacturing, grain handling and allied industries.
Today’s episode is brought to you by The BinWhip from Pneumat Systems. The powerful Dual Impact BinWhip removes the toughest buildup and blockages in industrial storage silos – without hazardous silo entry. Learn more today at binwhip.com.
In today’s episode, my guest is Brady Gaalswyk, co-president and owner of Easy Automation, Inc. We're talking about bottlenecks in feed facilities and how discovering and fixing them can save hundreds of down hours at your mill. We talk about common bottlenecks, how to fix them once you do, and what they can cost a mill if left unchecked.
The interview if you want to help out with the podcast and are listening to this in a podcasting app please rate us and subscribe. If you're listening online sign up for the Feeding Grain newsletter industry watch to see the latest podcasts and stay up to date with all the news from around the industry. Now on to the show.
Hey Brady, thanks for talking to me today. For anyone on this call, you are a frequent guest of the Feeding Grain Podcast, and we thank you for that, you're one of our favorite guests. For anyone who doesn't know, can you tell me a little bit more about yourself and your involvement in the feed manufacturing industry?
Brady Gaalswyk - 01:21 You bet. So my name is Brady Gaalswyk, co-president and part of the second generation at Easy Automation, originally started by my father. We focus on automation in both the feed grain as well as agronomy areas, as well as providing software and equipment specifically to that feed mill sector.
Kilger - 01:38 Yeah, a family company, which is always nice to see. There aren't enough of them out there anymore. So it's nice to hear you're a second generation. We're here today to talk a bit about feed mill bottlenecks.
You guys had a really nice blog post on your website, which everyone should visit. I'll have a link to it in the description below where you talk a little bit about feed mill bottlenecks and how feed mills can go about diagnosing them and addressing them. Tell me some about the bottlenecks that you see that typically affect the efficiency and productivity in feedmills and preferably ones that, you know, can be overcome.
Gaalswyk - 02:11 Yeah, absolutely.
When you're looking at bottlenecks and So sometimes bottlenecks are very obvious. We're talking about the operator.
They would likely know that, yep, this is what I'm waiting on all the time, or I don't have enough load up in, or I'm always waiting on this, or I'm always waiting on that. Sometimes they can provide some real insight of their mill and their system. Other times though, and some of the easiest to fix, are those small things that is just very common to overlook when you're steering at your same mill day and Day after day, because a lot of times it's actually those 30 seconds, 20 seconds, 2 minute delays between things or delays or issues or problems that it's not significant enough for somebody that's living in it to think it's making a big deal.
Gaalswyk - 03:00 It's just kind of, yeah, this is how we do it. But those actually add up with so many different batches going through a mill. 10 seconds a batch, 30 seconds a batch truly can add up to hours per day. And ultimately days and days of unnecessary amount of production or overtime just because of those small little bottlenecks that are kind of flying to the radar.
Kilger - 03:21 Yeah, definitely. Especially because, well, everyone notices when your mill shuts down for two hours, right? Everyone knows that bottleneck, everyone sees that. But those day-to-day processes that you're just so used to doing every day, you don't even consider them. Do you have any examples of these? What are some of the common ones you might see out there at a feed mill?
Gaalswyk - 03:40 Yes, so some of the most common ones, I'll use more examples that I've seen out there that might not seem like a big deal but actually add up.
So one was simply where instead of stacking the orders one on top of each other for the automation to just simply go on to the next one, the operator felt more of a comfort in just releasing one order at a time and then coming back and releasing the next order because he wanted just to have that control.
Well through our reporting capabilities we actually reported the amount of time between orders and then total amount of time waiting and while it was only you know a lot of times 3 to 5 minutes per order, I think the average is like 4 minutes and 15 seconds between orders. It ended up that mail was waiting about 2 hours per day.
Because it was waiting on not knowing what the next order it was supposed to make. So just that small thing, you know, they got busy. Oh, I want to finish loading this truck before I start the next order. Where it ended up being, you know, a significant amount of time. Another was when you look at ingredient way up times and how can I speed up my mill and how can I make things faster.
A specific example, right, customer was waiting on the way up. And wanted it to be faster. I was watching it and saw that the bottleneck was that it was waiting on the microsystem. So we looked into it a little bit further and what had happened is that customer had replaced variable frequency drive VFD on the system and it's important to after you do that to then consult with the automation and what the settings were to have it run the most optimal so that it starts out at really fast high hertz and then as it gets closer it slows down and stops. It's going very slow at the very end to be accurate. Well they hadn't called in Wow, and those are both such small things.
