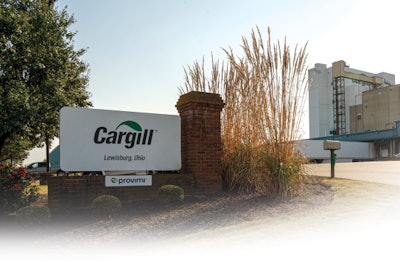
A step forward, state-of-the-art, the industry’s future ... all these things can be said about Cargill’s new feed premix facility in Lewisburg, OH. The $50 million facility features a 160-foot steel premix tower and 220,000 square feet of production space full of some of the most advanced technology in the industry. This new technology will create new standards for the premix industry and meet the evolving demands from consumers.
New standards
Adriano Marcon, president of Cargill’s animal nutrition business, says to adapt to changes in consumer preferences, the feed industry will need to set new standards of production. Consumers’ demand for their meat to be fed antibiotic- and animal-protein-free diets is rising, creating a valuable market for producers.
To capitalize on this market, producers will need to prove that they met consumer standards throughout the life cycle of that animal. They will need their feed company to trace their product and guarantee it’s pure. The need for purity and traceability has led Cargill to make each of its new premix facility’s four production lines animal-protein-free and antibiotic-free, allowing its customers to do the same.
“We supplement a significant part of the feed in the United States today, and we feel very responsible for the quality of what we produce,” explains Marcon. “We want to be in tune with consumers and their requirements to our customers, to the animal protein producers. There is a need to establish new production standards, especially enabling pork producers, poultry producers, milk and beef, to come up with products that meet different needs.”
Through its feed products and the premixes it sells to other feed manufacturers, Cargill’s impact on the feed industry motivated them to build a facility that would raise the standards of accuracy for the industry. To set those new standards, Cargill has embraced a bioefficacy concept.
“The bioefficacy concept means every nutritional compound that we use in our products is biologically active,” says Marcon. “The compound will do its job regardless of the feed processing temperature conditions or the mixture conditions that can attack vitamins. Our bioefficacy works. It starts with our supplier approval process, followed by our raw material approval process, and finally the premix production process.”
When designing its premix facility, Cargill drew on its experience building other premix facilities around the globe. The goal was to create a premix facility with the ultimate micro-dosing and blending precision.
“In the premix production process, what we do goes in parts per million level,” says Marcon. “Grams per metric ton are enough to nourish animals, or if not properly mixed, to become toxic to animals. This facility is designed based on our experience to deliver the ultimate mixing and dosing accuracy, to ensure that those parts per million are there for each ingredient.”
Cargill operates in 33 different countries, all with various regulations and needs. Marcon says this worked in Cargill’s favor, as it was able to bring in a global team of manufacturing specialists with experience in premix production.
“The team we gathered assessed the technologies we were using around the world, especially in our newer plants,” explains Marcon. “Using the experience we had and the technologies we implemented in Lewisburg, and working with our suppliers-partners to design newer standards, we established new error-proof mechanisms.”
Critical location
With a team assembled, Cargill needed a place to build and decided to continue its investment in southwest Ohio. The company had purchased a site in Lewisburg, where it already had a feed manufacturing operation.
“When we purchased the site, we were able to repurpose much of the basic infrastructure that was there, including a large warehouse and office space, instead of tearing it down to build a completely new plant,” says Mark Lueking, North America managing director of Cargill Animal Nutrition. “This reduced our use of resources in construction, as sustainability was a key objective for our design team. Lewisburg equips us to grow in the region, particularly with the increasing number of customers who require a non-medicated production environment. We consider Lewisburg an essential and critical location as it relates to animal nutrition for North America.”
Cargill is famous for its safety culture, and that extended to the construction of its premix facility. Lueking says the company worked with the construction and installation teams to ensure safety was the top priority. Safety became even more of a challenge during 2020 when the COVID-19 pandemic forced them to take extra precautions to ensure visitors to the site and Cargill’s team would stay safe and healthy.
“We were less concerned with getting this built on a timeline than the safety of our people,” explains Lueking. “The design team and the leadership on the ground did an excellent job of staying in close contact with the construction and the installation team, ensuring everything was moving along in a safe manner. Those teams also set the pace we were hoping for, and ultimately, ensured everything was installed correctly. Giving our customers peace of mind is one of the most critical things this plant allows — ensuring the integrity of the overall construction process and the installation process of this equipment was quite important.”
The perfect mix
The need for accurate, uncompromised premix manufacturing has driven Cargill throughout the planning, design and construction of its new facility. Technology and best practices have been built into the facility to ensure this is possible from an equipment standpoint and viable for the workers who will run the plant.
“We don’t want cross-contamination, mixes that are different than designed, so vertical design was very important to us,” explains Marcon. “Gravity flow is also better for the environment, giving the facility better dust collection, waste recycling and energy savings.”
The design of the plant is infused with technologies that help it achieve the perfect mix. According to Marcon, Cargill’s automated weighing dosing system automates 95% of the mass needed when producing premixes. The automated weighing dosing system pulls from 100 micro ingredient bins that sit at the top of the premix tower in a humidity- and temperature-controlled area. The facility also uses barcoding to remove human error. If a scanned barcode does not match the formula being created, the lids refuse to open until the correct ingredient is selected.
“Once the components of the mix are added, a checkpoint validates the weight,” explains Lueking. “If the weight is not correct, then there’s an alert for the employees to investigate, verify and correct the issue.
“In addition to ensuring accuracy, the highly automated production process, with continuous human monitoring, reduces the risk of injuries to employees,” he continues. “It gives that peace of mind — from the automation we have in place to the integrity of the product coming through the system.”
The quality control does not stop at the mixer. Once mixed, formulations pass through multiple checkpoints to ensure the accuracy of the individual weighments and the total batch content. The mix is then packaged into 50-pound bags or 2,000-pound super sacks and shipped to major food companies, feed mills and other Cargill locations.
“We must give our customers peace of mind,” says Lueking. “With the needs they have for animals at their locations and requirements they need to meet for their product, we have to take some of the stress and anxiety out of their hands and off their minds. We provide the peace of mind that the product they are receiving from Cargill is exactly what they requested for their animals.”
Cargill’s premix facility in Lewisburg, OH, may be the most advanced in the world, but the team at Cargill refuses to rest on its laurels. The team views every build as an opportunity to learn and grow for their business and their customers.
“We commit to being better every day here,” explains Lueking. “Today, we have to be better than we were yesterday, and tomorrow, we must be better again. It requires being humble.
“We need to learn from our experiences, good and bad, and make sure that we advance everything we do,” he says. “In terms of standards, this facility exceeds what’s required in Europe and the U.S., but we’re looking at our customer’s needs.
“It’s not about meeting regulatory standards so that this plant can operate in any part of the world. It’s about helping animals to express their productivity standard, and that’s why we focus on bioefficacy.” ■