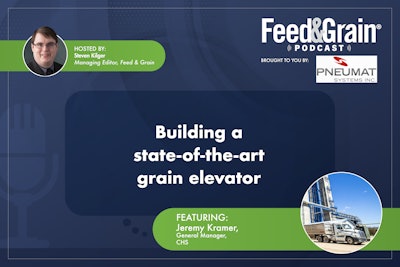
Join Steven Kilger, host of the Feed & Grain Podcast, in a compelling interview with Jeremy Kramer, General Manager of CHS. Discover the innovative journey behind the construction of a lights-out grain elevator in Herman, Minnesota, built amidst the challenges of the COVID-19 pandemic. From planning to execution, explore how CHS overcame construction hurdles, enhanced efficiency, and going from a 1970s model elevator into a state-of-the-art facility, setting new standards in the grain industry. Don't miss this exclusive episode offering insights into the future of grain handling and storage.
Transcript has been edited for clarity.
Steven Kilger: Hello, my name is Steven Kilger and I'm the managing editor of Feed & Grain magazine and the host of the Feed & Grain Podcast. Thank you so much for joining me today as we dive deep into the issues affecting the feed manufacturing, grain handling, and allied industries.
Today’s episode is brought to you by The BinWhip from Pneumat Systems. The powerful Dual Impact BinWhip removes the toughest buildup and blockages in industrial storage silos – without hazardous silo entry. Learn more today at BinWhip com.
So today I edited an interview that I did a while back with Jim Cramer, general manager of CHS about the grain elevator they built Herman, Minnesota. This grain elevator was pretty interesting because it was built via lights out facility. Plus it was built over the COVID-19 pandemic, which gave it whole bunch of construction challenges that they were able to overcome. It's a really neat story. So I'm really glad you're going to get to listen to it. Because this is an example of an interview that I would normally turn into cover story, but you'd end up getting such a small portion of what we actually talked about in that story. It's really nice that you guys will get to hear everything that we do.
Thank you so much for listening to the Feed & Grain Podcast. I hope you're having a great summer. And if you're listening to this in a podcasting app, please give us a review or rating. It really helps us out. If you prefer listening to this in your browser, make sure you sign up for Industry Watch, our newsletter. And we'll keep you up to date on all the newest podcasts that are coming out. With that out of the way, thank you for listening. Now onto the show.
Kilger: So why don't we kind of dive in, so can you guys go a little bit. go over kind of like the planning process of this elevator.
Jerry Kramer: The planning process, as far as building the whole facility?
Kilger: Right. Well, what brought you to the decision of like, this is the place to build. we, what, what, what was the need and how did you feel it?
Kramer: Sure. So, we have had an existing shuttle facility in the town of Herman for a long time. Quite honestly it was an elevator that we have retrofitted over the years, added some storage, added a second dump pit. But it was still, you know, a 1970s model elevator.
The scale was over the pit and anytime you have that, it typically is not as fast as the producer would like. So, we looked at different ways that we could retrofit further at the location in town. And we had, we owned some property just on the outside of town. We are about a mile north of Herman. We are still within city limits, but it is out on its own little parcel. And we have a 32,000-ton fertilizer plant here. And the main office is here. So, we had acreage to build new. And after we looked for a long time and hard at how to do something in town at the end of the day, it was going to be expensive, and we were going to really get what we always had. So, what this allowed us to do was start fresh and do it the right way.
So, we are about a mile from our existing shuttle. We built another shuttle that's state of the art and allowed us the speed that the, the farmer desires, along with adding space, because we are just. we could have used more upright space the way the, the producer takes the crop off these days. You know, one of the things that the producer is doing is they continue to invest in efficiencies, and that is both putting the crop in and taking the crop off. And so that is what the commercial. us in this case are, are trying to stay ahead of us. being able to make sure that we can get, you know, fertilizer to the ground ahead of the producer, as well as. stay ahead of, as we take, you know, corn and beans off in the fall of the year.
Kilger: I have noticed that it seems like, well, a lot of elevators are running into that situation too, like being in a downtown location, even if they were not once a part of town, the town was evolved around them. And so, you see a lot of. moves a little bit outside of it, just. more space, right. Especially traffic concerns and stuff like that.
Kramer: Yes. We bought fifty acres in about 2007 or eight. And so, we have this whole facility now. That is just exactly what you described. We've got some ability to sprawl here a little bit without getting too many things on top of us. Yeah.
Kilger: Yeah. that's, that seems to be the way that every, I mean, especially since now people are more and more, I don't know, anti-industry in their backyard.
Kramer: It seems sometimes so, yeah. It, it seems like. you know, the, the people that live in town, they don't want a lot of that truck traffic. No. And quite honestly, the producers do not want to have to fight around town with the truck traffic. Now Herman’s a town of about four hundred people. So, it's not a big city that we're trying to maneuver around.
Kilger: Yeah. Excellent. Can you go a little bit about into the kind of the planning of the construction phase?
Kramer: Okay. So CHS has its own construction department. Jim heads up that department. And so, I have worked with Jim for years now on, on various projects. So, we sat down and. worked through what we thought we needed for the, the project from a speed and space standpoint.
And. got my department. The rest of my department involved the, the grain guys inside the department and put together a plan. And then we took that to various contractors and. looked at, you know, what they had for thoughts around our plan. tweaked it toured a couple of other facilities that had recently built and. tweaked it some more. And that's how we came up with. the version that we ended up building. Nice. Yeah. , so. what kind of got you, what, what were your, what were the things that you knew you needed for this new facility? , okay. The first and the reason for it was, again, speed and space. , the producers just, he's so quick at taking the crop off and we just weren't able to do enough trucks per hour. And so we ended up, we'd have many days of long lines at the elevator just because we just couldn't get enough trucks through.
Kramer: And what this allowed us to do is now we've added three more dump pits. , and they're high speeds. So we're, we're, that's rated at 20 or. yeah, 25,000 bushels per hour per dump pit. And we've added three new dump pits. So just the new, yeah, just the new facilities rated at 75,000 an hour. And then we can dump another 25,000 bushels an hour at our uptown location. So, so. today, if you were able to evenly spread out your trucks throughout our facilities. in Herman, we'd be able to dump about a hundred thousand bushels an hour. Now that's what it's rated at. You physically can't get that many trucks through the whole system grading the grain and all that kind of stuff. Yeah, yeah, yeah. I, but what is, but it, it took us from two. a two dump pit location to a five dump pit location.