Like, what do you want to think about it? You're like, oh, I'll just, you know, I'll start the new order for the batch, you know, not stacking them. That's just a human thing. Or like, oh, this is easier for me. How much time could it cost?
Kilger - 05:43 But breaking it down like that and realizing how much it is, and especially since those are both such easy things to fix.
Which I think a lot of people, when they think of bottlenecks, they think of kind of infrastructure layout or something along those lines, you know, big projects that are going to take a lot to improve.
So it's really, I don't want to say good to hear, but nice to hear that some of these can be fixed without big investments in equipment and things like that.
Gaalswyk - 06:11 You touched on Steven and just the importance of ensuring that your mill is running at its peak efficiency.
All the bottlenecks or all the little variations are fully evaluated and trying to improve because if there's that opportunity to gain 10%, 20%, 30% efficiency, well, you know, that could be significant dollars compared to creating a 30% bigger mill or having to build another mill or capital expenditures, but also as it relates to overtime and just the amount of efficiency run.
All those motors are probably running during all those hours that it didn't need to in just how much cost it's getting. So it's like a well-tuned machine, right? It's important to focus on instead of just getting bigger and better is what I have being fully optimized.
Kilger - 06:51 Yeah. And well, that's a good, the cost is a good thing to bring up too. Cause you know, you think about it as just not producing as much feed. As I could be but in reality you're running all those all that equipment you're losing money from the energy expenditure alone not to mention you know the lost man hours and all those other things so that's a really good point.
Gaalswyk - 07:10 Absolutely and like I said going back to that just to kind of walk through an example of that 30 seconds is lost per batch let's say right and this even multiplies if you're running for a 24 hour period That can be like two hours per day. Okay, that's a lot, but think about it. That's, if you run 24-7, that's 730 hours per year just because of those 30 seconds. It just keeps piling on itself.
Kilger - 07:34 That's insane. Are there any like warning signs that you see in feed mills that you visit that maybe an operator should be looking for that, you know, kind of indicate that things aren't going as efficiently as they should be?
Gaalswyk - 07:46 Yes. So, you know, at a high level, you know, make sure you're utilizing the reporting capabilities of your mill and your automation.
For us, for example, we have this what we call daily performance report where it prints out and shows what the productivity of the mill throughout the day, as well as It creates a graph showing what errors that the mill had, what events or problems that the mill had, and then, you know, list those in the area of most common to least common or how many times they happened.
Because again, it can be so common for managers, especially managers that have multiple mills, again, the operator is sitting there and they're clearing through the event and they're just kind of going to the next one and they're not quite sure. They just think that's the way it is. That's just how we make feed and how we get through the day.
But having that visibility allows the manager to then drive in and say, okay, this isn't an issue. Also the chart to show the efficiency throughout the day, you can have those conversations and see, okay, I see at 10 o'clock it dipped. Why is it dipper? I see every day at 10 o'clock it dips. Why is there productivity dipping? Well, there's a lot of different reasons where it could be a problem or maybe we're waiting on a truck to unload or all the load out bins are full.
Okay, well maybe that means we need to look closer at the schedule of our drivers and how we plan that out because the mill can only control so much and sometimes the trucks and the incoming trucks and the deliveries all have to dance together to truly optimize the efficiency.
Kilger - 09:11 You touch on one of the key parts of all this, which is automation, right? Automation can help reduce all of these bottlenecks. I mean, automation is really the key to efficiency in the future for feed mills. Can you give some examples of maybe some of these bottlenecks that automation can fix commonly find in feed mills?
Gaalswyk - 09:28 The biggest one is fair efficiency of the bottleneck is the ingredient way up time. If you are manually weighing up ingredients or even if it's electric, you know, pushing buttons and watching a scale and weighing up ingredients, an automation system can do it so much faster, even a single scale.
Not to mention the fact that automation can be weighing multiple scales, 5, 6, 7, 8, 9, 5, 6, 7, 8, 9, Plus scales up at a time whereas a best-case scenario is for an operator to do one at a time. So that's a huge one right there in just the feed.
Now I'll also even say on top of that there's the move from manual to automated but I will also want to say that it relates to automation you know now that automation has been around for quite some time can be older systems and older softwares that are not as fast as upgraded versions.
