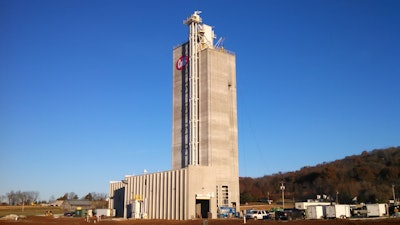
In the heart of one of America’s top chicken producing states lays every salmonella bacteria’s worst nightmare. It’s the newly built, state-of-the-art Cobb-Vantress, Inc. poultry feed mill located in Albany, KY. With advanced pathogen controls in place from incoming ingredients through feed load-out, salmonella and other bacteria face a veritable threat along every step of operations.
Features like airtight receiving pits, surgical-room-grade dust filters, the ability to heat treat its entire pelleting loop and a specialized feed trailer washing system demonstrate Cobb-Vantress’ dedication to stopping salmonella dead in its tracks.
Originally founded as Cobb’s Pedigreed Chicks in 1916, Cobb-Vantress, Inc. is the world’s oldest pedigree broiler breeding company. The brand known today was formed in 1986 as a joint venture between Tyson Foods, Inc. and The Upjohn Company. Tyson Foods, Inc. now owns 100% of Cobb’s stock, and Tyson continues to invest millions of dollars annually toward expanding Cobb’s pedigree breeding program — investments like the construction of the Albany mill, which serves Cobb’s two nearby complexes in Monticello, KY, and Lafayette, TN.
Until the Albany mill began feed production in early 2015, the complexes contracted from another supplier, in addition to receiving deliveries from Cobb’s Siloam Springs, AR, feed mill. But as Cobb’s director of nutrition, Dr. Chet Wiernusz, explained, the arrangement left room for improvement from a genetics and breeding standpoint.
“Our pedigree birds are the elite in our population because that’s where we make genetic progress,” Wiernusz started. “[Making progress doesn’t rely] as much on the nutrients themselves, but more on the level of consistent nutrients within the feed. We have to stay up with our competitors and give customers what they want, and we make faster progress by improving the consistency of the protein, fat and amino acid levels in our feed.”
If nutrient consistency is the expressed goal, then why so much emphasis on pathogen control? Because a disruption in Cobb’s feed supply from a salmonella outbreak would force it to find alternatives, which could have a detrimental effect on its breeding programs.
To avoid such interruption, in November 2013 engineering and construction firm Todd & Sargent Inc. began work on the Albany feed mill, and construction was completed by the end of 2014. The mill is capable of producing 3,000 tons of feed/80-hour week; however, mill manager Matt Ferguson currently produces about 2,000 tons/week on a 40-hour week schedule.
“The main emphasis is on producing quality, precise, pathogen-free feed — not producing the highest quantity per week,” Wiernusz said.
Designated areas
One special design feature is the Albany feed mill’s distinction between “clean” and “dirty” sides. Use of specialized equipment, designated clean areas controlled by airflow and other quality measures help ensure salmonella-free feed.
The dirty side starts at incoming ingredient receiving and ends once the treated feed is discharged from the pellet mill. The six-story mill’s clean side starts before the cooling process, where feed is sanitized, treated and kept separate in pressurized rooms from that point on.
Bob Chavis, project manager, Tyson Foods, Inc., said the two areas are kept separate from each other from the moment a truck enters the facility, thanks to a divided driveway that directs incoming ingredient trucks on one side and outgoing feed delivery trucks on the other.
Since salmonella travels easily through grain-dust filled air, controlled airflow and dust collection at critical control points help finish the job.
“Once the trucks come in with our ingredients, we open the door, they come into a pressurized receiving bay, and we close the airtightdoors, so all the dust will be contained in this room,” Chavis said. “We weigh the truck with our 10-foot by 70-foot scale, and then they begin unloading into our dump pits. A dustless pit system vacuums up the plume of dust produced while unloading.”
Mill designers made sure that personnel and ingredient suppliers pose little threat for cross-contamination.
“We installed a restroom for the [dirty] side to keep our receiving operator on the outside of the mill,” said Chavis. “It keeps all incoming truck drivers with ingredients separate from the mill, so we’re not crisscrossing traffic, having drivers and carriers bringing salmonella or other pathogens with them.”
But even with the precautions, the mill is designed to treat all incoming ingredients on the dirty side as though they’re positive for pathogens. After grinding and mixing, the pathogen treatment process begins with a 500-hp pellet mill with a “hot start” feature, pre-heating the feed before heading into the conditioner. The conditioner then treats the batch at 185 F for 45 seconds before dropping it into a 48-inch Hygenizer, where it holds the temperature at 185 F to 190 F for five minutes to kill bacteria and pathogens.
Pathogen growth prevention
Cobb-Vantress, Inc. and Tyson designed a revolutionary hot duct system to prevent bacteria growth in the pelleting system during periods of prolonged shutdown.