Simply upgrading the software, making sure your automation is up to date can have a significant aspect on ingredient weight at times. Another area that I see automation really helping is through the control of rolling and grinding systems. So it can be a common practice to have your rolling and grinding maybe is not the first thing you automate in an existing feed mill.
But by doing things such as automatic bin keep full, where the automation is looking at your ground bins, Making sure they're full, if they're not full, starting the system up to roll the grain and fill them all up, shut it off, shut things off in the proper order, and then watch again, see if the bins get empty to refill again.
While this can seem like not a big deal, a lot of times a mill's production and mill's rolling or grinding capacity are pretty tight neck and neck, where if operator isn't watching and keeping their bins ground A list of keywords. Grind the grain, the automation can be put in place to grind those bins full and then shut off in the proper order.
And during the time of operation, doing so in a manner that's safe for the equipment, safe for the facility, where if there was any problems or any issues with the hazard monitoring, it would shut it off in the proper order. So again, just those little things that might not seem like a big thing, keeping the bins full, right?
Pretty self-explanatory, but just get busy. It can be easy to get distracted and not stand up.
Kilger - 11:55 Yeah, very easy. I mean, that's what happens to all of us. Well, you made a really good point about when I think of going to automation, sometimes I think going from a turnkey facility.
The one that's automated, but you're right. Automation has now been around in the industry for decades. So for many people, you might have an automation system, but it now might be kind of outdated or not do what it can do.
How should feed mills kind of plan and execute transitions for more automated processes? Where do they find that kind of information? How do they know what's out there? Is there a good place to stay up to date?
Gaalswyk - 12:31 In a lot of ways, it is working with your automation provider. And I asked the question, hey, we want to automate more. What options are out there?
I do feel like trying to do a good job of educating their customers on what there is available. But at the same time, each of these mills are different. Each of them are customized to their own specific scenario. And maybe you're starting off at a different point of how automated they are.
Gaalswyk - 12:55 Maybe you have a different end goal of how automated they want to get to in varying budgets. So your automation provider can help work with what you have now, what they have available.
What makes the most sense or bang for their buck and how they can add that on. A lot of times, systems that may be putting only batching automation 20 years ago were adding more and more receiving automation, rolling and grinding automation, automation of loadout processes.
Another big area that we're automating more and more is pellet mills and pellet mill automation can be an area that starts off manual from a legacy system, but they want to add in over time. And a lot of these things can be added on relatively easy. To your existing automation platform, you will.
Gaalswyk - 13:36 It's not like you're having to start from scratch because it's just adding more and more on, pretty customizable.
Kilger - 13:42 Yeah. And it gives you all those benefits and not only more efficient processing, but also that data reporting you mentioned in the beginning, which is so key to finding the efficiencies in your plant. Just, you would never gather as much data as a machine.
Gaalswyk - 13:54 Absolutely. The other thing I want to touch on is relates to both bottlenecks as well as efficiency and automation is with the New generation of operators come in or the new generation of workforce, if you will, while maybe if you have an operator that's been around the system for 30 years, 40 years, you know, knows the system like the back of their hand, they are very good and very efficient and they don't have bottlenecks because they know that system like the back of their hand. However, now you get a next generation and they are younger generation, they're used to running computer systems, they're used to playing video games.
This concept of utilizing automation not only has them sit in the seat with a little training being very efficient use of the system right off the bat, but also just a more enjoyable work environment type of work that they want to do.
If there is any turnover, easier to train that next person in versus just relying on that individual's knowledge of the scenarios in their head and how to operate that system best. You're able to boil down all that information and knowledge into that automation.
Kilger - 14:58 Yeah. And the old age of, you know, the veteran knowing every single sound that a feed mill makes to make, make feed and have to go through and, you know, manually hit the pellet mill right here.
So it works right. I mean, those, those days are gone and for the better, I think, because by utilizing these systems, not only can you train people faster, you can also like move them around to your various facilities when you have shortages and all these other things.
So for those new people and even old employees, which just because you're operating a machine and you don't notice bottlenecks does not mean that you're doing it in the most efficient way possible. Those can be contrary ideas.
What kind of training programs would you recommend for employees in automated feedmills, both learning the software and then more important than I think a lot of people think, re-familiarizing yourself with the software out there once in a while.
You know, learning features that you don't use and all those kind of things. What kind of programs would you recommend for that?
Gaalswyk - 15:58 A lot of these facilities are so specific to their layout and specific to their facility that a lot of times it is working with the automation provider for that training programs. I mean, I know us here use automation.
It's pretty easy where we can either come on site to help with any training or any refreshers or have the people come to our facility to get a full demonstration mode and walk through things. Hopefully it's also very easy to provide our service and support.
We're able to directly log into your system, see your screen, see exactly what you're seeing, and walk you through on the phone of how you are running your system, how you flow through things, able to log in, make any adjustments to help tweak things.
So maybe if you're saying, hey, I feel like this isn't happening as fast as it should, or hey, I feel like this clean out of this conveyor is longer than it should, you can log in, help work through that. It's really truly a hand-holding approach because it's so specific to the facility and their application.
Kilger - 16:56 Yeah. What we do as editors is we always, when we do have meetings, we talk about these things too, right? And we discuss what we're doing versus the other employees. And that's part of it is just sharing ideas amongst themselves. So many people at Feedmills never talk to any other shifts or do anything like that.
Gaalswyk - 17:11 Absolutely. I think that's where the, you know, the value of reporting.
Can come in where especially if a manager or organization has multiple mills across their operation by having those data points and kind of creating that baseline it helps create those discussions where you know maybe one type of mills making a different type of feeder has a different size or different type of equipment that they'll never make as much feed but it helped drive those conversations of How one's being more consistent or how one's having less errors or once having less events helps drive those conversations and help point out those areas of opportunity.
I also have seen where that sometimes we have customers with multiple mills, you know, jump on a call and kind of talk through things. And it's incredible the amount of information that they share across the organization, where if you don't have create those spaces for opportunity, they kind of get stuck in your own little world.
Kilger - 18:04 Yeah, definitely. And even like you said, I mean, it's being able to See that four and a half minutes in between each batch at one plant and then seeing that doesn't happen the other and being able to ask why is it happening in this one but not this one so stuff like that it's really and that's the kind of thing that you can do with data gathering from automation that you can't really do just looking at stuff.
Gaalswyk - 18:25 Just standing there and feeling like it takes a long time doesn't help you gauge one compared to the other knowing that this mill average run timer is 40 seconds. And in this mill, the average runtime for that same ingredient, that same batch times is 80 seconds. Well, let's look into the why. Is there a setting wrong? Is the auger size wrong? Is the equipment size wrong? That's where that value of that reporting really shows up.
Kilger - 18:50 Yeah, more data should lead to more communication, not the opposite. How do you see the role of automation evolving in feedmills, particularly in addressing bottlenecks, but just also overall, what's the next big thing? Everyone's talking about AI.
Gaalswyk - 19:09 I've had a lot of data and automation for quite some time, but how to put that data into the users, the operators, the managers hands, In a way that they can actually make decisions off of it and actually change things, actually look into things because of it.
That is hard to get to, it doesn't get looked at, there's no decisions made off it. So a lot of that is in reporting tools and, you know, being able to visually see the data automatically is sent to you and that kind of thing. And then with the next step being AI.
So where can artificial intelligence is able to see some of those bottlenecks, give recommendations, give recommendations on How you're scheduling your loads, how you're scheduling your batches, essentially taking that data and doing a little bit like we've talked about just a little bit ago of how instead of that being conversations between mills, have that artificial intelligence be having that conversation or looking into it of what is a best practice and how can that be implemented here.
Kilger - 20:05 Yeah, definitely. Well, thank you so much for joining me today, Brady. I really appreciate it. Always love having you on. Like I said earlier, you have a great blog. You produce a lot of great content on your website and I'm jealous of it sometimes. I look at it and I'm like, oh, okay, they can't just write for Feed and Grain, huh? That's nice. But I would suggest anyone listening go check out some of the information you have on your website.
Gaalswyk - 20:29 Awesome. I appreciate that. Try to provide different types of insights. Obviously this is what we focus on and feel like we can provide some value to the discussion. So appreciate the opportunity to be podcast as well as just a part of the industry.
Kilger - 20:42 Yeah, happy to have you on, always am. We'll have you on again next year. I think that was about roughly the same time we had you on last year. So we'll have you on again. Thank you so much for talking to me today. Everyone have a great rest of your week and stay safe out there. Bye.