“All the moisture from when we shut down on the weekends provides a great place for salmonella and bacteria to grow,” Chavis started. “We’re taking boiler steam and using radiators with fans on them to duct hot air in to the mash bin, our conditioner and our whole pelleting system through the coolers and the pellet leg. This is something new in the United States.”
The air used for this control measure comes from the roof and first runs through a surgical-room-grade, 16 Hepa air filtration system. Then the clean, filtered air is heated up to 180 F before moving through and sanitizing all the equipment in the pelleting system loop.
Fleet sanitation
Another pathogen-control feature at the Albany feed mill is a high-temperature truck wash to disinfect their fleet of six delivery trucks.
“We’ve found once you have salmonella contamination, a truck is very hard to clean,” said Wiernusz. “So we use a heat treatment on all our trailers and trucks.”
After an initial washing, rinsing and drying, the trucks must sit for a number of hours before entering the specialized high-temperature, fully enclosed bay. A Tyson-developed control system brings the temperature from ambient to around 170 F to 180 F and holds it there for 20 to 25 minutes.
Hot air is forced into the compartment of the trailer where the feed body is heated, and at the end of the one-and-a-half-hour cycle, the truck is pumped with fresh air and brought back down to the ambient temperature.
Wiernusz remarked that the washing feature helps protect feed mills from what he sees as the biggest pathogen threat: recontamination.
“I think it’s relatively easy to clean the salmonella from feed, but recontaminating it when you’re cooling it down and allowing the dust from your raw materials to interact with your finished feed, that’s really the key,” Wiernusz said. “Recontamination can be the result of a mill not designed from a salmonella and pathogen control standpoint. Trying to modify their whole environment is difficult, so we took the opportunity to think of it from the start.”
Creative thinking from the design phase led Cobb-Vantress, Inc. to explore innovative applications like a pelleting loop sanitizer and a heat treatment truck wash. Added measures such as separate clean and dirty sides, carefully directed traffic, and critically placed dust control systems all combined to catapult Cobb-Vantress, Inc.’s Albany feed mill to the forefront in pathogen contamination control and prevention.
Home-grown Automation Enhancess Quality Control, Eases Record Keeping
While there are many reliable pelleting, mixing, batching and routing automation systems on the market today, the Cobb-Vantress, Inc. Albany, KY, mill took advantage of access to Tyson Foods, Inc.’s in-house developed TMCS (Total Mill Control System). Not only does it come with full load traceability and round-the-clock technical support, but it also eases record-keeping demands put on feed mills by the FDA and HACCP certification, while reducing human error.
For example, automatic locking lids on Cobb’s microingredient bins helps prevent operators from accidentally adding incorrect ingredients to a formula.
Bob Chavis, project manager for Tyson Foods, Inc. said, “The operator uses a scanner to scan the bar codes [on the ingredients]. The TMCS detects what ingredient was scanned and will only unlock that bin, so it’s extra quality control to assure there’s no cross-contamination.”
Beyond that, Cobb-Vantress’ mill manager Matt Ferguson is comforted knowing the TMCS provides full traceability of where their corn, soy and other ingredients came from, while also providing batch ID numbers and run-ID numbers for pelleting runs. The TMCS tracks which bin each run was assigned to all the way to load-out, and which farm the feed was delivered to. Ferguson noted that the ability to trace one step upstream and downstream the supply chain is a critical HACCP certification requirement.
Chavis listed personnel reduction as another advantage of Cobb’s TMCS. “The mill was designed for full automation: Even simple two-way valves are controlled by operators, allowing one person to control the entire mill.” The facilty employs only 15 people, including six truck drivers.
Equipment List | |
---|---|
SUPPLIER | EQUIPMENT |
Aircon Corp. | Cooler Cyclones, Ducting |
AIRLANCO (AGI) | Dust Filters |
APEC | Fat Coater |
Cleaver-Brooks | Boiler Equipment |
Conveyors, Inc. | Screw Conveyors |
CPM | Pellet Mill, Conditioner, Hygenizer, Steam Harness, Press Feeder |
Pellet Crumbler | |
Feed Cleaner | |
Geelen Counterflow | Pellet Cooler |
Hayes & Stolz Ind. Mfg. Co. LLC | Bucket Elevators |
Mixer | |
Distributors | |
Industrial Fabrication | 15,000-gallon Fats Tank |
Intersystems (Abel) | “Loss-in-Weight” Micro System |
Kaeser Compressors | Air Compressor, Dryer, etc. |
Memphis Scale Works, Inc. | Rice Lake Weighing Systems Truck Load out Scale |
Rice Lake Weighing Systems Truck Load out Scale | |
Mill Technology Co. | Hammermill |
New York Blower Co. | Fans |
Poly Processing Co. | #1500 8,000-gallon Alimet Tank/#1510 8,000-gallon Betaine Tank |
Schumacher Elevator Co. | (4)-Man x 1,000-pound Manlift |
Simpson Technologies | Pellet Mill Auto Lubrication System |
TRAMCO (AGI) | Drag Conveyor |